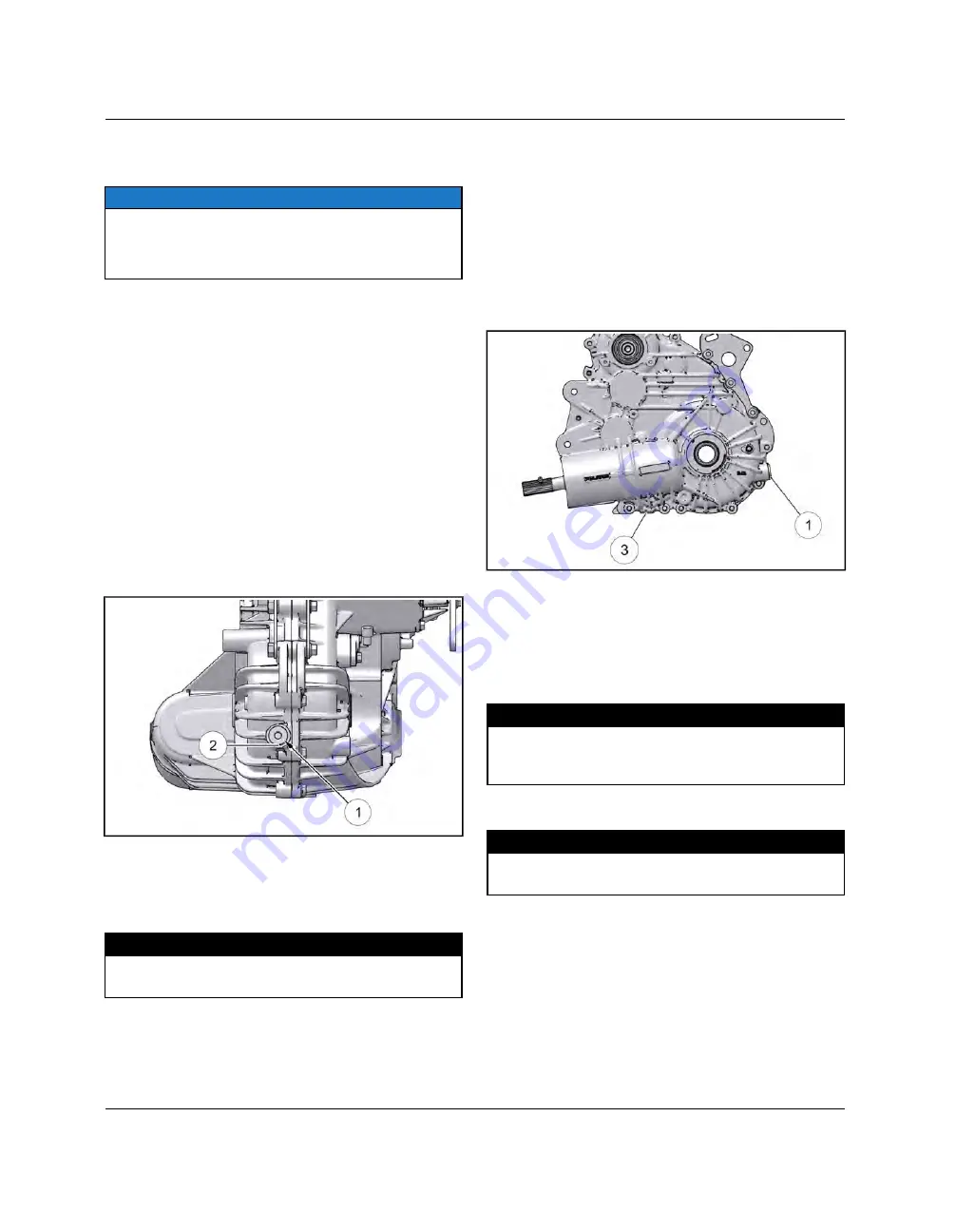
2.46
9850068 R01 - 2020-2021
RZR
PRO XP / XP 4 Service Manual
© Copyright Polaris Industries Inc.
TRANSMISSION
TRANSMISSION LUBRICATION
NOTICE
It is important to follow the transmission maintenance
intervals described in the Periodic Maintenance Chart.
Regular lubricant level inspections should be performed
as well.
The transmission lubricant level should be checked and
changed in accordance with the maintenance schedule.
• Be sure vehicle is positioned on a level surface when
checking or changing the lubricant.
• Check vent hose to be sure it is routed properly and
unobstructed.
TRANSMISSION OIL LEVEL CHECK
The fill plug is located on the rear portion of the
transmission gearcase. Access the fill plug at the rear of
the vehicle. Maintain lubricant level even with the bottom
of the fill plug hole.
1. Position vehicle on a level surface.
2. Remove the fill plug
q
and check the lubricant level.
3. If lubricant level is not even with bottom threads
w
,
add recommended lubricant as needed. Do not
overfill.
4. Reinstall the fill plug and torque to specification.
TORQUE
Transmission Fill / Drain Plug:
14 ft-lbs (19 Nm)
TRANSMISSION OIL CHANGE
The drain plug is located on the bottom of the
transmission gearcase. Access the drain plug through
the drain hole in the skid plate.
1. Remove the fill plug.
2. Place a drain pan under the transmission drain plug.
3. Remove drain plug
e
and allow lubricant to drain
completely.
4. Clean the drain plug magnetic surface.
5. Reinstall the drain plug and torque to specification.
6. Add the recommended amount of lubricant through
the fill plug hole. Maintain the lubricant level at the
bottom of the fill plug hole when filling the
transmission. Do not overfill.
FLUID CAPACITY
Recommended Transmission Lubricant:
AGL Synthetic Gearcase Lubricant
Capacity: 61 oz (1800 mL)
7. Reinstall the fill plug and torque to specification.
TORQUE
Transmission Fill / Drain Plug:
14 ft-lbs (19 Nm)
8. Check for leaks. Dispose of used lubricant properly.
Содержание RZR PRO XP 2020
Страница 3: ...REVISION INDEX REV DATE CHANGES R01 11 10 2020 Initial Release...
Страница 6: ......
Страница 10: ...1 4 9850068 R01 2020 2021 RZR PRO XP XP 4 Service Manual Copyright Polaris Industries Inc GENERAL INFORMATION...
Страница 144: ...2 58 9850068 R01 2020 2021 RZR PRO XP XP 4 Service Manual Copyright Polaris Industries Inc NOTES MAINTENANCE...
Страница 246: ...3 102 9850068 R01 2020 2021 RZR PRO XP XP 4 Service Manual Copyright Polaris Industries Inc NOTES ENGINE COOLING SYSTEM...
Страница 290: ...5 30 9850068 R01 2020 2021 RZR PRO XP XP 4 Service Manual Copyright Polaris Industries Inc NOTES EFI FUEL SYSTEM...
Страница 358: ...7 20 9850068 R01 2020 2021 RZR PRO XP XP 4 Service Manual Copyright Polaris Industries Inc NOTES TRANSMISSION...
Страница 404: ...8 46 9850068 R01 2020 2021 RZR PRO XP XP 4 Service Manual Copyright Polaris Industries Inc NOTES FINAL DRIVE...
Страница 478: ...9 74 9850068 R01 2020 2021 RZR PRO XP XP 4 Service Manual Copyright Polaris Industries Inc NOTES STEERING SUSPENSION...
Страница 587: ...Symptom and Occurrence Checklist BEEN PRESENT SINCE NEW 51...
Страница 588: ......
Страница 590: ......