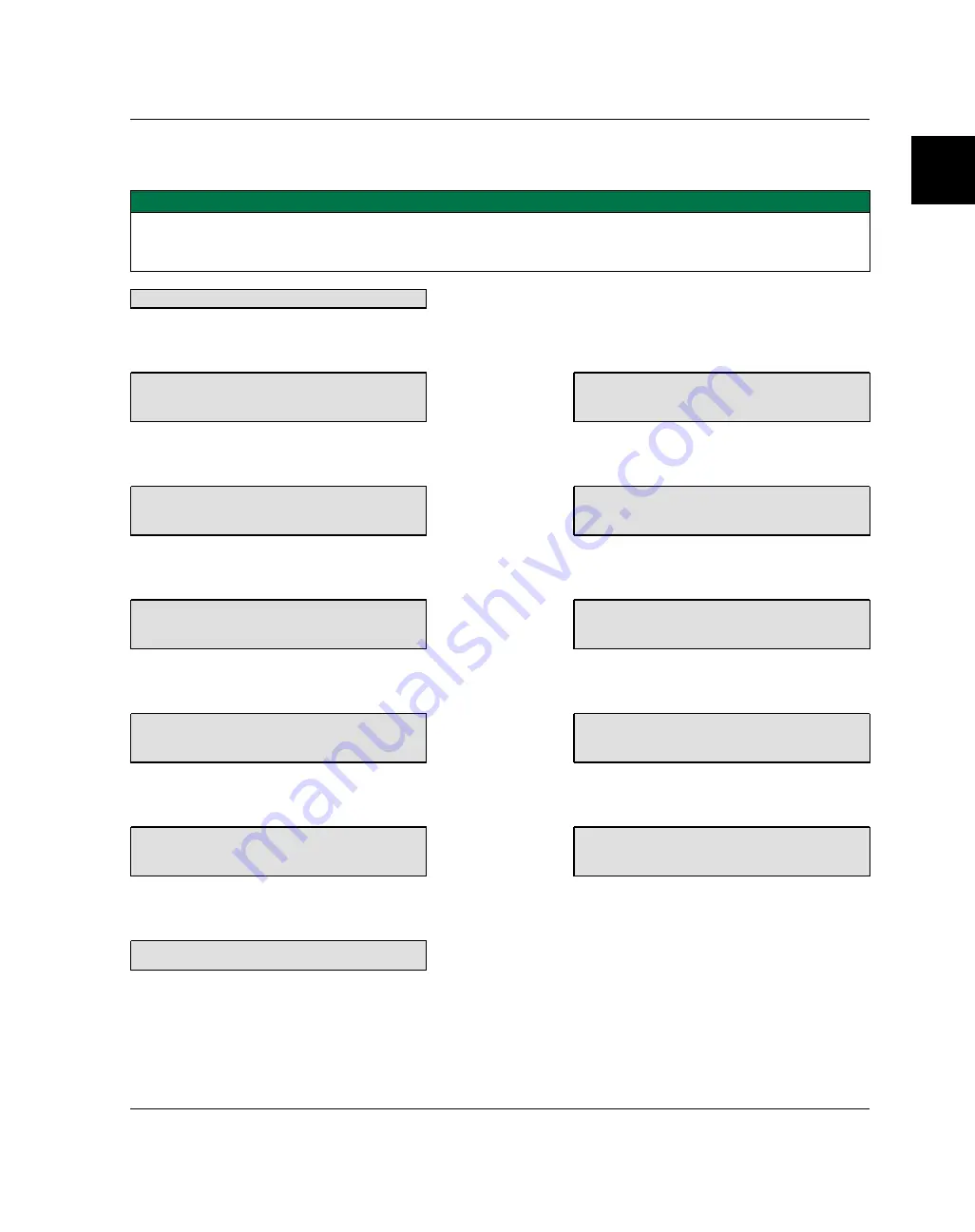
9850045 R01 - 2020-2021 RANGER 1000 Service Manual
© Copyright Polaris Inc.
1.69
STEERING / SUSPENSION DIAGNOSTICS
EPS TROUBLESHOOTING (POWER STEERING NON-FUNCTIONAL WITH MIL ON)
IMPORTANT
READ BEFORE YOU REPLACE THE EPS UNIT!
Verify the EPS unit has the latest software version and calibration loaded before replacing the EPS unit. If not, update
to the latest version for each and follow the guided diagnostic procedure(s) available in Digital Wrench®.
Power Steering Non Functional, MIL is ON
↓
Cycle the ignition switch. Is MIL on?
→
No
There is no issue. MIL on due to 5-minute
timeout. Verify code using Digital Wrench.
No
↓
Is Battery Voltage >11 and <16VDC?
→
No
Determine cause of incorrect battery voltage and
repair
Yes
↓
Is EPS Fuse OK?
→
No
Replace EPS Fuse.
Yes
↓
12 VDC and GND across 2 Pin EPS Connector
with Key On?
→
No
Check EPS Power Relay and Circuit
Yes
↓
12 VDC on Pin 3 of the 8 pin EPS Connector?
→
No
Check wiring from Connector to Ignition Switch
Circuit
Yes
↓
Begin Digital Wrench EPS Troubleshooting
Procedure
Содержание RANGER 1000 2020
Страница 4: ...REVISION INDEX REV DATE CHANGES R01 11 06 2020 Initial release...
Страница 6: ......
Страница 8: ......
Страница 88: ...1 80 9850045 R01 2020 2021 RANGER 1000 Service Manual Copyright Polaris Inc NOTES GENERAL INFORMATION...
Страница 280: ...4 34 9850045 R01 2020 2021 RANGER 1000 Service Manual Copyright Polaris Inc NOTES ENGINE ELECTRICAL...
Страница 308: ...5 28 9850045 R01 2020 2021 RANGER 1000 Service Manual Copyright Polaris Inc NOTES FUEL SYSTEM...
Страница 344: ...7 8 9850045 R01 2020 2021 RANGER 1000 Service Manual Copyright Polaris Inc SIDE VIEW TRANSMISSION...
Страница 374: ......
Страница 581: ...12 9850045 R01 2020 2021 RANGER 1000 Service Manual Copyright Polaris Inc 12 27 CHASSIS BODY ELECTRICAL...