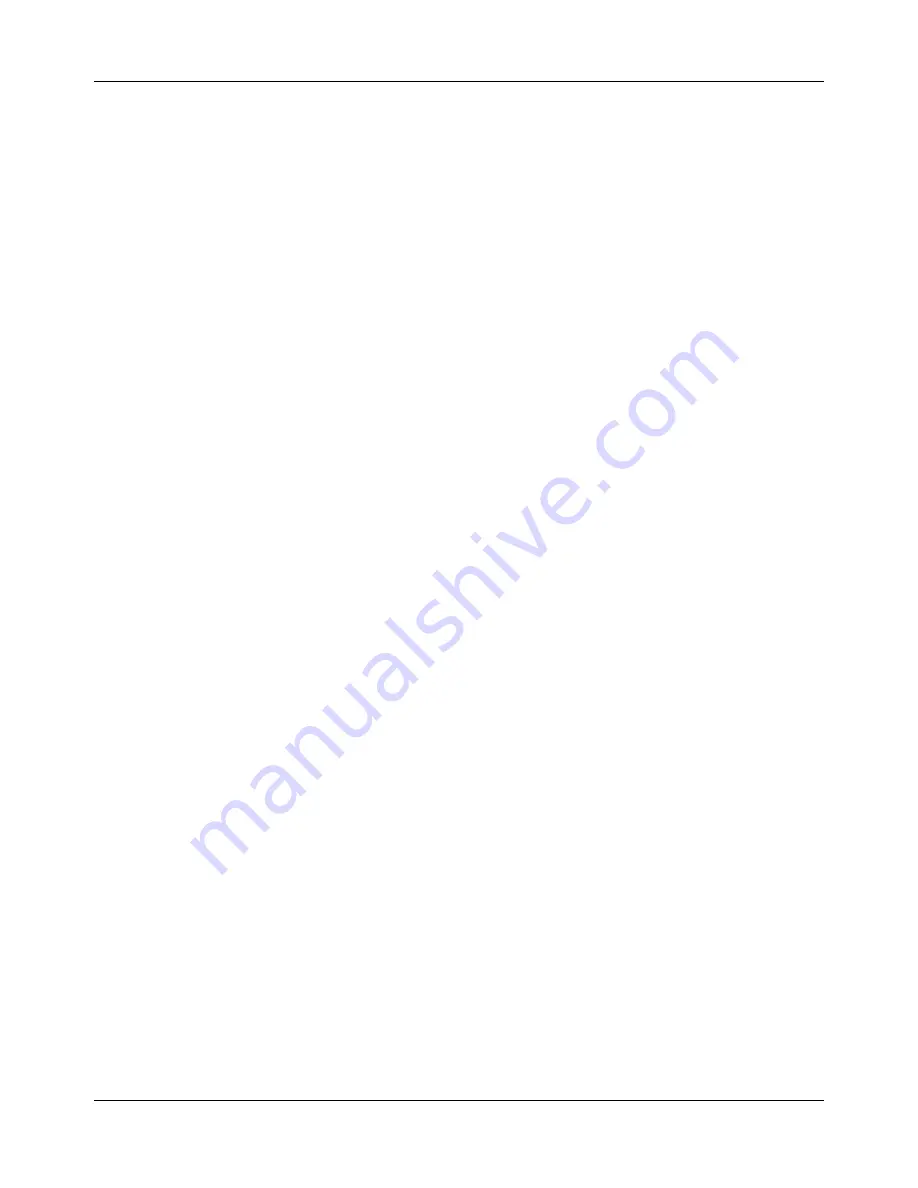
Operation
Theory of Operation
QuickStick HT User Manual
231
Rockwell Automation Publication MMI-UM007F-EN-P - September 2020
•
The vehicle master uses the position of the most recently acquired block far-
thest from the vehicle as an interim destination (target) to calculate the next
profile setpoint (P
set
, V
set
, and A
set
).
•
The vehicle master handles all collision avoidance to make sure brick-wall
headway is maintained between vehicles.
5.
The vehicle master uses the profile setpoints as inputs to control the vehicle position.
During the move, vehicle data such as actual position, velocity, and interim destination
are sent back to the node controller, typically every 100–200 ms. This data provides
the host controller some level of feedback as to where the vehicle is located.
6.
The vehicle master continues to generate updated motion profiles that are based on the
order and vehicle control continues based on the new profile setpoints. This updating
continues until the vehicle is handed off to the next vehicle master or it reaches its des-
tination.
The vehicle master hands-off vehicle control to the motor drive for the next motor as
the vehicle moves across motor boundaries. The new vehicle master ‘picks up’ where
the old one left off for profile generation. The new vehicle master is now responsible
to continue the closed-loop control of the vehicle.
7.
The motion order is finished when the vehicle position is equal to the ordered destina-
tion.
Motor Cogging
Brushless Permanent Magnet (BPM) motors that are iron core-based inherently exhibit cog-
ging forces. In traditional BPM motors, these cogging forces are felt when turning the shaft of
the motor and are periodic in nature. The periodicity in this case would be expressed in
degrees and the magnitude and direction of this cogging force would vary as a function of
shaft position.
Linear motors, such as the QuickStick HT motors from MagneMotion that use an iron core to
maximize thrust (equivalent to torque in a traditional rotary motor) also exhibit cogging
forces. The main difference between rotary motors and linear motors is that in linear motors
these forces are periodic as a function of distance versus angle. In the linear motor, these
forces tend to pull the vehicle forward or backward at specified intervals along the motor.
The QSHT motors are designed to minimize cogging as the vehicles travel over the motor.
Vehicles are subjected to slightly greater cogging as they travel from motor to motor. The fre-
quency of these cogging forces is directly proportional to vehicle speed. Cogging forces are
below 5% of the available thrust that is provided by the motors and do not appreciably impact
the acceleration and speed capabilities of the motors. However, cogging can lead to percepti-
ble low-level vibrations whose frequency are related to vehicle speed. These small vibrations
have a typical frequency range of 0 Hz (at zero speed) to 30 Hz (at high vehicle speeds).
Содержание 700-1384-01
Страница 334: ...334 MagneMotion Rockwell Automation Publication MMI UM007F EN P September 2020 This page intentionally left blank...
Страница 342: ...342 MagneMotion Rockwell Automation Publication MMI UM007F EN P September 2020 This page intentionally left blank...
Страница 343: ...QuickStick HT User Manual 343 Rockwell Automation Publication MMI UM007F EN P September 2020 Notes...