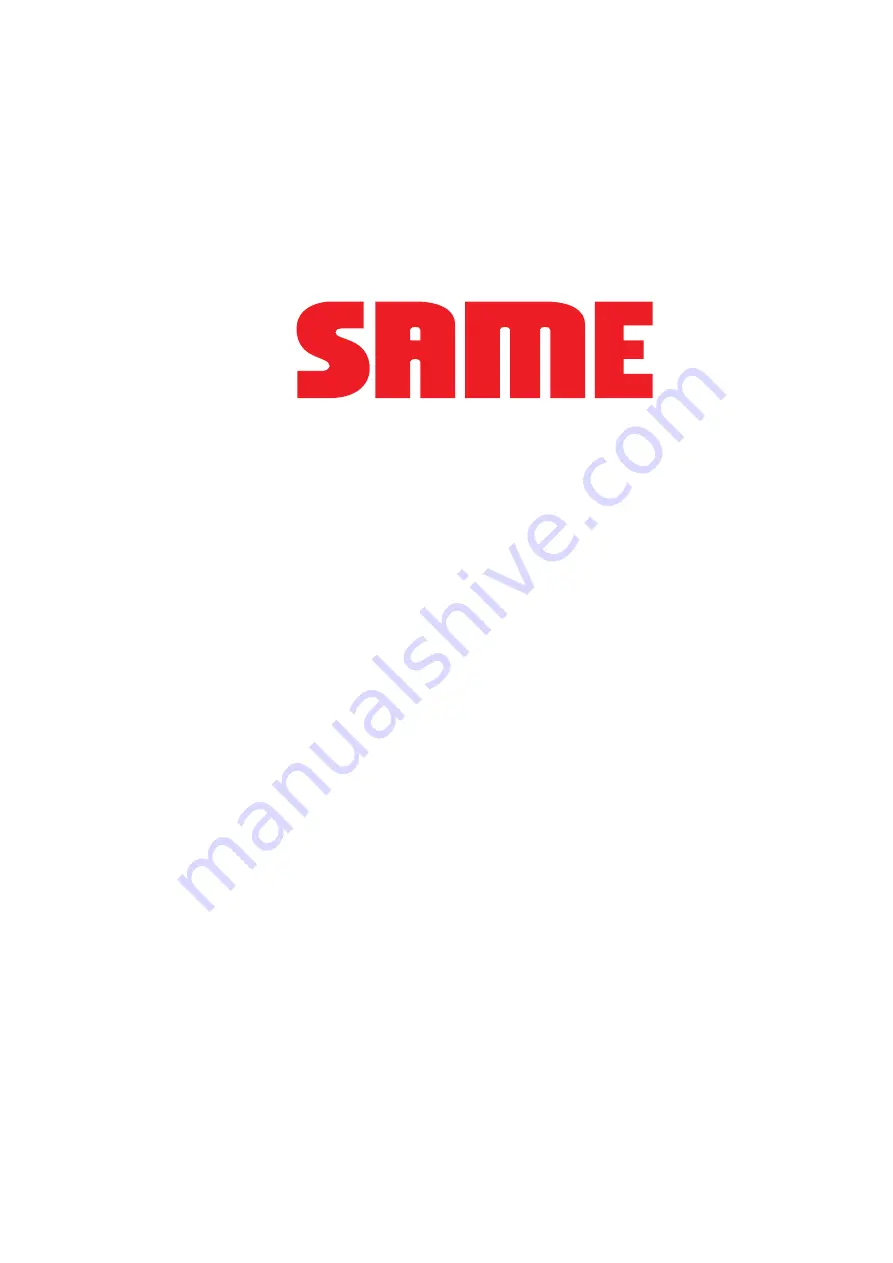
introduction
This publication is intended for the trained technician who must operate on our tractors.
It contains all general information relating to our tractor range, and in particular it highlights the inspection, overhauling
and adjustment procedures as well as the main instructions for dismantling and reassembling operations.
The workshop manual is a natural summary for the mechanic who has attended the vocational training and
specialization courses, which are held every year at our Service School, to permit him to perform a precise and qualified
work on tractor.
Its contents are therefore an exhaustive reference book for the experienced mechanic who desires to refresh his
memory on the sequence of the operations to be done. It is then good practice for every authorized dealer mechanic
to have at his disposal this publication, so that it may be consulted quickly when necessary.
We wish to thank in advance for the cooperation all thos people, who will let us have their suggestions in order to make
this publication more complete.
WORKSHOP MANUAL
SILVER 80
SILVER 90
SILVER 100.4
SILVER 100.6
Seat and headquarters:
V.le Ing. F. Cassani, 15
24047 Treviglio (BG)
Tel. 0363/4211
Telex: 311472 Samtra I
1
www.maskinisten.net
www.classicmachinery.net
Содержание SILVER 80
Страница 28: ...engine cylinders Fig 8 Engine cylinder 12 1 28 www maskinisten net www classicmachinery net...
Страница 30: ...engine crankshaft Fig 10 6 cylinder engine cranshaft 12 1 30 www maskinisten net www classicmachinery net...
Страница 223: ...Fig 23 SEPARATE BRAKES valve hydraulic systems vehicle brakes 54 5 223 www maskinisten net www classicmachinery net...
Страница 414: ...Fuse box system selectrical system 84 8 414 www maskinisten net www classicmachinery net...
Страница 419: ...CAB WIRING SHEET 1 CENTRAL WIRING 008 0610 4 40 419 www maskinisten net www classicmachinery net...
Страница 420: ...CAB WIRING SHEET 2 CENTRAL WIRING 008 0610 4 40 420 www maskinisten net www classicmachinery net...
Страница 421: ...CAB WIRING SHEET 2 A CENTRAL WIRING 008 0610 4 40 421 www maskinisten net www classicmachinery net...
Страница 422: ...422 www maskinisten net www classicmachinery net...
Страница 425: ...CAB WIRING SHEET 5 OVERHEAD WIRING 008 0400 3 10 425 www maskinisten net www classicmachinery net...
Страница 426: ...CAB WIRING SHEET 6 ELECTRIC HEATER WIRING 008 0403 3 20 426 www maskinisten net www classicmachinery net...
Страница 427: ...CAB WIRING SHEET 7 COLD CLIMATE ELECTRIC HEATER WIRING 007 6872 4 10 427 www maskinisten net www classicmachinery net...
Страница 428: ...CAB WIRING SHEET 8 S B A SYSTEM CONTROL SWITCH WIRING 007 6830 3 10 428 www maskinisten net www classicmachinery net...
Страница 429: ...CAB WIRING SHEET 9 ELECTRONIC LIFT WIRING 009 7712 4 40 429 www maskinisten net www classicmachinery net...
Страница 430: ...CAB WIRING SHEET 10 ELECTRONIC RPM CONTROL WIRING 009 7681 4 20 430 www maskinisten net www classicmachinery net...
Страница 432: ...CAB WIRING SHEET 12 H M L SHIFT CONTROL UNIT WIRING 007 6844 3 432 www maskinisten net www classicmachinery net...
Страница 435: ...PLATFORM WIRING SHEET 15 CENTRAL WIRING 009 6885 4 20 435 www maskinisten net www classicmachinery net...
Страница 439: ...PLATFORM WIRING SHEET 19 FRONT WORK LIGHTS 009 6887 3 439 www maskinisten net www classicmachinery net...
Страница 445: ...CHASSIS WIRING SHEET 25 STEERING ANGLE SENSOR WIRING 007 6847 3 20 445 www maskinisten net www classicmachinery net...
Страница 446: ...CHASSIS WIRING SHEET 26 DRAFT CONTROL SENSOR WIRING 009 3937 3 446 www maskinisten net www classicmachinery net...
Страница 448: ...CHASSIS WIRING SHEET 28 H M L SHIFT LEVER WIRING 008 0395 3 448 www maskinisten net www classicmachinery net...
Страница 449: ...Appendice 449 www maskinisten net www classicmachinery net...
Страница 453: ...NOTES 10 96 cod 307 1063 3 0 By Personal computing Documentazione Tecnica www maskinisten net www classicmachinery net...
Страница 454: ...www maskinisten net www classicmachinery net...
Страница 455: ...www maskinisten net www classicmachinery net...
Страница 456: ...307 1063 3 0 www maskinisten net www classicmachinery net...
Страница 460: ...Fig 2 HYDRIVE with minireduction IV 31 3 Transmission Hydrive www maskinisten net www classicmachinery net...
Страница 466: ...Fig 4 Hydrive X Transmission Hydrive 3 31 www maskinisten net www classicmachinery net...