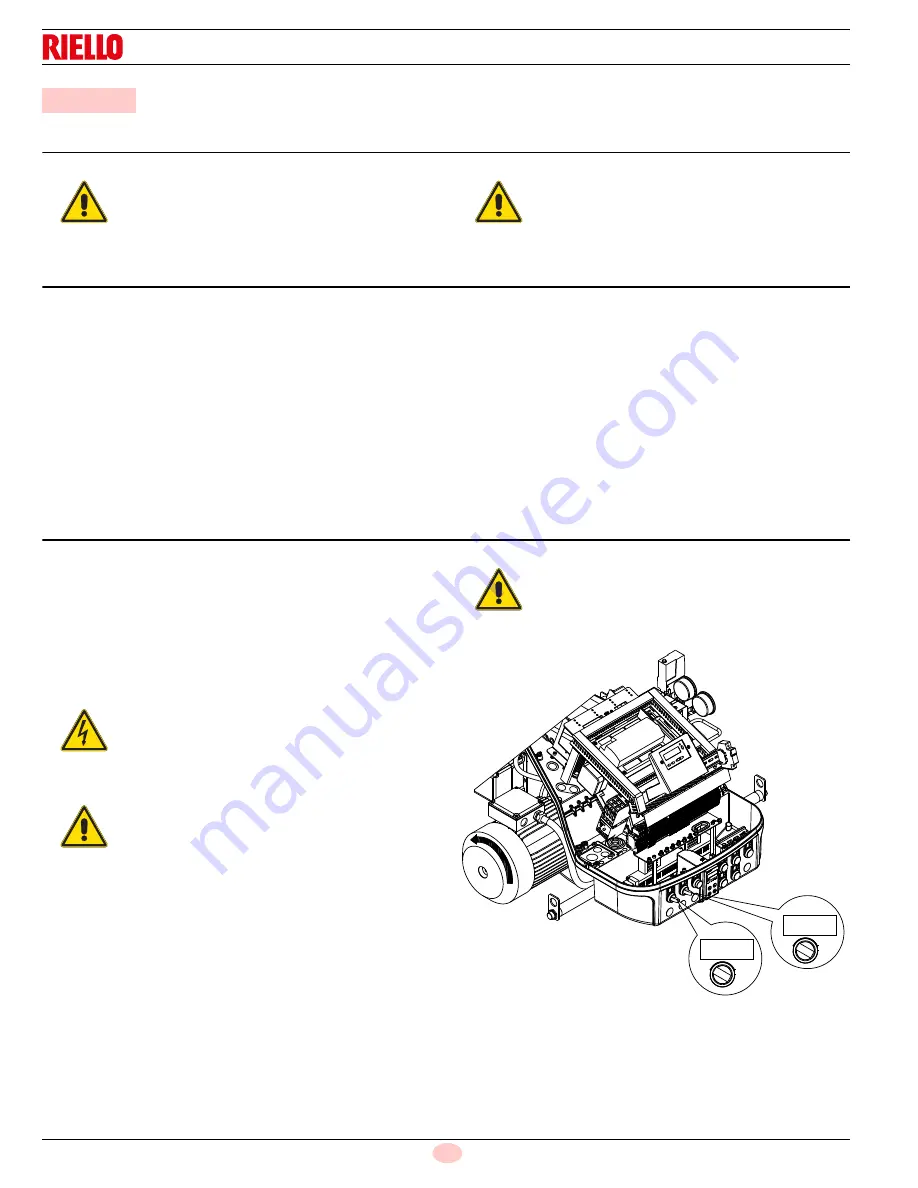
20109674
28
GB
Start-up, calibration and operation of the burner
5.1
Notes on safety for the first start-up
5.2
Burner calibration
The optimum calibration of the burner requires an analysis of the
flue gases at the boiler outlet.
The following settings that have already been made do not require
modification under normal circumstances:
5.2.1
Combustion head setting
Refer to page 20.
5.2.2
Nozzle adjustment
Refer to page 18.
5.2.3
Electrode position
Refer to Fig. 15.
5.2.4
Pump adjustment
No settings are required for the pump, which is set to 290 PSI by
the manufacturer.
This pressure must be checked and adjusted (if required) after the
burner has been ignited. The only operation required in this phase
is the application of a pressure gauge on the appropriate pump at-
tachment.
5.3
Burner start-up
Feed electricity to the burner via the disconnecting switch on the
boiler panel.
Close the thermostats/pressure switches, set the parameters on
the RWF55 regulator. Please refer to the specific manual for this
operation.
Turn the switch to position “
ON
” (Fig. 37) and turn the switch to po-
sition “
LOCAL
” for “local operation”, or “
REMOTE
” for “remote op-
eration”.
5
Start-up, calibration and operation of the burner
WARNING
The first start-up of the burner must be carried out
by qualified personnel, as indicated in this manual
and in compliance with the standards and regula-
tions of the laws in force.
WARNING
Check the correct working of the adjustment, com-
mand and safety devices.
DANGER
Make sure that the lamps or testers connected to
the solenoids, or indicator lights on the solenoids
themselves, show that no voltage is present.
If voltage is present, stop the burner
immediately
and check the electrical wiring.
WARNING
When the burner starts, check the direction of the
motor rotation, as indicated in Fig. 37.
As the burner is not fitted with a device to check the
sequence of the phases, the motor rotation may be
incorrect. As soon as the burner starts up, go in
front of the cooling fan of the fan motor and check it
is rotating anticlockwise (Fig. 37).
If this is not the case:
place the switch of Fig. 37 in position “
OFF
”
and wait for the control box to carry out the
switch off phase;
disconnect the electrical supply from the
burner;
invert the phases on the three-phase power
supply
WARNING
For the start-up procedure and the parameters
calibration, refer to the specific instruction man-
ual of the LMV37... electronic cam supplied with
the burner.
OFF ON
LOCAL REMOTE
Fig. 37
20111963