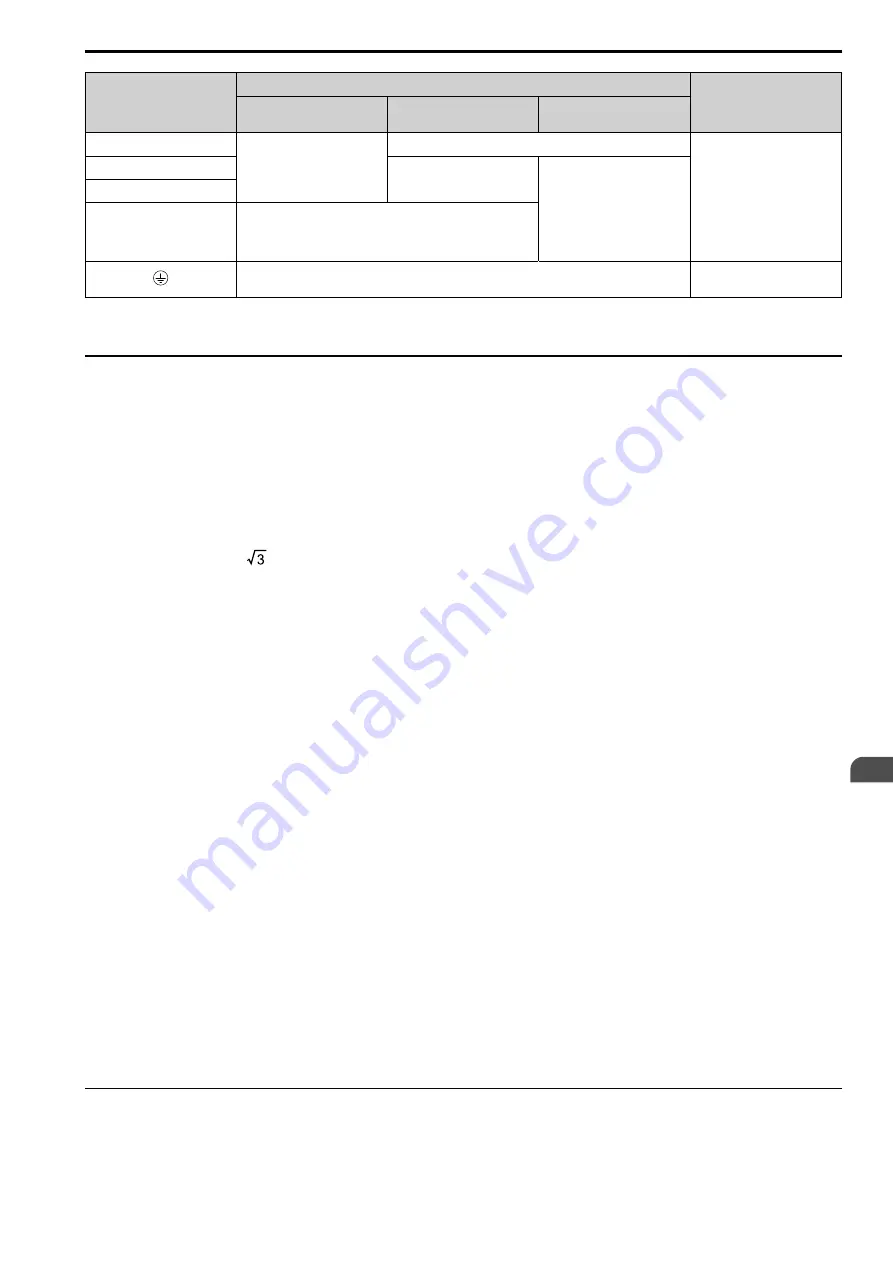
SIEPYEUOQ2A01G AC Drive Q2A Technical Manual
77
Terminals
Model
Function
2004 - 2082
4002 - 4044
2110 - 2138
4060 - 4168
2169 - 2415
4208 - 4675
+2
•
DC power supply input (+1
and -)
•
DC reactor connection (+1 and
+2)
-
To connect peripheral devices, for
example:
•
DC power input
•
Braking Unit
•
DC Reactor
Note:
Remove the jumper between
ter1 and +2 to
connect a DC reactor.
+1
DC power supply input (+1 and -)
•
DC power supply input (+1
and -)
•
Braking unit connection (+3
and -)
-
+3
-
•
200 V: D class grounding (ground to 100 Ω or less)
•
400 V: C class grounding (ground to 10 Ω or less)
To ground the drive.
Use terminals B1 and - to connect a CDBR-type control unit to drive models 2004 to 2138 and 4002 to 4168 that
have built-in braking transistors.
◆
Wire Selection
■
Wire Selection Precautions
WARNING!
Electrical Shock Hazard. The leakage current of the drive will be more than 3.5 mA. The IEC/EN 61800-5-1: 2007
standard specifies that users must wire the power supply to automatically turn off when the protective ground wire disconnects.
Users can also connect a protective ground wire that has a minimum cross-sectional area of 10 mm
2
(copper wire) or 16 mm
2
(aluminum wire). Failure to obey these standards can cause death or serious injury.
Think about line voltage drop before selecting wire gauges. Select wire gauges that drop the voltage by 2% or less
of the rated voltage. Increase the wire gauge and the cable length when the risk of voltage drops increases.
Calculate line voltage drop with this formula:
Line voltage drop (V) =
× wire resistance (Ω/km) × wiring distance (m) × motor rated current (A) × 10
-3
.
■
Precautions during Wiring
•
Use terminals B1 and - to connect braking units to drives that have built-in braking transistors (models 2004 to
2138 and 4002 to 4168). Use ter3 and - to connect braking units to drives that do not have built-in
braking transistors.
•
Refer to
“
Braking Unit, Braking Resistor Unit Instruction Manual (TOBPC72060001)
”
for information about
wire gauges and tightening torques to connect braking resistor units or braking units.
•
Use ter1 and - to connect a regenerative converter or regenerative unit.
NOTICE:
Do not connect a braking resistor to ter1 or -. Failure to obey can cause damage to the drive circuitry.
■
Notes on Wire Gauges and Tightening Torques
•
The recommended wire gauges are based on continuous current ratings of 75 °C (167 °F) 600 V class 2 heat-
resistant indoor PVC wire. Assume these conditions:
–
Ambient temperature: 40 °C (104 °F) or lower
–
Wiring distance: 100 m (3281 ft.) or shorter
–
Normal Duty Rated current value
•
Use ter1, +2, +3, -, B1, and B2 to connect a peripheral option such as a DC reactor or a braking resistor.
Do not connect other items to these terminals.
•
Refer to the instruction manual for each device for recommended wire gauges to connect peripheral devices or
options to ter1, +2, +3, -, B1, and B2. Contact the manufacturer or your nearest sales representative if
the recommended wire gauges for the peripheral devices or options are out of the range of the applicable gauges
for the drive.
Select the correct wires for main circuit wiring.
Refer to
Wire Gauges and Tightening Torques as Specified by European Standards on page 178
Refer to
Wire Gauges and Tightening Torques as Specified by UL Standards on page 201
.
◆
Main Circuit Terminal and Motor Wiring
This section outlines the various steps, precautions, and checkpoints for wiring the main circuit terminals and
motor terminals.
Содержание Q2A
Страница 2: ...This Page Intentionally Blank 2 SIEPYEUOQ2A01G AC Drive Q2A Technical Manual...
Страница 12: ...12 SIEPYEUOQ2A01G AC Drive Q2A Technical Manual...
Страница 18: ...i 2 Legal Information 18 SIEPYEUOQ2A01G AC Drive Q2A Technical Manual...
Страница 28: ...1 2 Features and Advantages of Control Methods 28 SIEPYEUOQ2A01G AC Drive Q2A Technical Manual...
Страница 64: ...2 9 Installation Methods 64 SIEPYEUOQ2A01G AC Drive Q2A Technical Manual...
Страница 166: ...4 9 Test Run Checklist 166 SIEPYEUOQ2A01G AC Drive Q2A Technical Manual...
Страница 172: ...5 2 European Standards 172 SIEPYEUOQ2A01G AC Drive Q2A Technical Manual...
Страница 173: ...Standards Compliance 5 5 2 European Standards SIEPYEUOQ2A01G AC Drive Q2A Technical Manual 173...
Страница 174: ...5 2 European Standards 174 SIEPYEUOQ2A01G AC Drive Q2A Technical Manual...
Страница 175: ...Standards Compliance 5 5 2 European Standards SIEPYEUOQ2A01G AC Drive Q2A Technical Manual 175...
Страница 176: ...5 2 European Standards 176 SIEPYEUOQ2A01G AC Drive Q2A Technical Manual...
Страница 258: ...6 2 Modbus Communications 258 SIEPYEUOQ2A01G AC Drive Q2A Technical Manual...
Страница 356: ...8 7 Storage Guidelines 356 SIEPYEUOQ2A01G AC Drive Q2A Technical Manual...
Страница 357: ...SIEPYEUOQ2A01G AC Drive Q2A Technical Manual 357 9 Disposal 9 1 Safety Precautions 358 9 2 Disposal Instructions 359...
Страница 360: ...9 2 Disposal Instructions 360 SIEPYEUOQ2A01G AC Drive Q2A Technical Manual...
Страница 526: ...11 20 Parameters Changed by PM Motor Code Selection 526 SIEPYEUOQ2A01G AC Drive Q2A Technical Manual...