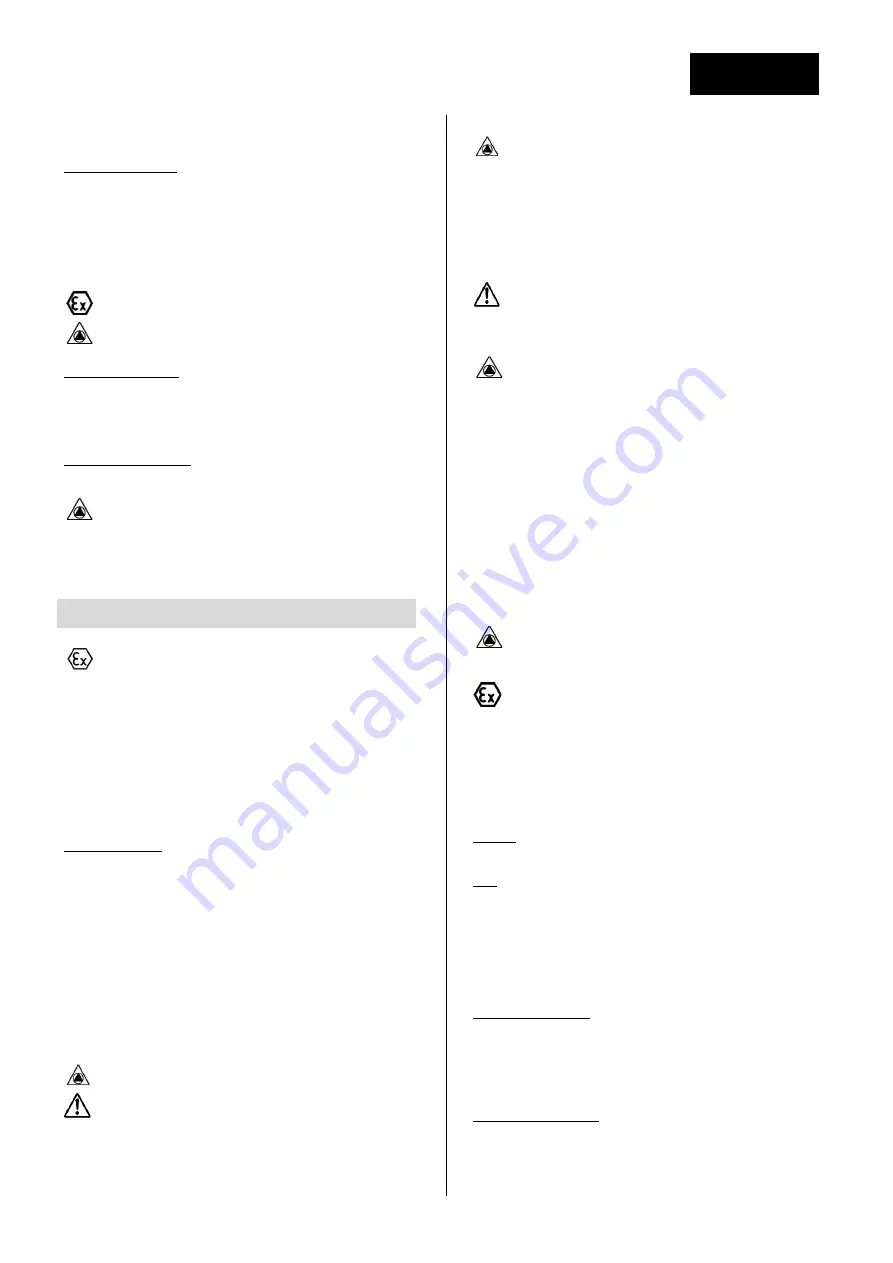
ENGLISH
15
required duty point on site. To ensure a reliable use of the equipment a
few precautions should be taken :
Electrical requirements :
Variable frequency drive will not generate voltage peak higher than
850V (motor phases isolation) and dU/dt values higher than 2500 V/µs
(winding isolation). If those values can be reached, a filter should be
installed : ask inverter manufacturer for proper selection and motor
manufacturer for limit values.
Choose a vector control inverter or use a quadratic V/F control
inverter.
Check that motor nominal voltage is never exceeded.
Power supply cable should comply to ATEX regulation. Ensure that
motor winding is equipped with CTP temperature sensors inside.
A physical barrier should separate power supply cables and low
voltage cables to avoid analog signal distortion.
Hydraulic requirements :
A dedicated suction pipe should be dedicated to each pump used with
a negative suction head (suction lift).
Check that the pump NPSH
R
at minimum speed is always lower than
system NPSH
A
.
Mechanical requirements :
Lower speed should not fall under 40% of pump nominal speed to
avoid any vibrations and an unstable flow.
The harmonic currents that are created by the VSD pass through
motor ball bearings. Standard ball bearings can be used up to
55KW. For higher installed power (see engraved power on motor name
plate), the motor should be equipped with isolated ball bearings
(specific ball bearing) or with isolated bearing housing (and standard ball
bearing).
8
START-UP
8.1
PRE-COMMISSIONING
If the pump is installed in a potentially explosive atmosphere or
when dangerous or polluting fluids are pumped, it is advised (Zone
2) or requested (zone 1) to install additional protection devices.
Check following points :
Pump flow is always higher than authorized continuous minimum flow,
Pump never runs dry,
Normal leakage of the shaft seal is controlled,
Surface temperature bearings housings is lower than the maximum
admissible surface temperature in selected ATEX zone,
Pressure on discharge side of the pump is lower than pump maximum
allowable working pressure.
Set alarm and stop trips of sensors.
In every cases check :
Quality of electrical connections,
Protection devices are installed,
Auxiliary piping are connected,
Flanges connections,
Suction line and pump casing are filled with fluid,
Motor direction of rotation is correct,
Coupling alignment is correct,
Oil level was checked and greasing of ball bearings has been done,
Coupling guard is installed.
8.2
FILLING / VENTING
Before the very first start-up, pump casing and suction line must be filled
with fluid (depending on piping system a vacuum pump may have to be
used).
Pump casing should be perfectly vented to avoid that the
mechanical seal runs dry.
Take precautionary measures when manipulating dangerous, hot,
cold or polluting fluids. Wearing individual protective devices is
necessary. The operator must known potential Hazards.
8.3
START-UP
If a barrier fluid, flushing fluid, cooling fluid or a heating fluid is
used, check that auxiliary systems are activated and working
correctly before pump start-up.
Close isolating valve on pump discharge side.
Open all valves in suction line.
Proceed to pump priming (if not already done). Pump casing and
suction pipe should be completely filled with fluid.
Turn the pump on and check discharge pressure increase. Compare
this pressure to the shutoff pressure available on the hydraulic curve
In order to avoid an important overheating of the liquid inside the
pump the pump should not work more than 20 to 30 seconds
against a closed discharge valve.
If expected pressure is reached then progressively open the discharge
valve.
If there is no liquid delivered or if discharge pressure is too low
then see chapter “trouble shooting”.
8.4
RUNNING CHECKS
During operation of pump in duty conditions (capacity, head,
temperature, …) the following points must be checked :
Check and note pump duty point. If necessary convert pressure value
from bar indicated on the pressure gauge to mwc :
HMT
mce
= (P
bar
x 100) / (SG x 9,806) with SG= fluid Specific Gravity.
Check and note current consumption on each phase of the motor.
Check calibration of motor protections.
Check temperature of ball bearings (on bearing housing surface).
Check flexible coupling alignment after several pump starts (only for
concerned pumps variants).
Check tightening of flanges fastening bolts.
Check there is no leakage and no abnormal running noise.
When pumping hot fluids, the definitive coupling alignment should
be done only when system nominal temperature is reached and
stabilized. See chapter 7.1.4 COUPLING ALIGNMENT
Check the surface temperature on the bearing bracket and on the
pump casing. Check pumped fluid temperature. Alarm and stop
trips settings should be done according those values. Refer to specific
sensors IOM before adjusting those trips.
If an external flushing, quench or an external heating is installed, the
following points should be checked :
External flushing
:
Check flushing pressure and compare with following maximum values :
Pressure :
For impeller diameter 125 : P
suction
+ 0,5 bar
Other impeller diameters : P
suction
+ P
differential
+ 0,5 bar
Flow :
Delivered flow should be between 0,1 and 0,2 m
3
/h
Quench
:
Max Pressure = 4 bar
Heating
:
Max pressure = 4 bar with water vapor at 140°C
Gland packing assembly :
A small leakage of packing gland is necessary to ensure proper
lubrication of the packing rings (20 to 40 drops per minute is
acceptable). If there is not enough leakage then packing ring will be
destroyed rapidly. Check that the external liquid supply of the gland
packing is turned on before starting-up the pump (if applicable).
Mechanical seal assembly :
For pumps equipped with a quench, external flushing, or a heating
system, check that the external liquid supply is turned on before
starting-up the pump. In any case the mechanical seal should have time
to cool down between two starts.
Содержание NEX
Страница 2: ......
Страница 27: ...FRAN AIS 27 12 1 1 PLAN EN COUPE Roue ouverte Roue aubes invers es...
Страница 29: ...FRAN AIS 29 13 DECLARATION CE...
Страница 30: ...FRAN AIS 30...
Страница 53: ...ENGLISH 25 12 1 1 SECTIONAL DRAWING Open impeller Reverse vane impeller...
Страница 55: ...ENGLISH 27 13 EC DECLARATION OF CONFORMITY...
Страница 56: ...ENGLISH 28...
Страница 59: ...5 1 1 1 2 2 1 2 2 SALMSON 2 3 2 4 2 4 1 25 68 5 C 2 4 2...
Страница 60: ...6 2 5 2 6 Salmson 2 7 2 8 2 9 ATEX...
Страница 62: ...8 2 9 7 2 9 8 2 9 9 3 3 1 3 2 3 3...
Страница 63: ...9 6 Salmson 3 4 25 3 4 1 4 NEX 5 5 1 NEX...
Страница 69: ...15 0 4 7 1 2 1 2 3 1 2 3 4 5 6 7 8 7 1 3 7 1 4 0 2 1...
Страница 70: ...16 Parallel Angular 7 2 7 2 1 7 2 2 L 2 3 7 2 3...
Страница 71: ...17 8 10 2 NPSHR NPSHA 7 2 4 3 3 10 0 35 2 0 7 7 3 230 400 400 400 690 690 60079 14...
Страница 72: ...18 7 3 1 Y 230 400 400 690 7 3 2 U 7 3 3 U 3 7 3 4 7 4 850 dU dt 2500 ATEX NPSHR NPSHA...
Страница 73: ...19 40 55 8 8 1 2 1 8 2 8 3 1 2 3 4 20 30 5 8 4 HMT P 100 SG 9 806 SG 7 1 4...
Страница 74: ...20 125 P 0 5 P P 0 5 0 1 0 2 3 4 4 140 20 40 8 5 Salmson 9 9 1 9 2...
Страница 86: ...32 11 12 12 1 12 1 1...
Страница 89: ...35 13...