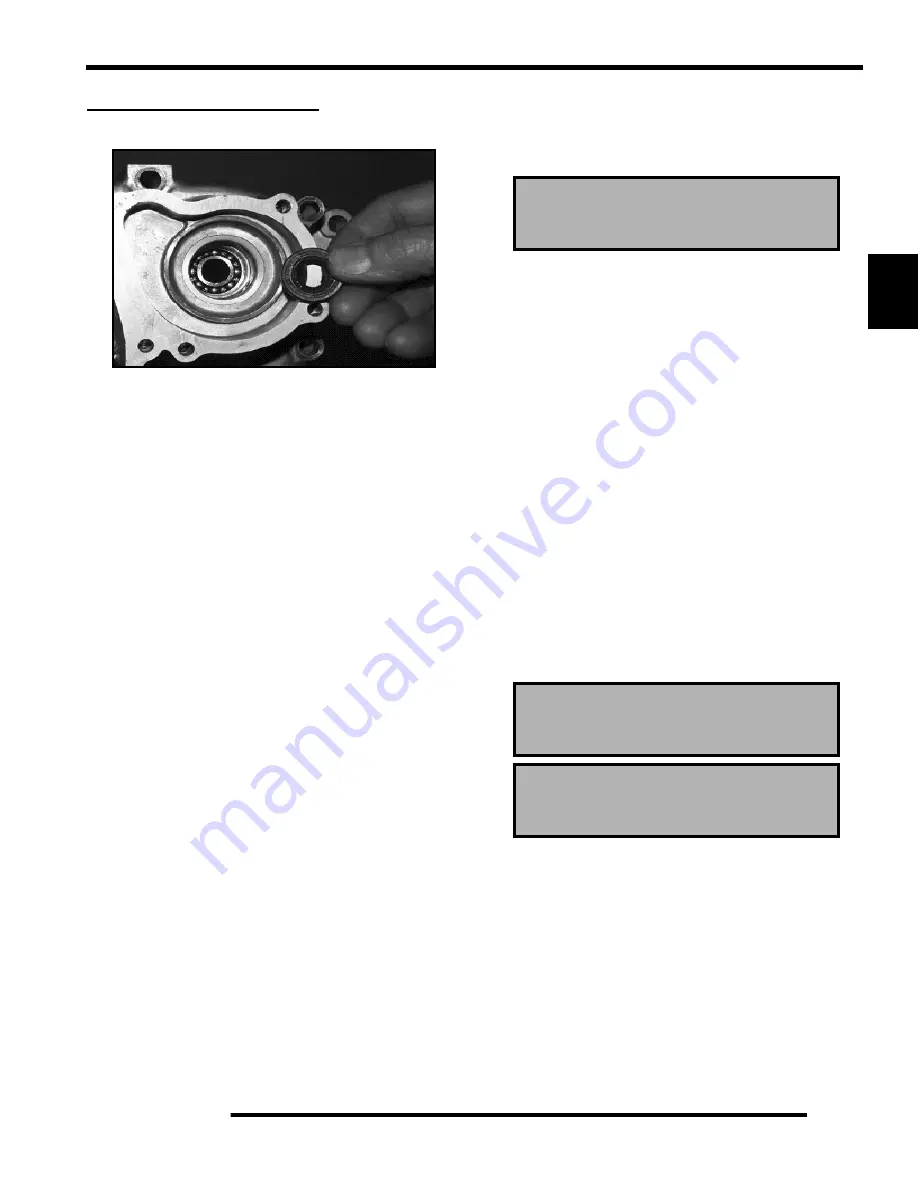
3.41
ENGINE
3
ENGINE REASSEMBLY
Pump Shaft Oil Seal Installation
1. Install the seal from the outside of the crankcase (water
pump side) with the spring facing inward, toward the pump
shaft bearing.
2. Drive or press the seal into place using a 25 mm (.985") seal
driver, until flush with the outer edge of the seal bore.
3. Lubricate the seal lip with grease.
Crankshaft / Counter Balance / Oil Pump
Installation
Lubricate all bearings with clean engine oil before assembly.
Use the Crankshaft/Water Pump Installation Kit
(PN 2871283)
to prevent damage to the crankshaft and main bearings during
installation.
1. Install the crankshaft into the PTO side crankcase. Screw
the threaded rod into the crankshaft until the threads are
engaged a minimum of one inch (25.4mm).
2. Install the collar, washer, and nut onto the threaded rod.
Hold the crankshaft and tighten the nut to draw the
crankshaft into the main bearings until fully seated. Loosen
the nut and remove the threaded rod from the crankshaft.
If removal is difficult, install two nuts on the end of the
threaded rod and tighten against each other.
3. Install the proper shim on the magneto end of the
crankshaft.
4. Place the balancer shaft in the PTO crankcase aligning the
timing marks on the crankshaft and balancer gears. Install
the proper shim washer on the shaft.
5. Inspect the oil pump sealing surface on the crankcase.
Apply a light film of engine oil to the surface and install the
oil pump.
NOTE: Do not use gasket sealer on the pump mating
surfaces.
NOTE: After engine is assembled and the vehicle is
prepared for field operation, oil pump MUST be
primed. Follow oil pump priming procedure on Page
3.12.
6. Align the drive gear with the drive pin on the pump shaft
and install the gear. Be sure the gear is fully seated and
properly engaged.
7. Install the proper shim washer on the pump shaft.
Crankcase Assembly
1.
Apply Crankcase Sealant (
PN 2871557
) to the crankcase
mating surfaces. Be sure the alignment pins are in place.
2. Set the crankcase in position carefully to avoid damaging
the pump shaft seal and install the magneto end crankshaft
installation tool (follow instructions provided with the
Crankshaft/Water Pump Installation Kit
(PN 2871283)
.
Draw the crankcase halves together by tightening the nut
on the tool and tapping lightly in the pump shaft area with
a soft faced hammer to maintain alignment. Continually
check alignment of the cases during installation, closing the
gap equally until the surfaces are tightly seated.
3. Remove the tool.
4. Install the crankcase flange bolts and tighten in 3 steps
following the pattern on Page 3.6 to specified torque.
Water Pump Mechanical Seal Installation
1. Clean the seal cavity to remove all traces of old sealer.
2. Place a new mechanical seal in the seal drive collar, and
install on the pump shaft.
3. Screw the guide onto the end of the pump shaft.
4. Install the washer and nut and tighten to draw seal into place
until fully seated.
5. Remove the guide adaptor using the additional nut as a jam
nut if necessary.
Oil Pump Bolt Torque:
6. ft. lbs. (8 Nm)
Crankcase Bolt Torque:
14 ft. lbs. (19 Nm)
Crankcase Sealant:
(PN 2871557)
Содержание Ranger 500 2x4 2007
Страница 1: ......
Страница 7: ...1 5 GENERAL INFORMATION 1 VEHICLE DIMENSIONS 113 in 287 cm 58 in 147 cm 76 in 193 cm RANGER 2X4 4X4 ...
Страница 20: ...1 18 GENERAL INFORMATION SAE Tap Drill Sizes Metric Tap Drill Sizes Decimal Equivalents ...
Страница 82: ...3 23 ENGINE 3 Cylinder Head Exploded View EH50PL EFI Shown A A ...
Страница 153: ...4 45 ELECTRONIC FUEL INJECTION 4 Fuel Pump Circuit Ignition Coil Circuit ...
Страница 154: ...4 46 ELECTRONIC FUEL INJECTION Idle Air Control IAC Circuit Throttle Position Sensor TPS Circuit ...
Страница 155: ...4 47 ELECTRONIC FUEL INJECTION 4 Manifold Air Pressure Sensor MAP Circuit Engine Coolant Temperature Sensor Circuit ...
Страница 156: ...4 48 ELECTRONIC FUEL INJECTION Intake Air Temperature Sensor IAT Circuit Malfunction Indicator Light MIL Circuit ...
Страница 157: ...4 49 ELECTRONIC FUEL INJECTION 4 Diagnostic Connector Circuit ...
Страница 296: ...10 10 ELECTRICAL POWER DISTRIBUTION MODULE NON EFI MODELS PDM Operation ...
Страница 309: ...10 23 ELECTRICAL 10 EFI Cooling System Break Out Diagram PDM RD WH Key On 12 V Power ...
Страница 331: ...10 45 ELECTRICAL 10 ELECTRICAL BREAKOUT DIAGRAMS EFI MODELS Starting Circuit Key On Power Circuit ...
Страница 332: ...10 46 ELECTRICAL Transmission Switch Circuit Differential Solenoid Circuit ...
Страница 333: ...10 47 ELECTRICAL 10 Charging System Circuit Cooling Fan Circuit ...
Страница 334: ...10 48 ELECTRICAL AWD Circuit ...
Страница 339: ...WD 1 WIRE DIAGRAM RANGER 500 2X4 4X4 CHASSIS ...
Страница 340: ...WD 2 WIRE DIAGRAM RANGER 500 2X4 4X4 DASH ...
Страница 341: ...WD 3 WIRE DIAGRAM RANGER 500 EFI 4X4 CHASSIS PAGE 1 OF 2 ...
Страница 342: ...WD 4 WIRE DIAGRAM RANGER 500 EFI 4X4 CHASSIS PAGE 2 OF 2 ...
Страница 343: ...WD 5 WIRE DIAGRAM RANGER 500 EFI 4X4 DASH ...
Страница 344: ...WD 6 WIRE DIAGRAM RANGER 500 EFI 4X4 BREAKOUTS ...
Страница 345: ...WD 7 WIRE DIAGRAM RANGER 500 2X4 4X4 BREAKOUTS ...