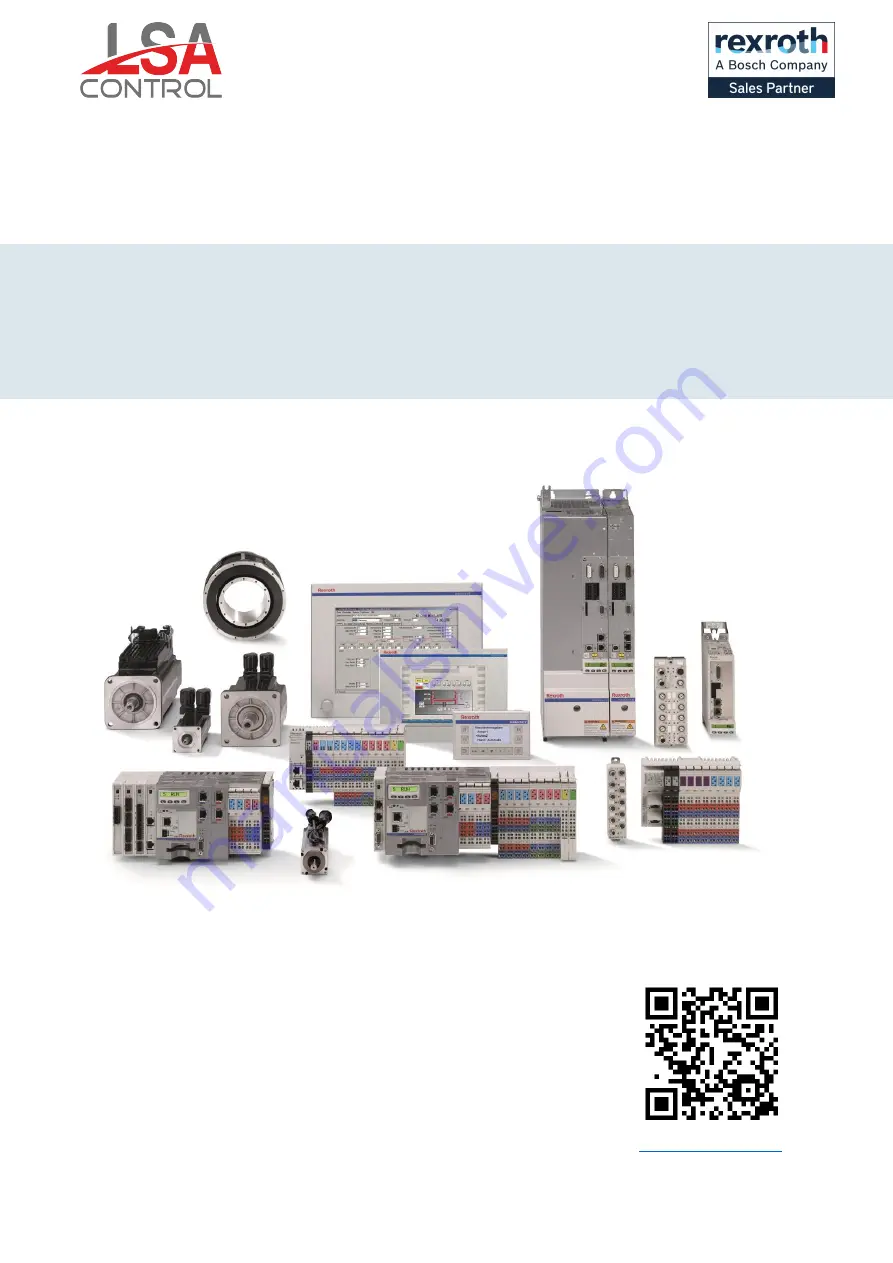
Levante Sistemas de
Automatización y Control S.L.
Catálogos
Distribuidor oficial Bosch Rexroth, Indramat, Bosch y Aventics.
LSA Control S.L. - Bosch Rexroth Sales Partner
Ronda Narciso Monturiol y Estarriol, 7-9
Edificio TecnoParQ Planta 1ª Derecha, Oficina 14
(Parque Tecnológico de Paterna)
46980 Paterna (Valencia)
www.lsa-control.com
www.boschrexroth.es
Содержание Mannesmann Rexroth CLM-01.3-M
Страница 5: ...LSA Control S L www lsa control com comercial lsa control com 34 960 62 43 01 ...
Страница 7: ...LSA Control S L www lsa control com comercial lsa control com 34 960 62 43 01 ...
Страница 17: ...LSA Control S L www lsa control com comercial lsa control com 34 960 62 43 01 ...
Страница 31: ...LSA Control S L www lsa control com comercial lsa control com 34 960 62 43 01 ...
Страница 39: ...LSA Control S L www lsa control com comercial lsa control com 34 960 62 43 01 ...
Страница 57: ...LSA Control S L www lsa control com comercial lsa control com 34 960 62 43 01 ...
Страница 150: ...LSA Control S L www lsa control com comercial lsa control com 34 960 62 43 01 ...
Страница 153: ...LSA Control S L www lsa control com comercial lsa control com 34 960 62 43 01 ...
Страница 215: ...LSA Control S L www lsa control com comercial lsa control com 34 960 62 43 01 ...
Страница 291: ...LSA Control S L www lsa control com comercial lsa control com 34 960 62 43 01 ...
Страница 313: ...LSA Control S L www lsa control com comercial lsa control com 34 960 62 43 01 ...
Страница 314: ...LSA Control S L www lsa control com comercial lsa control com 34 960 62 43 01 ...
Страница 315: ...LSA Control S L www lsa control com comercial lsa control com 34 960 62 43 01 ...
Страница 316: ...LSA Control S L www lsa control com comercial lsa control com 34 960 62 43 01 ...
Страница 317: ...LSA Control S L www lsa control com comercial lsa control com 34 960 62 43 01 ...
Страница 318: ...LSA Control S L www lsa control com comercial lsa control com 34 960 62 43 01 ...
Страница 319: ...LSA Control S L www lsa control com comercial lsa control com 34 960 62 43 01 ...
Страница 320: ...LSA Control S L www lsa control com comercial lsa control com 34 960 62 43 01 ...
Страница 321: ...LSA Control S L www lsa control com comercial lsa control com 34 960 62 43 01 ...
Страница 323: ...LSA Control S L www lsa control com comercial lsa control com 34 960 62 43 01 ...
Страница 325: ...LSA Control S L www lsa control com comercial lsa control com 34 960 62 43 01 ...
Страница 326: ...LSA Control S L www lsa control com comercial lsa control com 34 960 62 43 01 ...
Страница 327: ...LSA Control S L www lsa control com comercial lsa control com 34 960 62 43 01 ...
Страница 328: ...LSA Control S L www lsa control com comercial lsa control com 34 960 62 43 01 ...
Страница 329: ...LSA Control S L www lsa control com comercial lsa control com 34 960 62 43 01 ...
Страница 331: ...LSA Control S L www lsa control com comercial lsa control com 34 960 62 43 01 ...
Страница 332: ...LSA Control S L www lsa control com comercial lsa control com 34 960 62 43 01 ...
Страница 333: ...LSA Control S L www lsa control com comercial lsa control com 34 960 62 43 01 ...
Страница 335: ...LSA Control S L www lsa control com comercial lsa control com 34 960 62 43 01 ...
Страница 336: ...LSA Control S L www lsa control com comercial lsa control com 34 960 62 43 01 ...
Страница 337: ...LSA Control S L www lsa control com comercial lsa control com 34 960 62 43 01 ...
Страница 339: ...LSA Control S L www lsa control com comercial lsa control com 34 960 62 43 01 ...
Страница 340: ...LSA Control S L www lsa control com comercial lsa control com 34 960 62 43 01 ...
Страница 341: ...LSA Control S L www lsa control com comercial lsa control com 34 960 62 43 01 ...
Страница 343: ...LSA Control S L www lsa control com comercial lsa control com 34 960 62 43 01 ...
Страница 344: ...LSA Control S L www lsa control com comercial lsa control com 34 960 62 43 01 ...
Страница 345: ...LSA Control S L www lsa control com comercial lsa control com 34 960 62 43 01 ...
Страница 346: ...LSA Control S L www lsa control com comercial lsa control com 34 960 62 43 01 ...
Страница 347: ...LSA Control S L www lsa control com comercial lsa control com 34 960 62 43 01 ...
Страница 349: ...LSA Control S L www lsa control com comercial lsa control com 34 960 62 43 01 ...
Страница 351: ...LSA Control S L www lsa control com comercial lsa control com 34 960 62 43 01 ...
Страница 352: ...LSA Control S L www lsa control com comercial lsa control com 34 960 62 43 01 ...
Страница 353: ...LSA Control S L www lsa control com comercial lsa control com 34 960 62 43 01 ...
Страница 354: ...LSA Control S L www lsa control com comercial lsa control com 34 960 62 43 01 ...
Страница 355: ...LSA Control S L www lsa control com comercial lsa control com 34 960 62 43 01 ...
Страница 357: ...LSA Control S L www lsa control com comercial lsa control com 34 960 62 43 01 ...
Страница 359: ...LSA Control S L www lsa control com comercial lsa control com 34 960 62 43 01 ...
Страница 360: ...APPENDIX D PARAMETER INPUT SHEETS LSA Control S L www lsa control com comercial lsa control com 34 960 62 43 01 ...
Страница 361: ...LSA Control S L www lsa control com comercial lsa control com 34 960 62 43 01 ...
Страница 369: ...LSA Control S L www lsa control com comercial lsa control com 34 960 62 43 01 ...
Страница 370: ...LSA Control S L www lsa control com comercial lsa control com 34 960 62 43 01 ...
Страница 372: ...LSA Control S L www lsa control com comercial lsa control com 34 960 62 43 01 ...
Страница 373: ...LSA Control S L www lsa control com comercial lsa control com 34 960 62 43 01 ...
Страница 374: ...LSA Control S L www lsa control com comercial lsa control com 34 960 62 43 01 ...
Страница 375: ...LSA Control S L www lsa control com comercial lsa control com 34 960 62 43 01 ...
Страница 376: ...LSA Control S L www lsa control com comercial lsa control com 34 960 62 43 01 ...
Страница 377: ...LSA Control S L www lsa control com comercial lsa control com 34 960 62 43 01 ...
Страница 383: ...LSA Control S L www lsa control com comercial lsa control com 34 960 62 43 01 ...