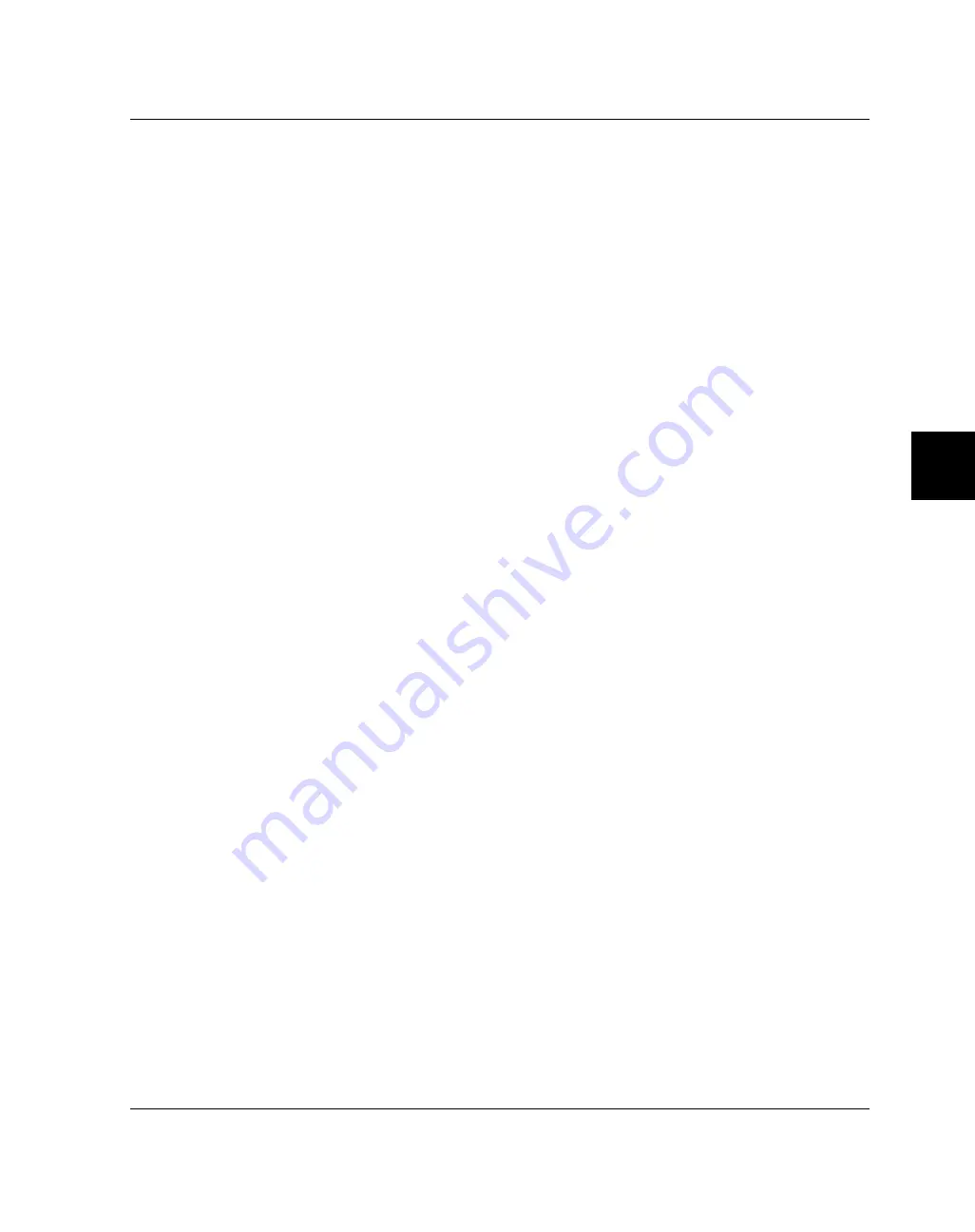
5.3
DRIVE CLUTCH OPERATION
Drive clutches primarily sense engine RPM. The two
major components which control its shifting function are
the shift weights and the coil spring. Whenever engine
RPM is increased, centrifugal force is created, causing
the shift weights to push against rollers on the moveable
sheave, which is held open by coil spring preload. When
this force becomes higher than the preload in the spring,
the outer sheave moves inward and contacts the drive
belt. This motion pinches the drive belt between the
spinning sheaves and causes it to rotate, which in turn
rotates the driven clutch.
At lower RPM, the drive belt rotates low in the drive
clutch sheaves. As engine RPM increases, centrifugal
force causes the drive belt to be forced upward on drive
clutch sheaves.
DRIVEN CLUTCH OPERATION
Driven clutches primarily sense torque, opening and
closing according to the forces applied to it from the drive
belt and the transmission input shaft. If the torque
resistance at the transmission input shaft is greater than
the load from the drive belt, the drive belt is kept at the
outer diameter of the driven clutch sheaves.
As engine RPM and horsepower increase, the load from
the drive belt increases, resulting in the belt rotating up
toward the outer diameter of the drive clutch sheaves
and downward into the sheaves of the driven clutch. This
action, which increases the driven clutch speed, is called
upshifting.
Should the throttle setting remain the same and the
vehicle is subjected to a heavier load, the drive belt
rotates back up toward the outer diameter of the driven
clutch and downward into the sheaves of the drive clutch.
This action, which decreases the driven clutch speed, is
called backshifting.
In situations where loads vary (such as uphill and
downhill) and throttle settings are constant, the drive and
driven clutches are continually shifting to maintain
optimum engine RPM. At full throttle a perfectly matched
PVT system should hold engine RPM at the peak of the
power curve. This RPM should be maintained during
clutch upshift and backshift. In this respect, the PVT
system is similar to a power governor. Rather than vary
throttle position, as a conventional governor does, the
PVT system changes engine load requirements by either
upshifting or backshifting.
SHIFT WEIGHTS
Shift weights have many factors designed into them for
controlling engagement RPM and shifting patterns. Shift
weights should not be changed or altered without first
having a thorough understanding of their positioning and
the effects they may have on belt to sheave clearance,
clutch balance and shifting pattern.
PVT BREAK-IN (DRIVE BELT / CLUTCHES)
A proper break-in of the clutches and drive belt will
ensure a longer life and better performance. Break in the
clutches and drive belt by operating at slower speeds
during the 10 hour break-in period as recommended. Pull
only light loads. Avoid aggressive acceleration and high
speed operation during the break-in period.
MAINTENANCE / INSPECTION
Under normal use the PVT system will provide years of
trouble
free
operation.
Periodic
inspection
and
maintenance is required to keep the system operating at
peak performance. The following list of items should be
inspected
and
maintained
to
ensure
maximum
performance and service life of PVT components. Refer
to the troubleshooting checklist at the end of this chapter
for more information.
• Belt Inspection
• Drive and Driven Clutch Buttons and Bushings
• Drive Clutch Shift Weights and Pins
• Drive Clutch Spider Rollers and Roller Pins
• Drive and Driven Clutch Springs
• Sheave Faces (clean and inspect for wear)
• PVT System Sealing. Refer to appropriate illustrations
on the following pages. The PVT system is air cooled
by fins on the drive clutch stationary sheave. The fins
create a low pressure area in the crankcase casting,
drawing air into the system through an intake duct. The
opening for this intake duct is located at a high point on
the vehicle (location varies by model). The intake duct
draws fresh air through a vented cover. All connecting
air ducts (as well as the PVT cover) must be properly
sealed to ensure clean air is being used for cooling the
PVT system and also to prevent water and other
contaminants from entering the PVT area. This is
especially critical on units subjected to frequent water
fording.
Содержание Sportsman 850 Touring EPS
Страница 4: ......
Страница 6: ......
Страница 72: ...2 40 NOTES MAINTENANCE ...
Страница 78: ...3 6 OIL FLOW DIAGRAM ENGINE COOLING SYSTEM ...
Страница 93: ...3 3 21 WATER PUMP ASSEMBLY TORQUE SPECIFICATIONS ENGINE COOLING SYSTEM ...
Страница 94: ...3 22 STATOR COVER ASSEMBLY TORQUE SPECIFICATIONS ENGINE COOLING SYSTEM ...
Страница 100: ...3 28 VALVE COVER ENGINE COOLING SYSTEM ...
Страница 101: ...3 3 29 CAMSHAFT CARRIER CAMSHAFT ROCKER ARM ENGINE COOLING SYSTEM ...
Страница 102: ...3 30 CYLINDER HEAD VALVES INTEGRATED THROTTLE BODY ENGINE COOLING SYSTEM ...
Страница 103: ...3 3 31 VALVE AND SPRING HEIGHT DETAIL SPM850 ENGINE COOLING SYSTEM ...
Страница 104: ...3 32 VALVE AND SPRING HEIGHT DETAIL SPM1000 ENGINE COOLING SYSTEM ...
Страница 105: ...3 3 33 PISTON CONNECTING ROD ENGINE COOLING SYSTEM ...
Страница 106: ...3 34 CRANKSHAFT ENGINE COOLING SYSTEM ...
Страница 107: ...3 3 35 CRANKCASE ENGINE COOLING SYSTEM ...
Страница 108: ...3 36 CRANKCASE UPPER ENGINE COOLING SYSTEM ...
Страница 109: ...3 3 37 BALANCE SHAFT BALANCE SHAFT TIMING ENGINE COOLING SYSTEM ...
Страница 110: ...3 38 CRANKCASE LOWER WITH OIL PUMP ENGINE COOLING SYSTEM ...
Страница 111: ...3 3 39 STATOR COVER FLYWHEEL WATER PUMP COUPLER ENGINE COOLING SYSTEM ...
Страница 112: ...3 40 WATER PUMP WATER PUMP COUPLER STATOR ENGINE COOLING SYSTEM ...
Страница 113: ...3 3 41 DRIVE COUPLER REAR STARTER GEAR ENGINE COOLING SYSTEM ...
Страница 141: ...3 3 69 CRANKCASE ASSEMBLY UPPER ENGINE COOLING SYSTEM ...
Страница 143: ...3 3 71 BALANCE SHAFT TIMING ENGINE COOLING SYSTEM ...
Страница 145: ...3 3 73 CRANKCASE SEALANT AND TORQUE VALUES ENGINE COOLING SYSTEM ...
Страница 154: ...3 82 NOTES ENGINE COOLING SYSTEM ...
Страница 160: ...4 6 FUEL TANK FUEL TANK ASSEMBLY VIEW FUEL SYSTEM ...
Страница 170: ...4 16 EFI SYSTEM LAYOUT EFI SYSTEM ASSEMBLY VIEW FUEL SYSTEM ...
Страница 204: ...4 50 NOTES FUEL SYSTEM ...
Страница 217: ...5 5 13 DRIVE CLUTCH SERVICE DRIVE CLUTCH EXPLODED VIEW ALL MODELS PVT SYSTEM ...
Страница 245: ...6 6 11 Primary Shaft Rear Output Shaft Reverse Shaft Coupler Input Shaft TRANSMISSION ...
Страница 246: ...6 12 Cam Shift Shaft Bellcrank Shift Shaft TRANSMISSION ...
Страница 254: ...6 20 TRANSMISSION EXPLODED VIEW TRANSMISSION ...
Страница 330: ...7 74 NOTES FINAL DRIVE ...
Страница 338: ...8 8 STEERING EPS STEERING ASSEMBLY VIEW EPS MODELS STEERING SUSPENSION ...
Страница 372: ...8 42 NOTES STEERING SUSPENSION ...
Страница 374: ...9 2 BRAKE SYSTEM TROUBLESHOOTING 9 25 BRAKE SYSTEM TROUBLESHOOTING 9 25 BRAKE NOISE TROUBLESHOOTING 9 26 BRAKE SYSTEM ...
Страница 377: ...9 9 5 BRAKE SYSTEM ASSEMBLY VIEWS SPORTSMAN SCRAMBLER 850 BRAKE SYSTEM BRAKE SYSTEM ...
Страница 378: ...9 6 SPORTSMAN SCRAMBLER 1000 BRAKE SYSTEM BRAKE SYSTEM ...
Страница 379: ...9 9 7 SPORTSMAN SCRAMBLER INTERNATIONAL BRAKE SYSTEM BRAKE CALIPER EXPLODED VIEW BRAKE SYSTEM ...
Страница 381: ...9 9 9 BRAKE SYSTEM ...
Страница 436: ...11 22 INSTERMENT CLUSTER TROUBLESHOOTING INSTRUMENT CLUSTER KEY OFF NO POWER ELECTRICAL ...
Страница 437: ...11 11 23 INSTRUMENT CLUSTER KEY ON NO POWER ELECTRICAL ...
Страница 438: ...11 24 INSTRUMENT CLUSTER NO HIGH BEAM INDICATOR ELECTRICAL ...
Страница 439: ...11 11 25 INSTRUMENT CLUSTER NO INCORRECT FUEL LEVEL ELECTRICAL ...
Страница 492: ...11 78 EPS TROUBLESHOOTING ELECTRICAL ...
Страница 497: ...11 11 83 BREAKOUT WIRING DIAGRAMS AWD NON ETC AWD INPUT ETC COOLING FAN CRANKSHAFT POSITION SENSOR ELECTRICAL ...
Страница 499: ...11 11 85 INTAKE AIR TEMP SENSOR NON ETC THROTTLE POSITION SENSOR NON ETC TMAP ETC TMAP NON ETC ELECTRICAL ...
Страница 500: ...11 86 NOTES ELECTRICAL ...