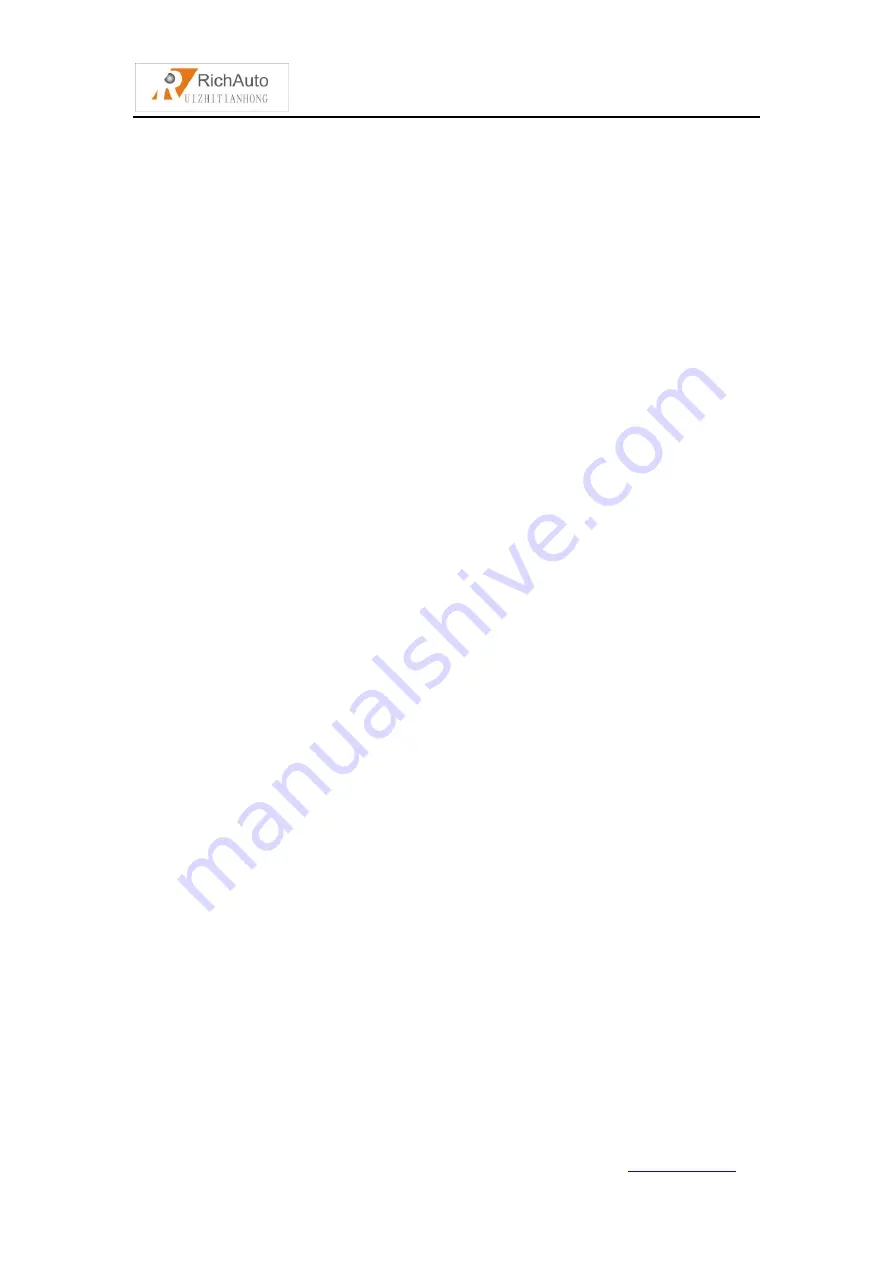
RichAuto S & T Co., Ltd
Add: 5th
floor, No.4 building, No 4. Yard, life Rd, life science park, beiqing St., changping district Beijing, China
Tel
:
010-53275118 Fax
:
010-53275110/53275111 Web site
11
3
.
Wiring Instructions
3.1 RichAuto interface board description
Interface board schematic diagram: