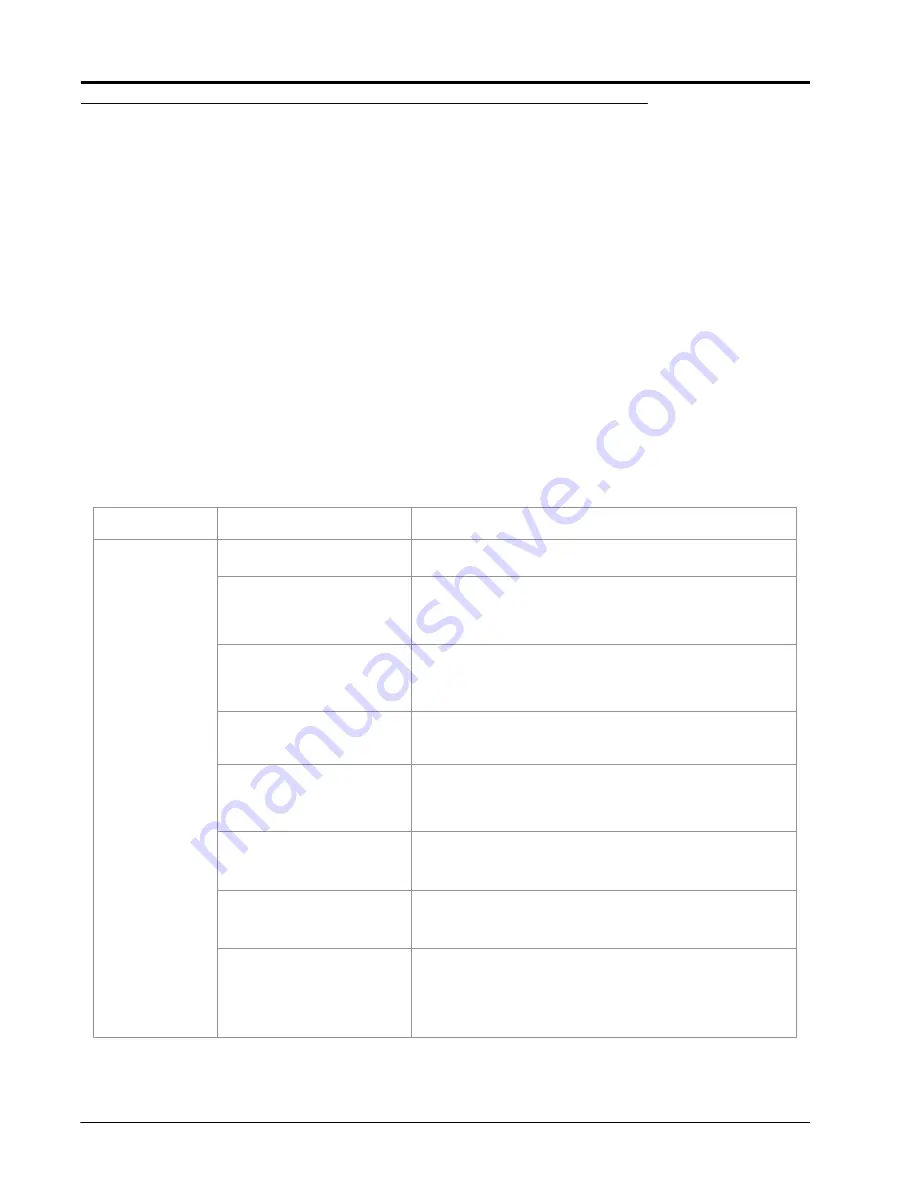
Chapter 4
34
Envizio Pro and Envizio Pro II Installation and Operation Manual
CAN Troubleshooting
Although the control algorithm is located within the CAN node, all of the same troubleshooting techniques that
are used in a traditional hard-wired or serial control systems still apply to a CAN system and the behavior of the
system remains the same. Flow and speed sensors, as well as the control valve and boom valves, are used in
the same fashion.
CAN Node Off-line Errors
Occasional reports have been received on Raven consoles sporadically losing communication with one or
more CAN nodes. The most likely causes for this problem are:
1.
Corroded and/or open connections in the circuit.
2.
Computer and/or CAN node logic power and grounds connected to a “dirty” power source (dirty power is
defined as any circuit with a variable load that exceeds 1 ampere). This is especially true of circuits loaded
by electrical coils.
3.
Computer and/or nodes connected to different power and/or ground sources. This can result in components
operating at different voltage planes.
Below are some common causes for communication failures:
Issue
Possible Cause
Solution
CANbus cannot
read the product
node
• The node is not connected to
the CANbus
• Connect the node and re-initialize the field computer to read
the product node.
• Node is not properly powered
• Connect the clean power - 16 gauge red wire and high current
power - 12 gauge red wire from the product node to a 12V DC
power source that is capable of supplying power to all nodes
connected to the CANbus system
• Node is not properly
grounded
• Connect the clean ground - 16 gauge white wire and the high
current ground - 12 gauge white wire to a good, quality ground
source. Raven recommends grounding the wires to the
negative terminal of the battery.
• The boom/speed node share
power and ground
connections
• Make sure that each node has a separate power and ground
connection.
• CANbus ends not terminated
• Make sure that both ends of the CANbus system are properly
terminated. Refer to the
Raven CANbus Network Installation
Manual
for information on properly terminating the CANbus
network.
• Corroded pins in CANbus
connections
• Check CANbus cable connectors for any highly corroded pins.
• Ensure dielectric grease has been applied to all cable
connections exposed to weather and field conditions.
• Moisture in connection
• Check CANbus cable connectors for any corroded pins.
• Ensure dielectric grease has been applied to all cable
connections exposed to weather and field conditions.
• Connectors not seated
properly
• Check that all CANbus cable connectors are inserted fully
(until the locking tab is engaged).
• Be sure to remove any moisture in connections which were
not properly seated. Check for corroded pins and apply
dielectric grease when reconnecting CANbus cables.
Содержание Envizio Pro
Страница 1: ...Software Version 3 2 Envizio Pro Envizio Pro II Installation Operation Manual...
Страница 36: ...Chapter 3 26 Envizio Pro and Envizio Pro II Installation and Operation Manual...
Страница 148: ...Chapter 7 138 Envizio Pro and Envizio Pro II Installation and Operation Manual...
Страница 158: ...Chapter 8 148 Envizio Pro and Envizio Pro II Installation and Operation Manual...
Страница 174: ...Chapter 9 164 Envizio Pro and Envizio Pro II Installation and Operation Manual...
Страница 178: ...Chapter 10 168 Envizio Pro and Envizio Pro II Installation and Operation Manual...
Страница 184: ...Chapter 11 174 Envizio Pro and Envizio Pro II Installation and Operation Manual...
Страница 210: ...Appendix D 200 Envizio Pro and Envizio Pro II Installation and Operation Manual...
Страница 230: ...Index 220 Envizio Pro Envizio Pro II Installation Operation Manual...