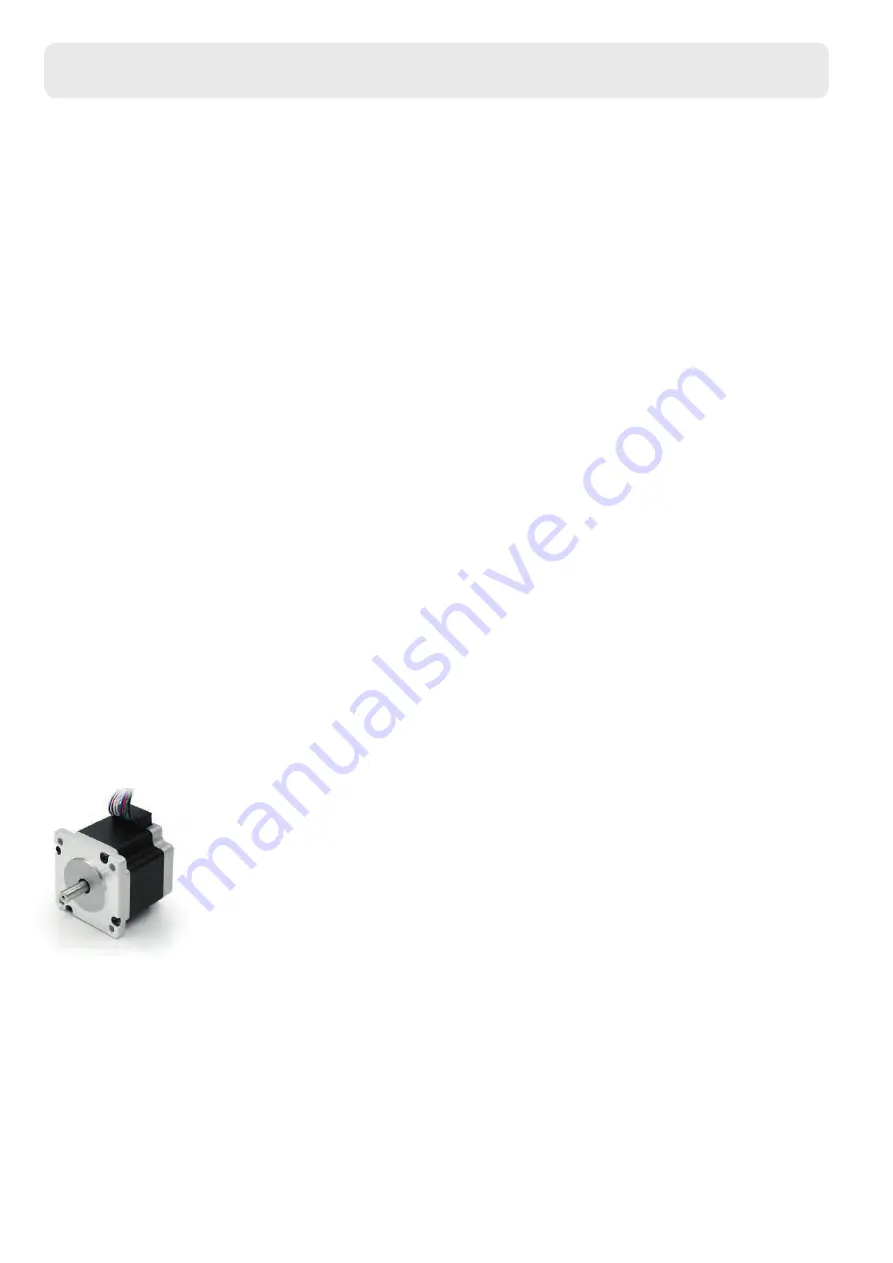
14
AXLE DRIVES
●
Drive motors must be mounted on the X and Z axes.
●
In order to be able to move the axes, the installed threaded spindles must be moved using
stepper or servo motors. These are available in various sizes which must be selected to suit
the machine.
●
Stepper motors or so-called hybrid servo motors, or also „closed-loop stepper motors“
are recommended. Genuine AC or DC servo motors can also be used, but often have the
disadvantage that they are more expensive and are designed for high speeds, which are
rarely used during operation on the ELS. Hybrid stepper motors are therefore ideal for
operation with the ELS because they drive more safely and generate more power thanks to
position feedback.
●
The motor systems almost always consist of a motor and a suitable output stage, also called
driver. This output stage receives the drive signals from the ELS and converts them into
current signals for the motor. The power amplifiers need their own power supply.
●
The ELS outputs 5V step and direction signals at the outputs. You can use any type of motor
that can be operated with these signals, most systems fall under this category. Examples are
all stepper motor and servo output stages from Leadshine or identical.
●
We recommend the direct connection or a 1:1 connection via toothed belt. Transmission
ratios reduce the maximum feed rate, but increase the torque.
●
Step rate: The maximum step rate of the ELS depends on the encoder pulses. It is therefore
naturally limited. We recommend setting the motor output stages of the Z axis to 400 or 800
steps/revolution. The output stage of the X-axis can be set to 800 - 1600, depending on the
thread pitch of the spindle.
We recommend mounting a hybrid servo motor (closed-loop stepper motor) on the Z axis and
a stepper motor on the X axis.
Stepper motors are special motors which are able to carry out a rotation in
200 defined steps. These motors are driven by stepper motor drivers or out
-
put stages which convert the weak control signals into current for the motor
coils and thus drive the motors.
Servomotors have a slightly different design, all have in common the fact
that they have a device that reports the position of the motor, a feedback
that allows the motor to be precisely controlled to a certain position. Servo motors achieve
higher speeds than stepper motors, but together with the control electronics they are much
more expensive than stepper motors. Since we do not need very high speeds for the ELS, it is
sufficient in most cases to fall back on stepper motors. Servomotors also often require more
than 800 steps per revolution, which is too much for operation with the ELS.
A middle way is the new hybrid servo motors, i.e. stepper motors with position feedback, so-
called closed-loop systems. These have higher torques than normal stepper motors and are
equipped with feedback. The matching output stages are also able to adjust the position be-
tween the steps, which leads to very precise drives. And the best thing is: step losses are exclud-
Содержание ELS 4 Basic
Страница 2: ......
Страница 23: ...21 ...
Страница 59: ...57 ...
Страница 63: ...61 ...
Страница 96: ...Zeroing is done as follows Possible grooves 94 ...