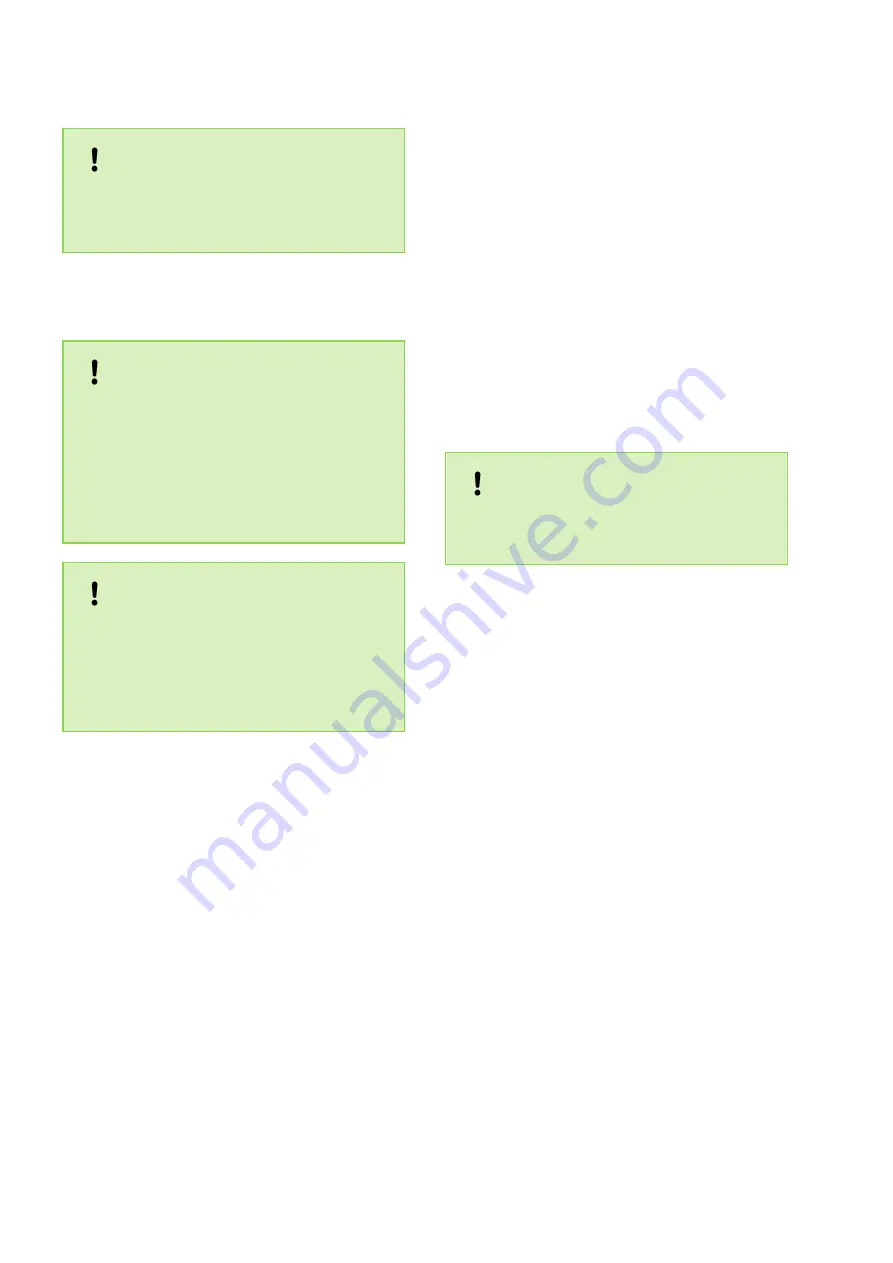
NOTICE!
Country-specific laws may differ from Regula-
tion (EC) 842/2006. The respective national
laws for leak testing of heat pumps must be
observed.
Checking the filling level and filling pressure of
the brine cycle
NOTICE!
Leaks in the brine cycle can lead to brine
leaking and damage. For this purpose, switch
off the automatic circuit breakers of the heat
pump.
–
Switch off the heat pump if there are leaks
in the brine cycle.
–
Have leaks repaired by your specialist tech-
nician.
NOTICE!
If the brine level is too low, the heat pump may
be damaged.
–
After initial operation, check the brine level
daily for one week and half-yearly there-
after.
–
Have your specialist refill the brine liquid.
If the brine level drops slightly in the first month
after the system is commissioned, this is normal.
The level can also vary depending on the tempera-
ture of the heat source. However, it must never
sink so far that it is no longer visible in the brine
expansion tank, as otherwise air will enter the
brine cycle. Check the brine level or filling pressure
of the brine cycle and the pre-pressure of the dia-
phragm expansion vessel at regular intervals.
You can read the filling pressure of the brine cycle
(“pressure heat source”) in the heat pump con-
troller.
The filling pressure should be between 1 and 2
bar. If the filling pressure drops below 0.2 bar, the
heat pump is automatically switched off and an
error message is displayed.
10
Temporary shutdown
The system may not be switched off at the mains
power supply even if the heat pump is not used for
heating purposes over an extended period (e.g.
holidays)!
n
The system is to be switched to "Stand-by"
mode for heating during temporary shutdowns
and for hot water it should be switched to "Off"
mode.
n
Heating phases can be programmed for the
duration of the period of absence.
n
The previous operating mode has to be
switched back on when the shutdown phase is
over.
n
Instructions for changing the mode appear in
the corresponding chapter of the heat-pump
manager's manual.
NOTICE!
In "Standby" , the heat pump is in standby
mode. Of the entire system, only the frost-pro-
tection function s activated.
REMKO cooling module
20
Содержание KNGcooling module
Страница 23: ......