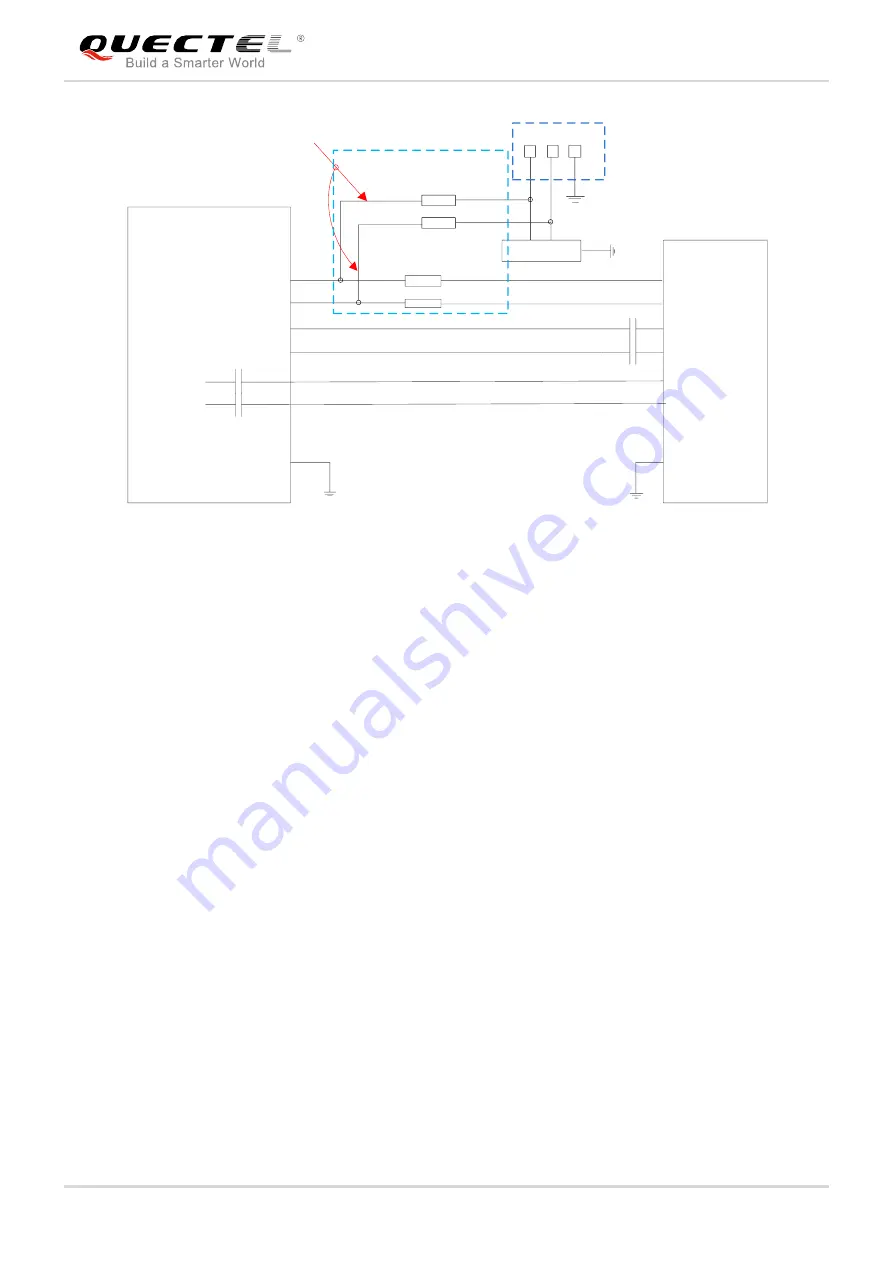
LTE-A Module Series
EM12-G Hardware Design
EM12-G_Hardware_Design 33 / 62
GND
USB3.0_TX-
USB3.0_TX+
GND
USB3.0_RX-
USB3.0_RX+
USB3.0_RX-
USB3.0_RX+
USB3.0_TX-
USB3.0_TX+
C3
C4
USB_DP
USB_DM
R1
R2
0R
0R
USB_DM
USB_DP
C1
C2
ESD Array
100nF
100nF
100nF
100nF
Module
MCU
R3
R4
NM_0R
NM_0R
Test Points
Minimize these stubs
Figure 16: Reference Circuit of USB 2.0 & 3.0 Interface
In order to ensure the integrity of USB 2.0 & 3.0 data line signal, R1/R2/R3/R4 components must be
placed close to the module, capacitors C1 and C2 have been placed inside the module, capacitors C3
and C4 must be placed close to the MCU, and these components should be placed close to each other.
In order to ensure the USB interface design corresponding with USB 2.0 & 3.0 specifications, please
comply with the following principles:
It is important to route the USB 2.0 & 3.0 signal traces as differential pairs with total grounding.
1) For USB 2.0 routing traces, the trace impedance of the
differential pair should be 90Ω, and the
trace length difference between the differential pair should be less than 2mm.
2)
For USB 3.0 routing traces, the trace impedance of Tx and Rx differential pairs should be 90Ω,
and the trace length difference between Tx and Rx differential pairs should be less than
0.7mm.
Do not route signal traces under crystals, oscillators, magnetic devices or RF signal traces. It is
important to route the USB 2.0 & 3.0 differential traces in inner-layer with ground shielding on not
only upper and lower layers but also right and left sides.
If USB connector is used, please keep the ESD protection components as close as possible to the
USB connector. Pay attention to the influence of junction capacitance of ESD protection components
on USB 2.0 & 3.0 data lines. The capacitance value of ESD protection components should be less
than 2.0pF for USB 2.0, and less than 0.4pF for USB 3.0.
If possible, reserve a 0R resistor on USB_DP and USB_DM lines, respectively.