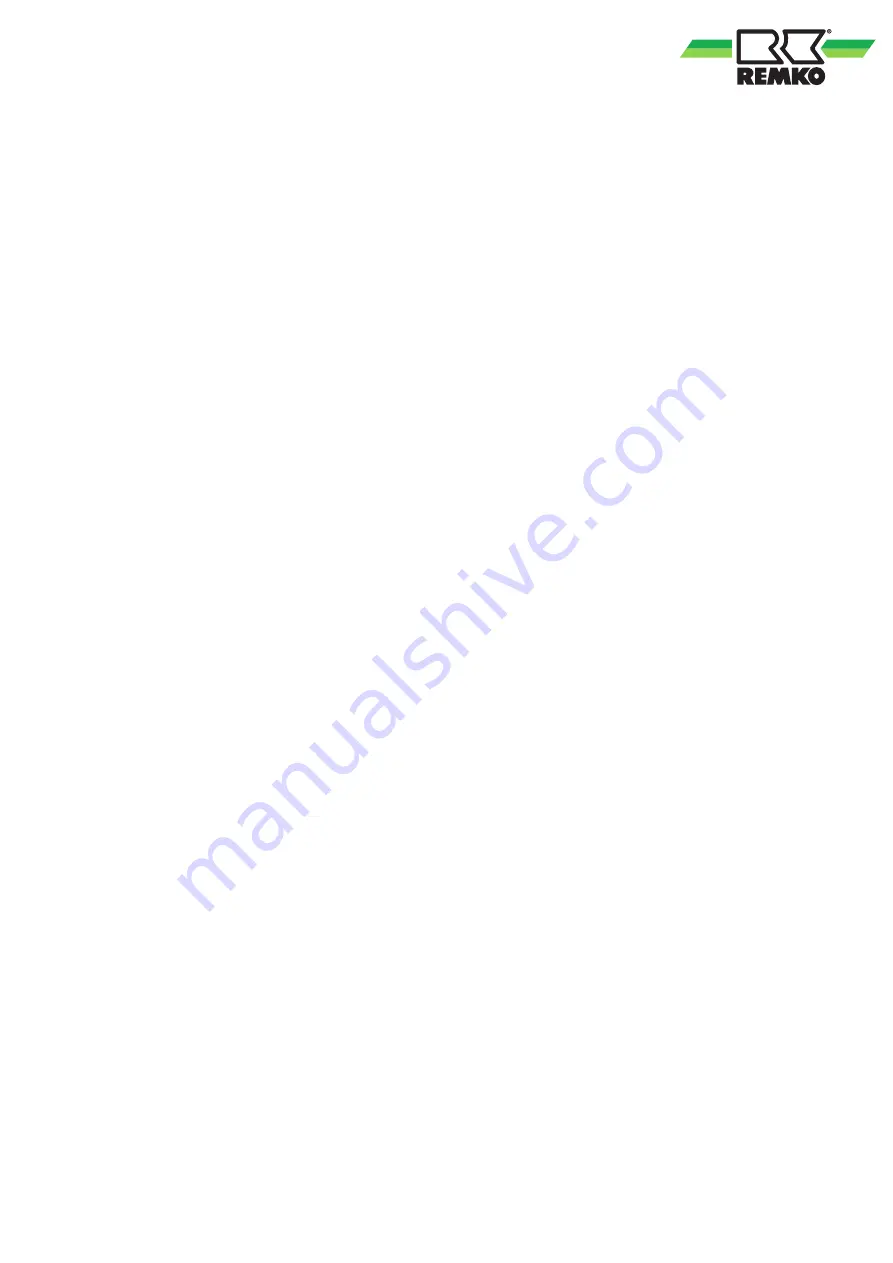
n
Leak detection methods
The following leak detection methods are per-
mitted for systems with combustible refriger-
ants. Electronic equipment must be used for
detecting leaks. These must be selected with
the sensitivity matched to the situation and
recalibrated if necessary (calibration must take
place in a refrigerant-free environment). The
leak detection device must be adjusted to the
lowest flammability limit (LFL) of the refrig-
erant. Liquid leakage instruments are permitted
for most refrigerants. Chlorinated substances
are the exception here as the chlorine in com-
bination with the refrigerants can cause corro-
sion on the copper cables. If a leak is detected,
all potential open ignition sources must be
removed immediately. If a leak has been
detected in the system which requires
reworking of the piping in the form of soldering,
the system must be completely free of refrig-
erant or, if possible, the affected part discon-
nected from the system using stopcocks. The
affected system parts must be flushed with
oxygen-free nitrogen run before and during the
repair work.
n
Emptying and evacuating the system
If the refrigerant circuit must be opened for
repairs or other reasons, this must be carried
out in a safe and professional way. In any
event, proceed with extreme caution since igni-
tion may occur at any time! Stick to the fol-
lowing procedure:
1. Drain the refrigerant
2. Flush the system with insert gas
3. Evacuate
4. Repeat steps 2 to 3 if required
5. Opening the system by cutting or soldering
The system must be flushed with oxygen-free
nitrogen in order to guarantee safety. The
flushing process must be repeated multiple
times if necessary. Do not use compressed air
or oxygen for the flushing process! After evacu-
ating, flushing takes place by filling with dried
nitrogen until the operating pressure is reached
and then the system must be evacuated again.
This flushing process must often be repeated
until there is no more refrigerant in the system.
After the last flushing, the system must be
brought to the ambient pressure in order to
start work. The flushing process is indispen-
sable when soldering work is required on the
piping. Ensure that the vacuum pump outlet is
not near an ignition source and continuous
ventilation is guaranteed.
n
Filling process
The following requirements for the general
specifications must also be fulfilled during the
filling process:
- Ensure that no contamination occurs from
other refrigerants (residues in the filling equip-
ment).
- Keep the lines as short as possible to mini-
mise the likelihood of residues forming.
- Filling bottles and cylinders must be stood
upright.
- Ensure that the system is earthed before
filling.
- Label the system with the refrigerant type
designation after filling
- Never exceed the maximum fill level.
The system must be checked for leaks (pres-
sure test!) before filling. The system must be
checked for leaks once more after filling and
before commissioning. Check for leaks again
when leaving the work space.
n
Labelling when shutting down
If a unit must be taken out of operation and the
refrigerant must be disposed of, the unit must
be labelled with the date and a signature.
Ensure that the note remains attached to the
combustible refrigerant.
n
Transportation of units which contain com-
bustible refrigerants
National provisions must be observed.
n
Storing of units which contain combustible
refrigerant
National provisions must be observed.
n
Transportation without the original pack-
aging
If the units are transported without the original
packaging, they must be packed in such a way
that mechanical damage is prevented. The
units must be transported upright.
1.9 Unauthorised modification
and changes
Modifications or changes to units and components
are not permitted and may cause malfunctions.
Safety devices may not be modified or bypassed.
Original replacement parts and accessories
authorised by the manufactured ensure safety. The
use of other parts may invalidate liability for
resulting consequences.
9
Содержание MKT 255 ECO S-Line
Страница 26: ...REMKO MKT ECO series 26...
Страница 27: ......