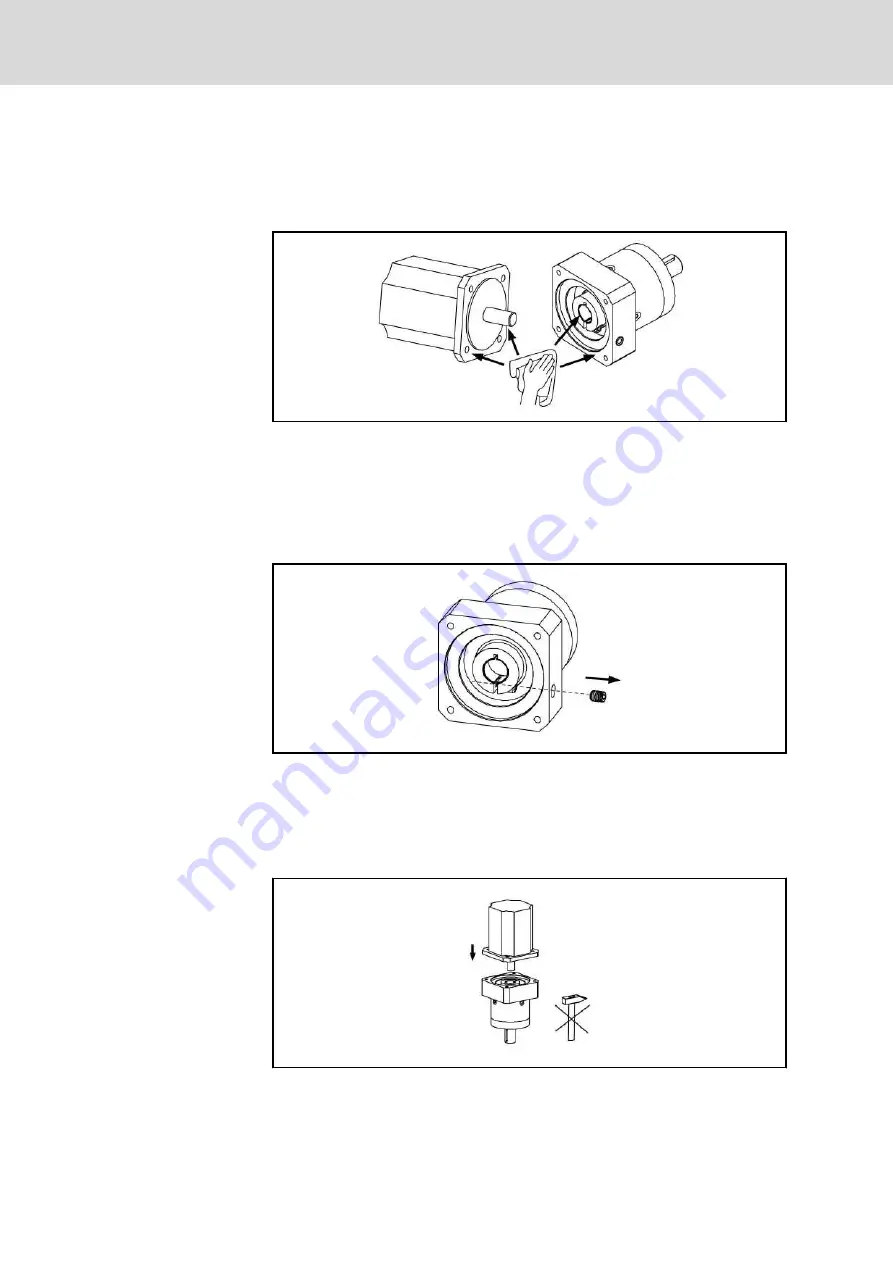
10.2.2
Mounting Procedure
If the gearbox and motor have been checked on their quality, the following
assembly procedure is recommended.
1. Clean and check the parts.
Fig.10-1:
Cleaning of the parts before mounting
Check for damage to the motor shaft, compression coupling bore and
any bushing, as well as the faces of motor and gearbox flanges and
clean them free from grease thoroughly. Do not clean the parts with
compressed air. Avoid using aggressive detergents, which could dam‐
age the seals.
2. Remove cap screws.
Fig.10-2:
Remove the cover screws
Remove the cover screws from the gearbox connection flange, which
covers the access to the clamping screw. Turn the compression cou‐
pling so that the heads of the clamping screws line up with the tapped
holes, which have now been opened in the gearbox`s adapter plate.
3. Insert the motor shaft into the gearbox
Fig.10-3:
Insert the motor shaft into the gearbox
Insert the motor shaft into the gearbox coupling until the gearbox´s con‐
necting flange and the motor face are fully in contact. It `should be pos‐
Bosch Rexroth AG
DOK-GEAR**-GTE********-PR08-EN-P
Rexroth GTE Planetary Gearboxes
68/83
Assembly
Содержание GTE Series
Страница 6: ...Bosch Rexroth AG DOK GEAR GTE PR08 EN P Rexroth GTE Planetary Gearboxes IV 83 ...
Страница 26: ...Bosch Rexroth AG DOK GEAR GTE PR08 EN P Rexroth GTE Planetary Gearboxes 24 83 ...
Страница 32: ...Bosch Rexroth AG DOK GEAR GTE PR08 EN P Rexroth GTE Planetary Gearboxes 30 83 ...
Страница 58: ...Bosch Rexroth AG DOK GEAR GTE PR08 EN P Rexroth GTE Planetary Gearboxes 56 83 ...
Страница 68: ...Bosch Rexroth AG DOK GEAR GTE PR08 EN P Rexroth GTE Planetary Gearboxes 66 83 ...
Страница 78: ...Bosch Rexroth AG DOK GEAR GTE PR08 EN P Rexroth GTE Planetary Gearboxes 76 83 ...
Страница 82: ...Bosch Rexroth AG DOK GEAR GTE PR08 EN P Rexroth GTE Planetary Gearboxes 80 83 ...
Страница 85: ...Notes DOK GEAR GTE PR08 EN P Rexroth GTE Planetary Gearboxes Bosch Rexroth AG 83 83 ...