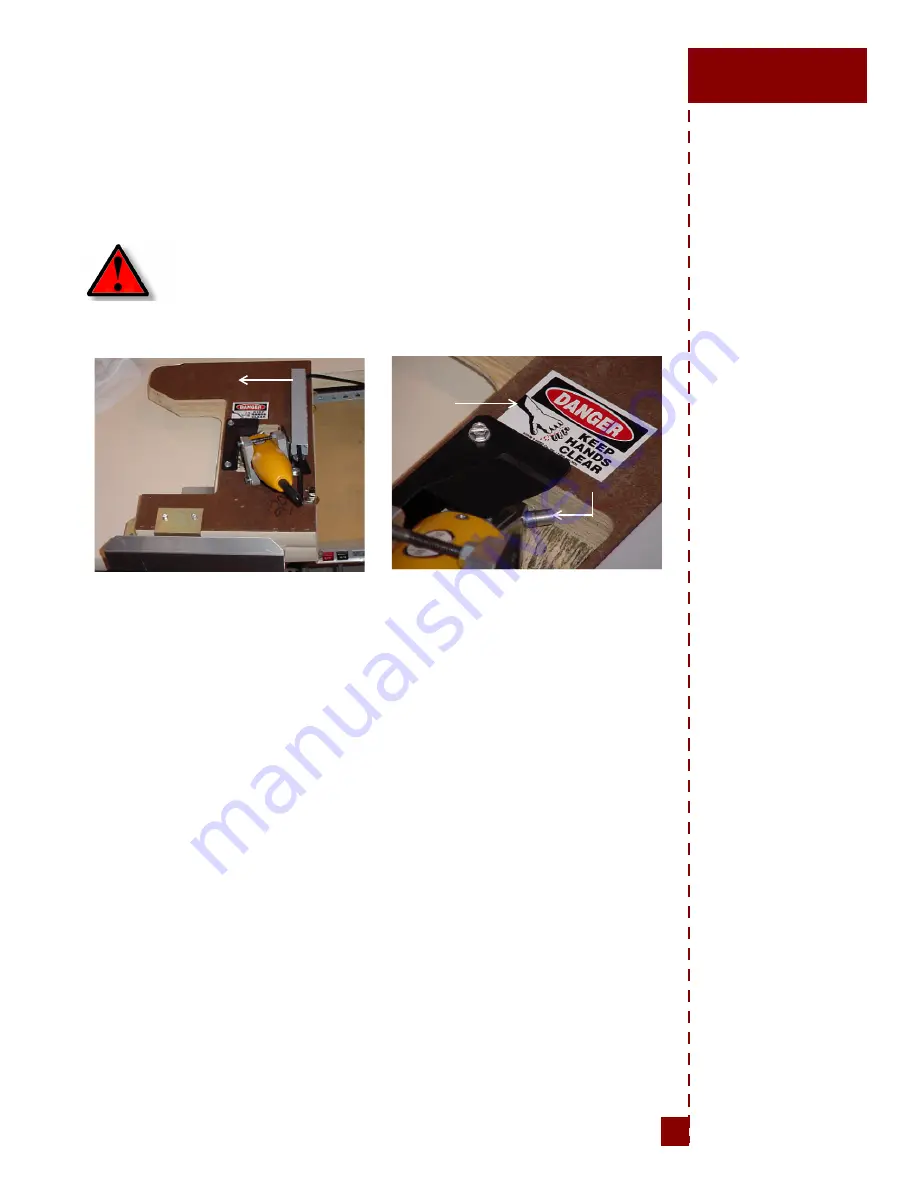
Flange Machine
Part Number 6Z8303
General Maintenance
71
4
After the blade is sharpened, release the button and lift your foot from the
flange cutter pedal.
5
Place the flange cutter section of the table back into its proper position.
Adjusting Belt Tension
Over time, you may find it necessary to adjust the tension on the motor belt.
Tension on the belt should be tight enough to keep the belt from slipping. If the
belt is too tight, this will overload and possibly damage the motor.
To adjust the belt tension:
1
Loosen the bottom nut found on the front of the motor.
2
Adjust up or down as needed.
3
After the adjustment, tighten both nuts located at the ends of the motor.
WARNING:
The rotary flange cutter blade is extremely sharp. Keep
hands and fingers clear of the rotary flange cutter while
sharpening the blade. Failure to do so could result in
serious personal injury.
Figure 8.14
Sharpening the rotary flange cutter blade
A
Move
toward
the left.
B
Always
observe
safety
decals.
sharpening button