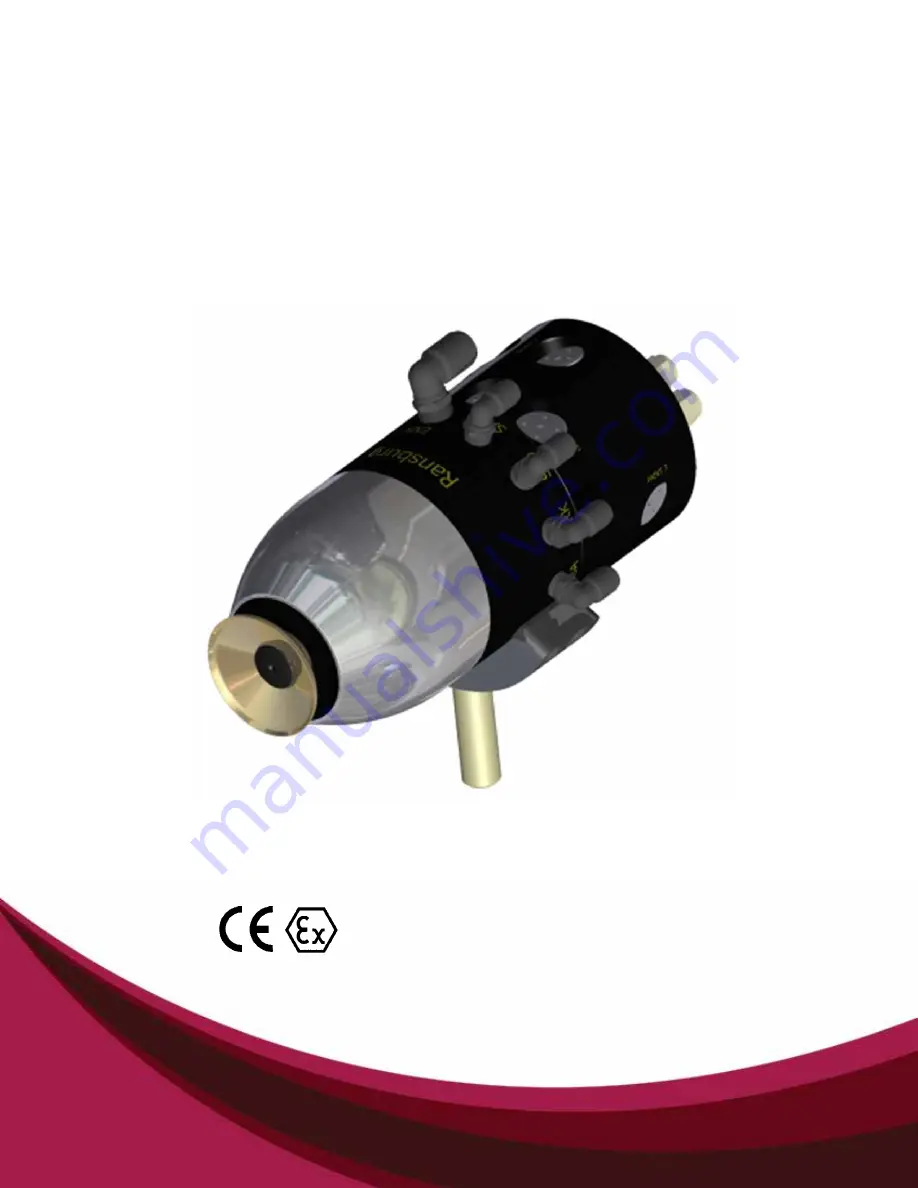
IMPORTANT:
Before using this equipment,
carefully read SAFETY PRECAUTIONS, starting
on page 1, and all instructions in this manual.
Keep this Service Manual for future reference.
Service Manual Price: $50.00 (U.S.)
MODEL: A13657
SERVICE MANUAL
LN-9282-14
June - 2014
Ransburg
AEROBELL 268
TM
IMPORTANT:
Before using this equipment,
carefully read SAFETY PRECAUTIONS, starting
on page 1, and all instructions in this manual.
Keep this Service Manual for future reference.
Service Manual Price: $50.00 (U.S.)
Содержание AEROBELL 268 A13657
Страница 18: ...OPERATING CHARACTERISTICS AND SPECIFICATIONS Aerobell 268 Introduction LN 9282 14 15 ...
Страница 19: ...OPERATING CHARACTERISTICS AND SPECIFICATIONS Aerobell 268 Aerobell 268 Aerobell 268 Introduction LN 9282 14 16 ...
Страница 20: ...OPERATING CHARACTERISTICS AND SPECIFICATIONS Aerobell 268 Aerobell 268 Aerobell 268 Introduction LN 9282 14 17 ...
Страница 21: ...DIMENSIONAL CHARACTERISTICS Aerobell 268 Introduction LN 9282 14 18 ...
Страница 29: ...Aerobell 268 Installation LN 9282 14 26 ...
Страница 75: ...Aerobell 268 Assembly Aerobell 268 Parts Identification LN 9282 14 72 ...
Страница 78: ...A13032 02 MONO FLEX DIRECT CHG Aerobell 268 Parts Identification LN 9282 14 75 ...