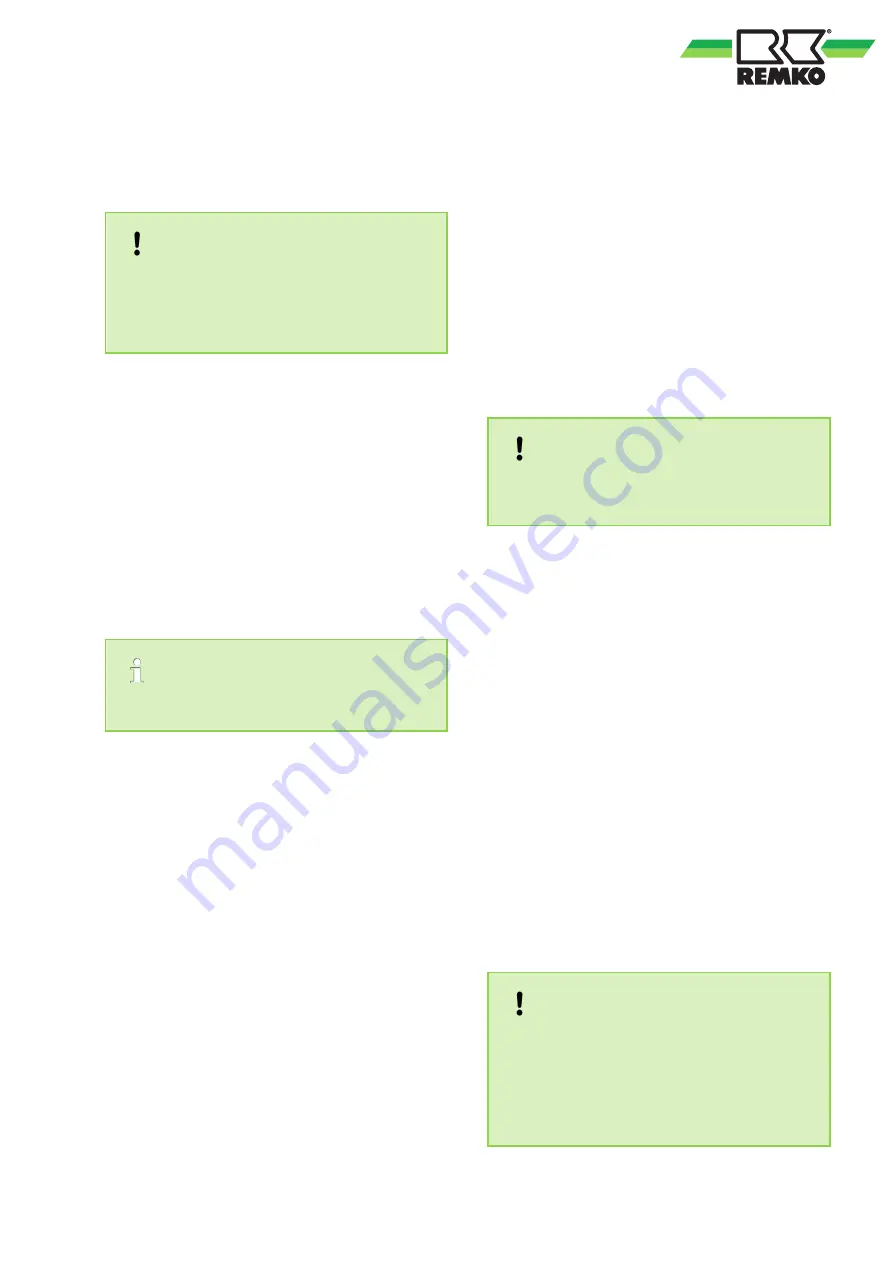
8
Commissioning
Control panel and information on commis-
sioning
NOTICE!
Before commissioning, the complete system
hydraulics must be flushed and filled in accord-
ance with standards. If a drinking water storage
tank is installed, this must likewise be filled
before commissioning.
The Smart-Control Touch is used to operate and
control the complete heating system. The Smart
Control Touch is operated via the touch display.
n
The unit is pre-installed at the factory. After a
reset of the Smart Control, the default parame-
ters are loaded.
n
An intensive visual inspection is to be carried
out before the actual commissioning.
n
Switch on the power supply.
n
The pre-installed data is then loaded and the
parameters can be set using the commis-
sioning wizard or in the system configuration.
You can find information on this in the separate
operating instructions of the Smart Control.
Additional information on the functional and
operation, refer to the Smart-Control manual.
9
Care and maintenance
Regular care and maintenance assure fault-free
operation and long service life for the heat pump
system.
Care
n
The heat pump must be kept free of dirt and
other deposits.
n
The unit is to be cleaned with a damp cloth. In
doing so, ensure that no caustic, abrasive or
solvent-based cleaning products are used. Use
of powerful water jets is to be avoided.
Cleaning the heat source site
NOTICE!
A dirt trap must be installed in the heat source
inlet of the heat pump to protect the evaporator
against contamination.
The filter screen of the dirt trap should be cleaned
one day after commissioning. Further checks
should be determined according to the level of pol-
lution. If no more impurities are visible, the filter of
the dirt trap can be removed to reduce the pres-
sure losses.
Maintenance
n
To perform the statutory leak test where appli-
cable, it is necessary to arrange a yearly main-
tenance contract with an appropriate specialist
firm.
Leak test
According to Regulation (EC) No. 842/2006, all
refrigeration systems containing a refrigerant filling
quantity of at least 2.4 kg, with “hermetically
sealed” refrigeration systems of at least 4.7 kg,
must be checked for leaks by the operator yearly.
The leak test must be documented and kept for at
least 5 years. The checks must be carried out by
certified personnel in accordance with Regulation
(EC) No. 1516/2007.
NOTICE!
If the refrigerant capacity of 2.4 or 4.7 kg is
exceeded, an annual leak testing must be made
of the refrigerant circuit by a firm specialising in
this field. A heat pump should always be serv-
iced yearly. Therefore, we recommend
arranging for a service contract that includes
the leak inspection.
19
Содержание KNGcooling module
Страница 23: ......