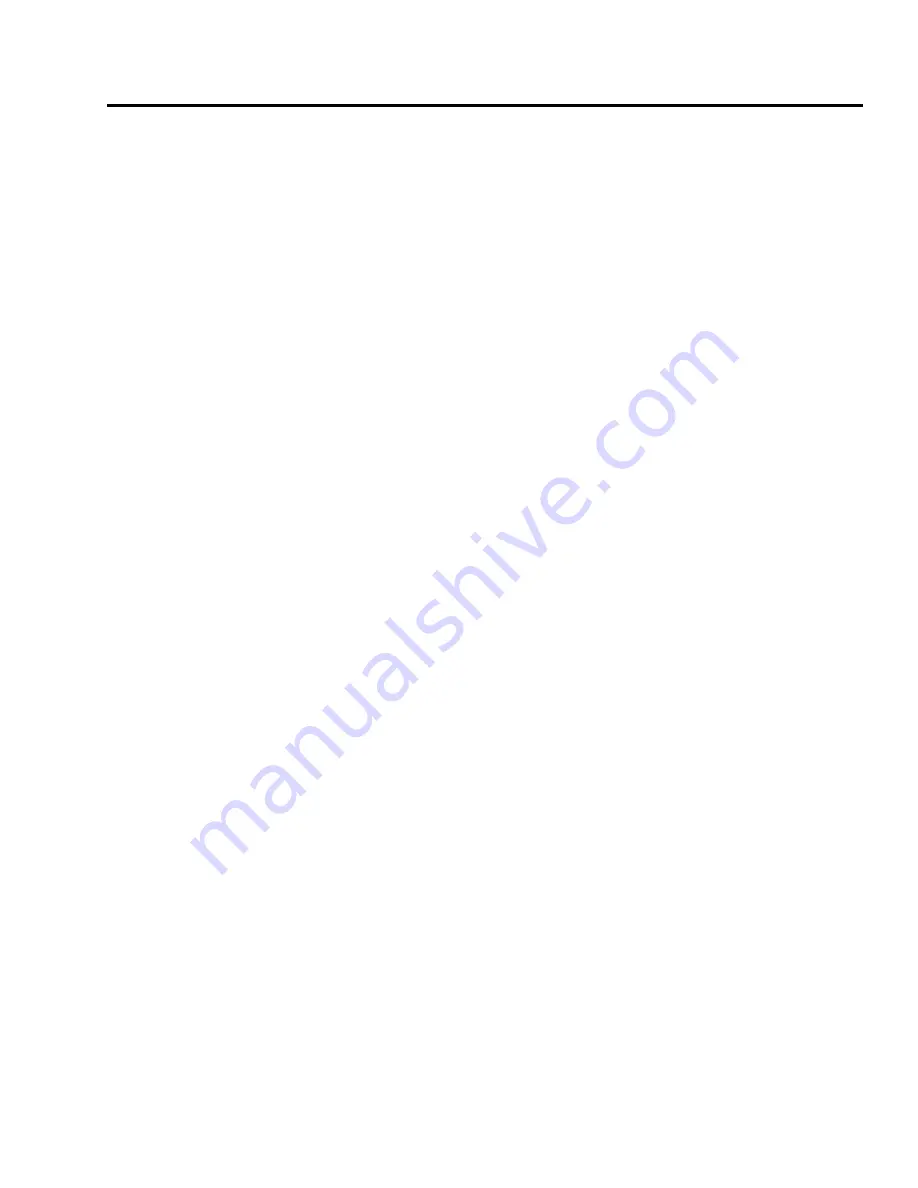
— CAUTION —
Do not introduce any trade additive to the basic lubricant unless recommended by
the engine manufacturer.
2-63. FILLING OIL SUMP. The oil sump should normally be filled with oil to the mark on the engine dipstick.
The quantity of oil required for the engines may be found in Table II-I. The specified grade of oil may be found
in Table II-III, the Lubrication Chart, or on the right cowl panel. To service the engine with oil, open the right
cowl panel, and remove the oil filler cap with dipstick.
2-64. DRAINING OIL SUMP. To drain the oil sump, provide a suitable container with a minimum capacity of
that required to fill the sump. Remove the engine cowl and open the oil drain valve located on the underside of
the engine by pushing the arms of the drain up and turning counterclockwise. This will hold the drain in the open
position. It is recommended the engine be warmed to operating temperature to insure complete draining of the
old oil.
2-65. OIL SCREENS (SUCTION). The oil suction screen, located either on the bottom aft end of the engine
sump, installed horizontally, or forward of the carburetor installed vertically. To remove both types, cut the safety
wire and remove the hex head plug. The screen should be cleaned at each oil change to remove any accumulation
of sludge and to examine for metal filings or chips. If metal particles are found in the screen, the engine should
be examined for internal damage. After cleaning and inspection, place the screen inside the recess in the hex
head plug, to eliminate possible damage to the screen. Insert the screen into the housing and when certain that
the screen is properly seated, tighten and safety the plug with MS-2099S-C41 safety wire.
2-66. OIL SCREEN (PRESSURE). The oil pressure screen, located in a housing on the accessory case of the
engine, between the magnetos, should be cleaned at each oil change to remove any accumulation of sludge and to
examine for metal filings or chips. If metal particles are found in the screen, the engine should be examined for
internal damage. When reinstalling the screen, it is recommended that a new gasket be used. Ascertain that the
screen fits flush with the base surface of the screen housing. Position housing on mounting pad and install
attachment bolts. Torque bolts within 5O to 70 inch-pounds.
2-67. OIL FILTER (FULL FLOW).
a. The oil filter element should be replaced after each 5O hours of engine operation; this is accomplished by
removing the lockwire from the bolt-head at the end of the filter housing, loosening the bolt, and removing the
filter assembly from the adapter.
b. Before discarding the filter element, cut metal housing of oil filter open using a suitable tool remove the
outer perforated paper cover, and using a sharp knife, cut through the folds of the element at both ends, close to
the metal caps. Then, carefully unfold the pleated element and examine the material trapped in the filter for
evidence of internal engine damage such as chips or particles from bearings. In new or newly overhauled
engines, some small particle of metallic shavings might be found; these are generally of no consequence and
should not be confused with particles produced by impacting, abrasion or pressure. Evidence of internal engine
damage found in the oil filter justifies further examination to determine the cause.
c. After the element has been replaced, tighten the attaching bolt within 15 to 18 foot-pounds of torque.
Lockwire the bolt through the loops on the side of the housing to the drilled head of the thermostatic valve. Be
sure the lockwire is replaced at both the attaching bolt-head and the thermostatic oil cooler bypass valve.
PIPER AIRCRAFT
PA-28-161 CADET
AIRPLANE MAINTENANCE MANUAL
Issued: FEBRUARY 28, 1989
HANDLING AND SERV I C I N G
1B23