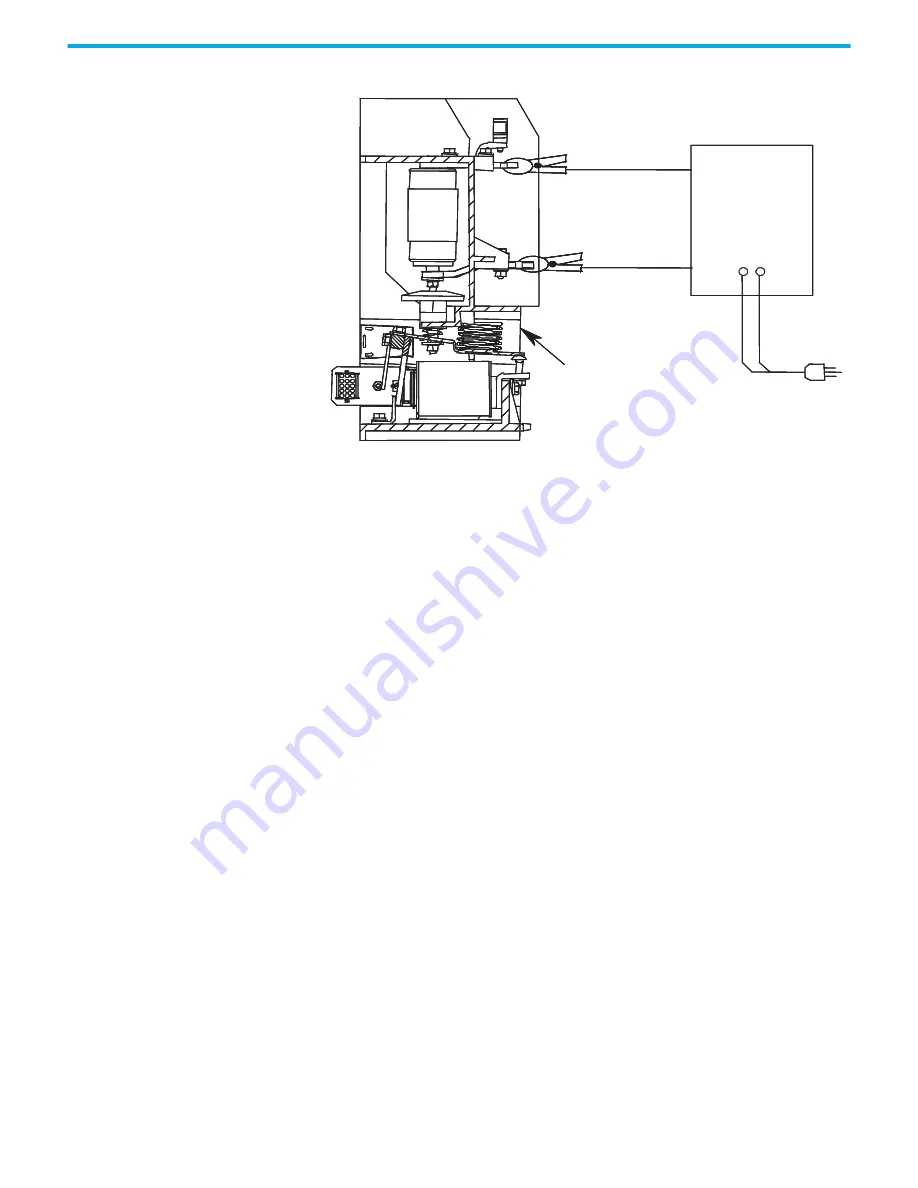
Rockwell Automation Publication 1502-UM060A-EN-P - October 2020
19
Chapter 2 Receiving and Handling
Figure 5 - Vacuum Bottle Integrity Test Circuit
The allowable leakage current value of 5 mA is exclusive of leakage due to test
equipment leads. The test setup leakage can be determined by running the
dielectric test with test leads not connected to the contactor and noting the
maximum leakage current. If this value is more than 2 mA, it must be added to
the 5 mA limit when testing the vacuum bottles.
Rockwell Automation does not recommend a DC Hi-pot test. The values that
are obtained during the test are not a reliable indication of vacuum bottle
integrity. An AC test provides a reliable vacuum integrity indication.
Additionally, the degree of vacuum within the bottle can be determined by
comparing initial test results to the present readings. Increases in leakage
current indicate a reduction in vacuum within the vacuum bottle.
Storage
To store the contactor before it is in service, store it in a clean, dry area, free
from dust and condensation. Do not store contactor outdoors.
Storage temperature must be between -20…+65
°
C (-4…+149
°
F). If storage
temperature fluctuates or if humidity exceeds 85%, use space heaters to
prevent condensation.
Insulation Resistance Test
Use a 1000V insulation resistance tester to verify that the resistance from
phase-to-phase or from phase-to-ground is greater than 500 megohms.
Vacuum Contactor
in Open Position
Vacuum
Checker
Содержание Allen-Bradley G Series
Страница 1: ...Medium Voltage 450 A Contactor Series G Bulletin Number 1502 User Manual Original Instructions ...
Страница 6: ...6 Rockwell Automation Publication 1502 UM060A EN P October 2020 Notes ...
Страница 16: ...16 Rockwell Automation Publication 1502 UM060A EN P October 2020 Chapter 1 Product Description Notes ...
Страница 20: ...20 Rockwell Automation Publication 1502 UM060A EN P October 2020 Chapter 2 Receiving and Handling Notes ...
Страница 48: ...48 Rockwell Automation Publication 1502 UM060A EN P October 2020 Chapter 4 Maintenance Notes ...
Страница 50: ...50 Rockwell Automation Publication 1502 UM060A EN P October 2020 Chapter 5 Troubleshooting Notes ...