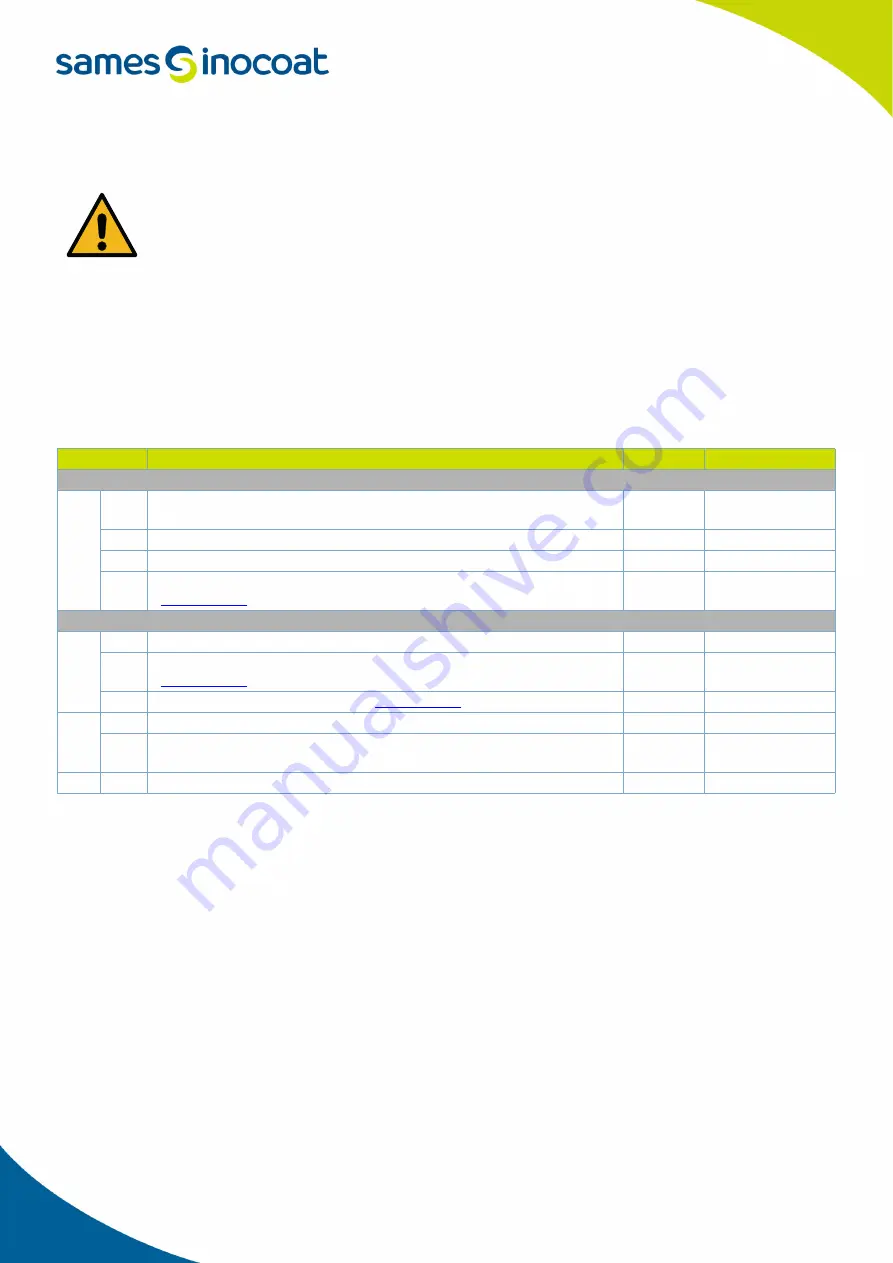
31
Member of Exel group
DRT7142
B - 2023/06
5. Maintenance
Before any intervention on the powder station, it is imperative to switch off the electrical and
pneumatic power supplies. After having cut off the pneumatic supply, it is imperative to empty
the air supply at the back of the powder plant by means of the safety valve. Pull on the ring
and the pressure drops.
5.1. Maintenance summary table
The soiling and wear of the different elements of the
Inocenter
powder station caused by the passage of the
powder depends on the nature of the powder and the operating conditions.
Therefore, the periodicity of maintenance indicated in the procedures below is only indicative. The user will have to
create his own maintenance range as he uses the
Sames
equipment.
Procedure
Detail
Duration
Frequency
Cleaning
A
A1
Checking the condition of the powder pumps
(injector, porous tube, ejector and sleeve valves)
10 min
Every 40 hours
of use
A2
Checking the condition of the cover seal of the tank
1 min
1 time per month
A3
Checking the condition of the sleeve valves
30 min
Every 3 months
A4
Checking the state of the transfer pump (sleeves and tubes)
(
-
-
Replacement
B
B1
Replacement of the vacuum generator
10 min
-
B2
Replacement of sleeves and porous tubes of the transfer pump
(
-
-
B3
Replacement of the transfer pump (
)
-
-
C
C1
Replacement of a powder pump
5 min
-
C2
Replacement of the ejector, injector, porous tube and sleeve valve of the
powder pump
10 min
-
D
D1
Replacement of the porous plate and flat seal on the tank bottom
-
-