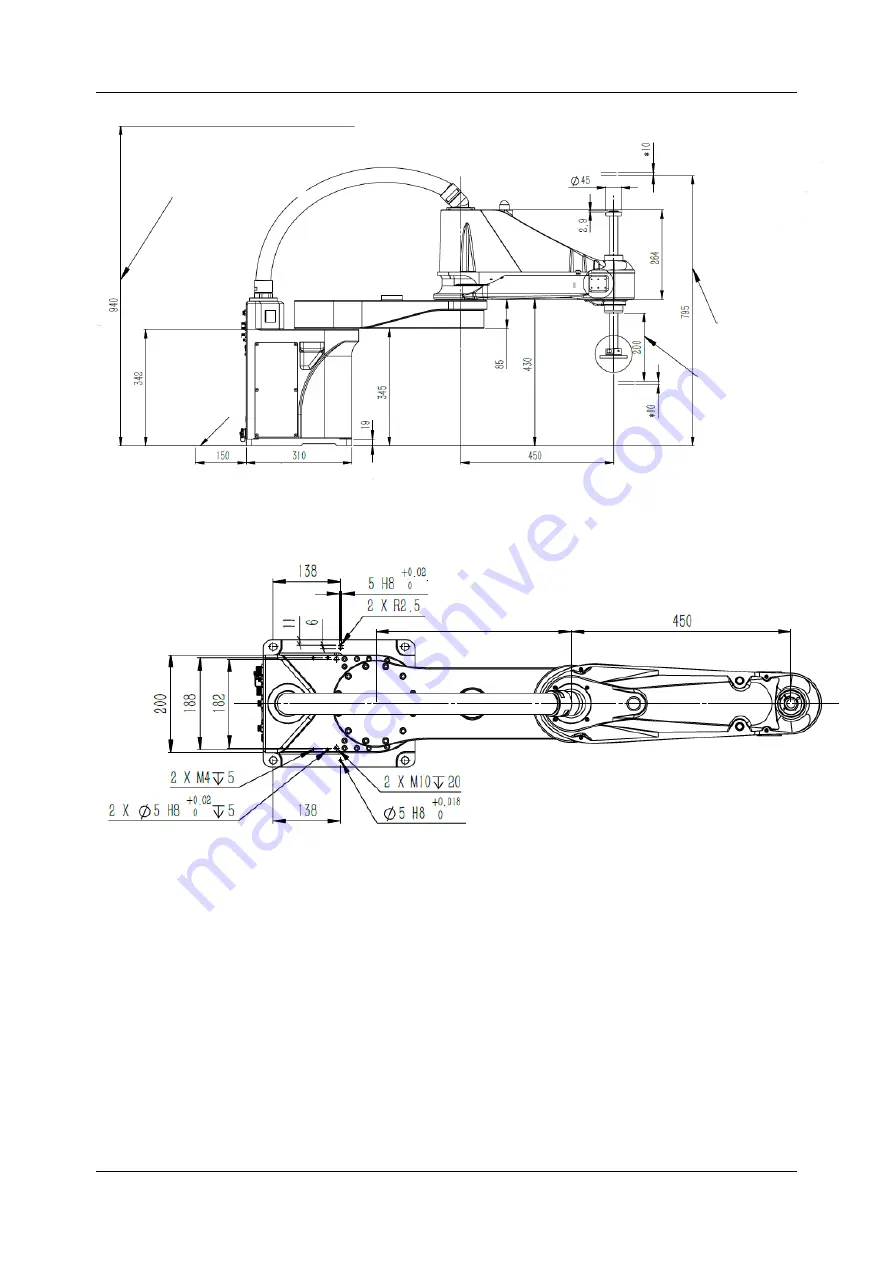
AH20 Robot User Manual
16 Document Version V1.0.1 (11-14-2022)
Figure 3-7 AH20-0850-0204-2000 dimensions (unit: mm)
Figure 3-8
AH20-0850-0204-2000 dimensions (unit: mm)
AH20-0850-0204-4000
The moving bellows will arch
to the left by up to 940 mm
Up to 795 mm
The maximum stroke of the
screw can reach 200 mm
150 mm space
is reserved for
cables
* Position where the screw reaches
the hard limit
Through hole
Through hole
Through hole
Содержание AH20
Страница 1: ......
Страница 3: ......
Страница 29: ...AH20 Robot User Manual 14 Document Version V1 0 1 11 14 2022 Figure 3 5 AH20 1050 0204 2000 AH20 1050 0204 4000...
Страница 93: ...AH20 Robot User Manual 78 Document Version V1 0 1 11 14 2022 Figure 6 25 Teach interface...
Страница 105: ...AH20 Robot User Manual 90 Document Version V1 0 1 11 14 2022...