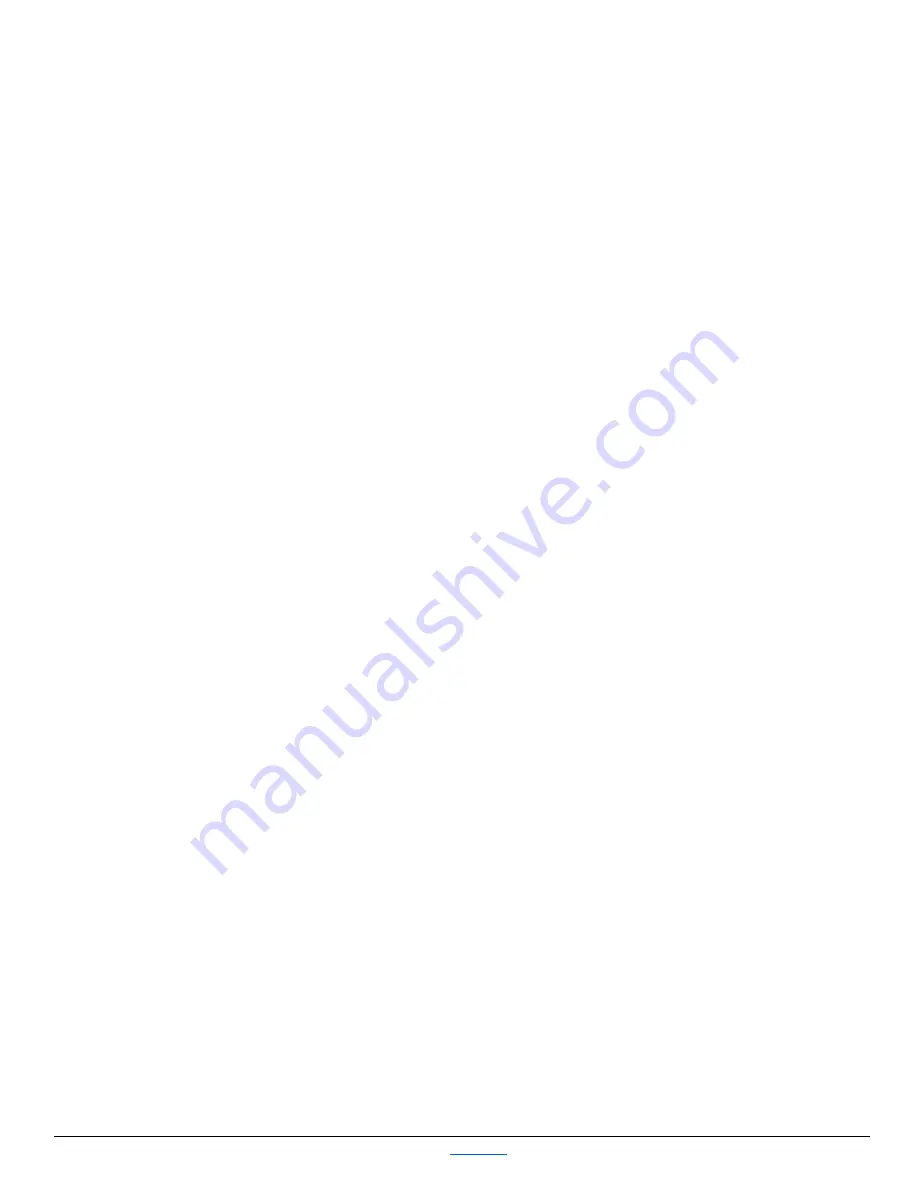
Robo-Tank DIY ATO System
User Manual – Page 6
2. How the ATO Operates
The ATO is ready to use out of the box however there are some settings you can fine-tune which are explained on the
following pages.
By default 3 of the 4 ports are being used for the ATO function, these are Sensor ports 1 and 2 and the Backup port.
Sensor port 3 is setup to monitor the level in the reservoir however you can allocate this as another backup for the ATO
function if you prefer (see page 11) and refer to “10. Adjusting the Advanced Settings” to adjust the setting.
The ATO ships setup to automatically calculate a maximum allowable run-time which is updated after every successful
top off and averaged over the past 4 top offs. It takes 4 complete cycles for this feature to activate until the manual max
run-time setting is used which is 5 minutes by default but can also manually set your own max run-time and disable the
auto calculate feature.
When using the auto calculated max run-time it’s highly recommended to use optical sensors for the ATO function with
the included mounting bracket. These sensors are highly accurate operating in an approximate 1mm window, the
spacing between the sensors is 4mm which is important for the calculated max run-time to function as intended.
If your ATO sensors are not optical you should turn off the auto calculate feature and use the default 5 minute max run-
time or manually adjust it to your needs.
Sensor 1 is the primary sensor and switches the ATO on and off
If Sensor 1 fails to switch off the ATO, water will rise to Sensor 2 which should switch it off (water level will have
rose approximately 4mm above normal top off scenario)
If Sensor 2 switches off the ATO it will now control the ATO taking the place of the primary sensor.
If Sensor 3 isn’t used for the ATO and water goes above Sensor 2 the maximum run-time will kick in and switch
the ATO off (water level will have rose approximately 9mm above normal top off scenario)
If Sensor 3 is used for the ATO and Sensor 2 fails to switch off the ATO water will rise to Sensor 3 which should
switch if off (water level will have rose approximately 8mm above normal top off scenario)
If Sensor 3 fails to switch off the ATO the maximum run-time will kick in and switch the ATO off (water level will
have rose approximately 13mm above normal top off scenario)
If the maximum run-time switches off the ATO it will remain off until the ATO has been reset or if one of the
sensors reports a high water level
If water reaches the emergency backup float switch the power is cut to the pump in a way that bypasses the
code and electronics making it a true fail safe (water level will have rose approximately 18-20mm above normal
top scenario)
There’s an additional timer that starts when the pump turns on and will turn switch the ATO off if its active for
more than 10 minutes
The ATO can only run once during a 60 minute period
Sensor 1 has an adjustable start delay (5 second default) and 1 second stop delay, this allows the sensor to
stabilize before switching the ATO, the backup sensors respond in real time
ATO is switched off immediately when an alarm triggers however the actual alarm is suppressed until the
adjustable alarm delay has expired, if all sensors report good conditions beforehand the alarm will not sound
The ATO system is also equipped to monitor the energy consumption of your DC pump which is useful to detect any issues
with the water pump. This requires a about a day to be auto enable, once it does the alarm will sound if the pump isn’t
operating in its normal state so you know to clean or replace your pump before it quits completely. If you replace your
water pump simply unplug the power to the ATO module and power back up and the training session will start over. The
ATO will continue to function until the maximum run-time shuts down the system.