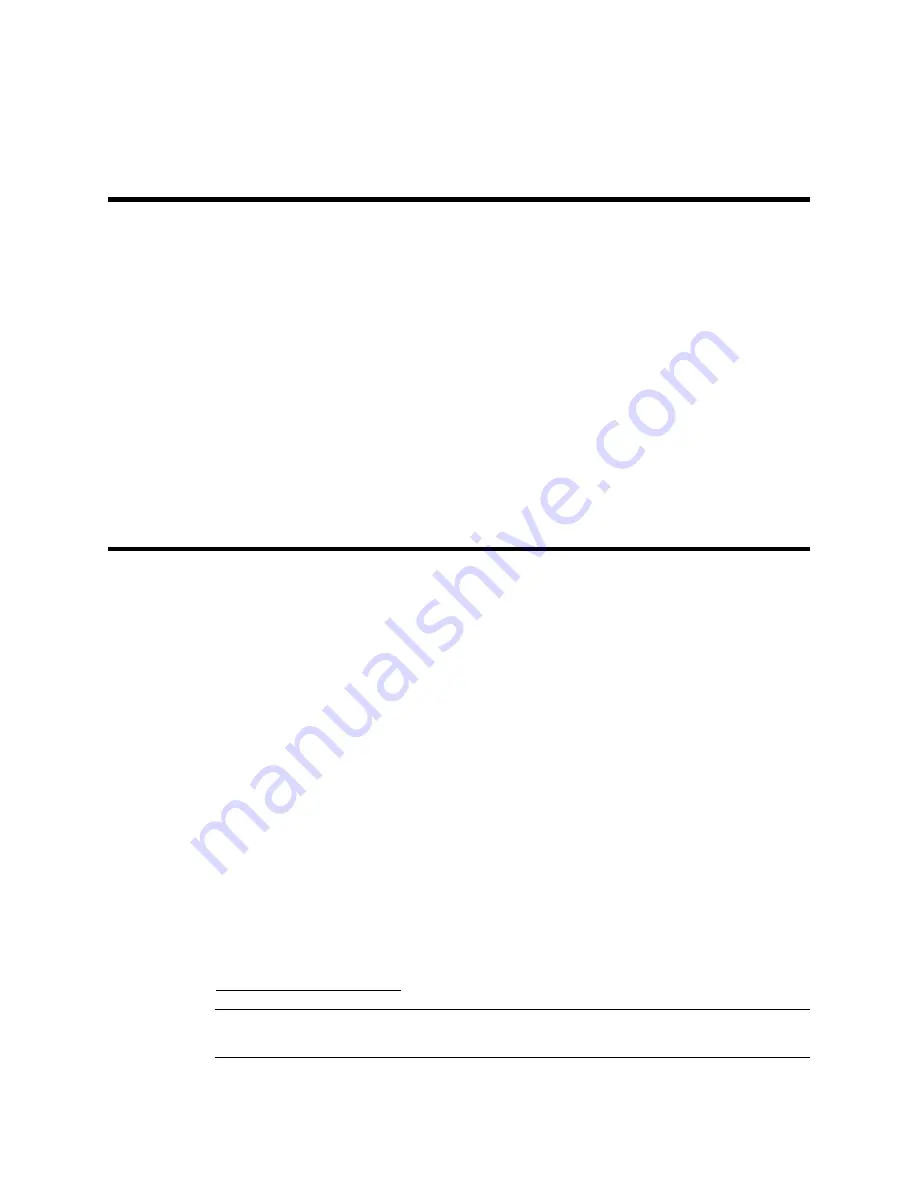
35-3010RK-04 Sample-Draw Detector • 13
the controller operator’s manual for directions.
6.
Remove the voltmeter from the test points.
7.
Close the housing door.
Operation
Normal Operation
During normal operation, the Pilot LED will be on and the flowmeter will indicate about
1.2 SCFH. The current gas readings will be indicated at the controller. See the controller’s
operator’s manual for a description of the reading indications.
Low Flow Alarm
If the flowrate falls below 0.6 SCFH (±0.2 SCFH), then the sample draw detector will
initiate a low flow alarm. In a low flow alarm the Fail LED will turn on and the pump will
shut off. In addition, the sensor signals to the controller will be interrupted by the sample
draw detector resulting in a failure indication for each channel at the controller. If a low
flow alarm occurs, press the pump reset switch for about 2 seconds to restart the pump,
turn off the Fail LED, and resume proper sensor signal transmission to the controller. If the
condition continues, find the cause of the reduced flow, correct it, and restart the pump
with the pump reset switch. A flow reduction can be caused by a flow blockage, a leak in
the flow system, a malfunctioning pressure switch, or a malfunctioning pump.
Maintenance
This section describes maintenance procedures. It includes preventive maintenance
procedures. This section also includes procedures to troubleshoot the sample draw
detector, replace components of the sample draw detector, and adjust the low flow setting.
Preventive Maintenance
This section describes a preventive maintenance schedule to ensure the optimum
performance of the sample draw detector. It includes daily, monthly, and quarterly
procedures.
Daily
1.
Verify that the pilot light is on.
2.
Verify that the flowmeter indicates a flow rate of approximately 1.2 SCFH.
If necessary use the bypass valve or flow adjust potentiometer to adjust the flow rate
to 1.2 SCFH.
3.
Verify a reading of 0%LEL for the combustible channel and 0 ppm for the CO channel
(100 mV at the amp 1 test points). Investigate significant changes in the reading.
Monthly
This procedure describes a test to verify that the sample draw detector responds properly
to the target gases.
Preparing for the response test
CAUTION:
This procedure may cause alarms at the controller. Take appropriate action to avoid
this, such as entering the calibration mode at the controller or disabling alarms.