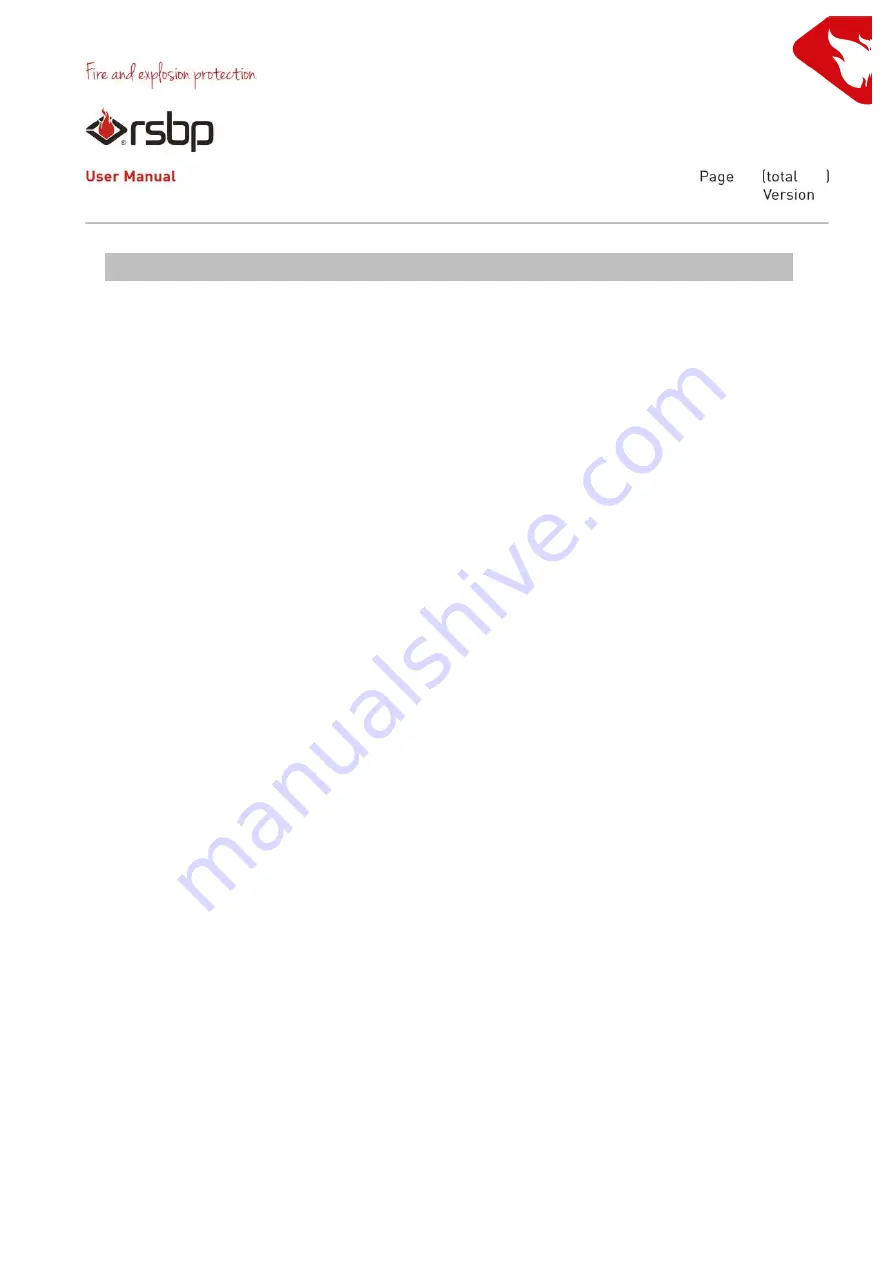
Flameless Explosion Venting Device
–
FLEX
25
35
1
6. OPERATORS, M AINTEN ANCE, AND ST AFF TR AINING
The device can be operated only by the person who is physically and mentally capable and
who has been demonstrably trained in this activity. Under normal operating conditions, there
is no risk of electric shock or heat injury.
The maintenance interval performed by the operator must be specified on the basis of
operating conditions for the given technology, in particular on the basis of the overall dust
nuisance. It is recommended that the following procedure is observed:
1. maintenance
2 weeks after commissioning
2. maintenance
6 weeks after commissioning
3. maintenance
8 weeks after commissioning
Based on the identified operational data (the clogging rate of the flame filter meshes and
other), the customer shall specify the FLEX maintenance interval (for example once a
month). The lowest maintenance frequency is once a year. Each maintenance must be
recorded in the operation log book, highlighting the information on the date and time of the
respective maintenance activity. Furthermore, it must be indicated whether the activity was
inspection, maintenance, change or repair, or what exactly was done with FLEX and why.
Last but not least, the name of the worker who performed the operation and his/her signature
must be indicated.
The FLEX maintenance consists in the following steps:
1) Check for any mechanical damage to FLEX.
2) Check of FLEX cleanliness. The flame filter meshes must be maintained in a
perfectly clean condition; no dust or other dirt may stick on the surface or inside the
FLEX device. Therefore, the meshes must be cleaned using an industrial vacuum
cleaner and/or mechanical means (a dry cloth, broom or others) within each
maintenance. If the FLEX is fitted with a protective bag, the bag must also be cleaned
from dust and dirt regularly. The bag can also be washed.
3) For the rectangular FLEX devices (of the F and R series), the membrane integrity can
be checked through the inspection hole. After the inspection and possible cleaning of
dirt, the hole must be thoroughly sealed using the inspection hole gasket. In the event
of damage, the new one can be ordered from the manufacturer. The original cover
(lid) of the inspection hole and the original fasteners, a self-locking nut (ISO 7040,
property class 8) and the plain washer (ISO 7090), both galvanized, should be used
for covering the hole. In the event of loss, you can replace the fasteners with the new
ones; for the FLEX devices of the F series and the FLEX device R1, they include the
nuts and washers M6, for FLEX R2, R3 and R4 M8. The M6 nuts must be tightened