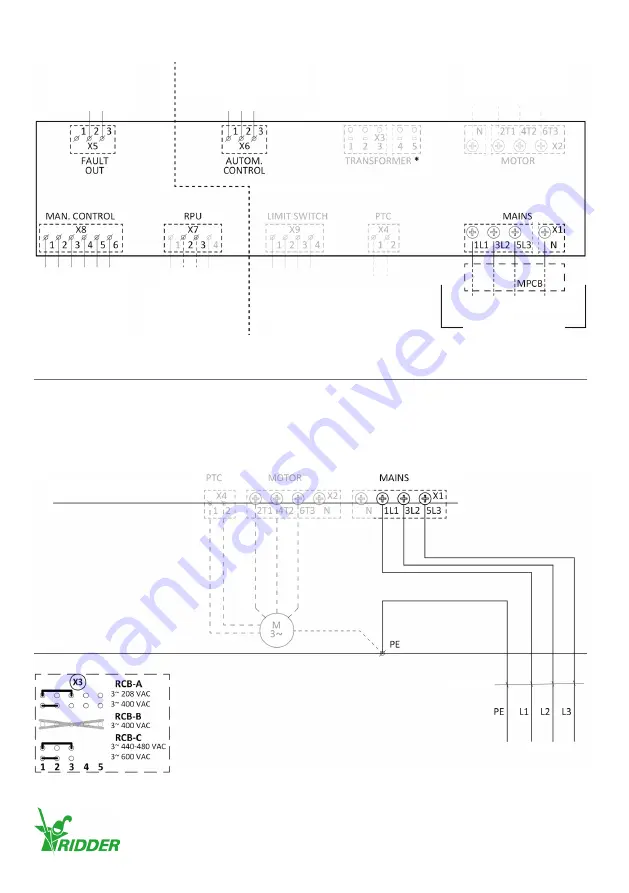
RLL400 control-board (RCB):
5.5 3-phase electric motor (208-600 VAC)
•
Make sure that the configuration (RCB-A or C) on X3 (TRANSFORMER) agrees with the supply
voltage!
•
Ridder Drive Systems connects X2 (MOTOR) and X4 (PTC).
•
Connect the supply voltage to X1 (MAINS) and PE (protective earth).
Alarm
§5.11 OPTIONAL
§5.9 OPTIONAL
§5.10 OPTIONAL
§5.5/ §5.6/ §5.7
CONTROL BOARD A2 (RCB)
Manual control
Position feedback
Power In
* X3 is not there on RCB-B
Automatic Control
Transformer configuration
Power Out
§5.8
Limit Switch
Thermal Protection
Control board A2
A1
(in)
(out)
(in)
4 x 1.5 mm²
Ridder Drive Systems B.V.
T
+31 (0)341 416 854 -
F
+31 (0)341 416 611 -
I
16
Содержание LogicLink RLL400
Страница 32: ......