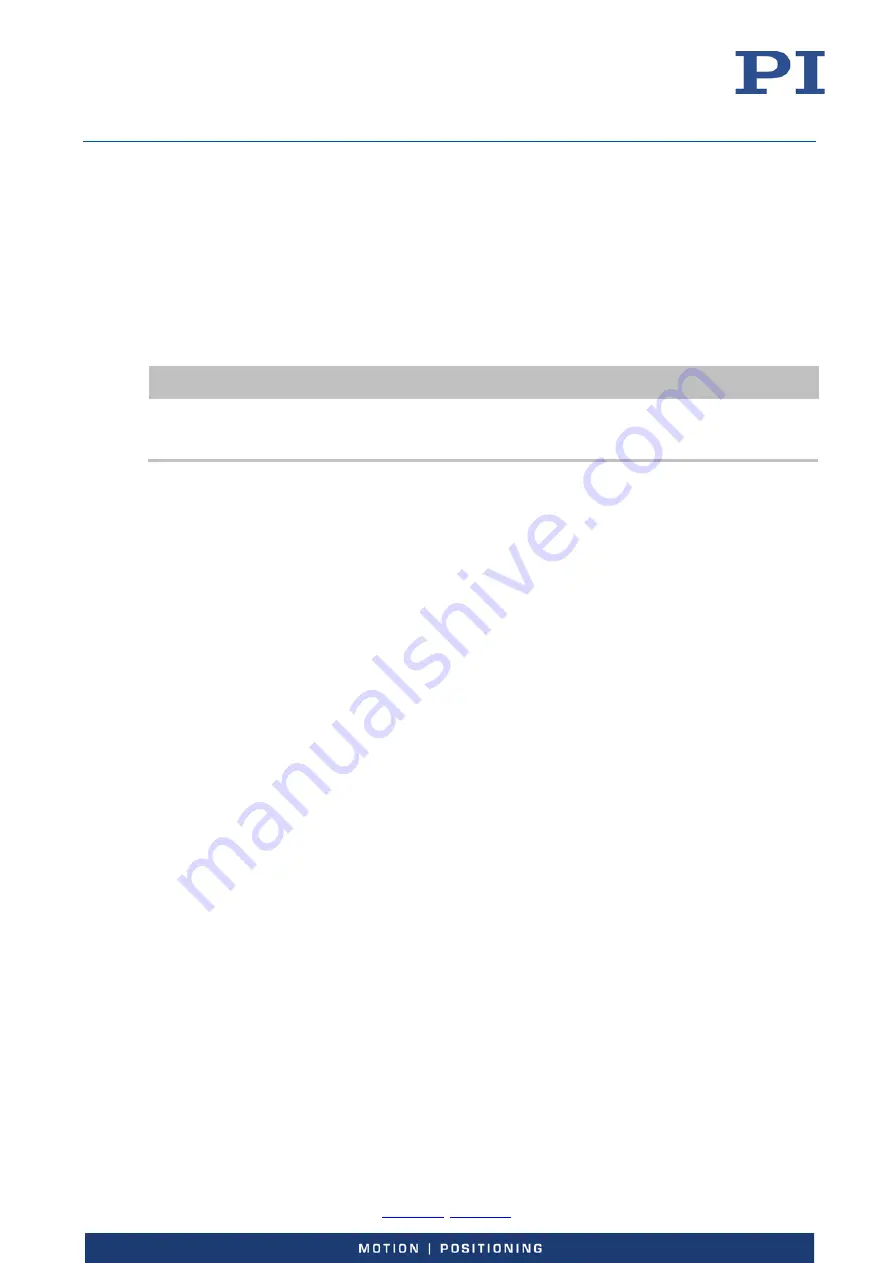
User Manual
E727T0005, valid for E-727
BRO, 2019-06-28
Physik Instrumente (PI) GmbH & Co. KG, Auf der Roemerstrasse 1, 76228 Karlsruhe, Germany
Page 140 / 240
Phone +49 721 4846-0, Fax +49 721 4846-1019, Email
Checking and Optimizing the Servo-Control Parameters
Adjusting the servo-control parameters (P-term, I-term) optimizes the dynamic properties of the
system (overshoot and settling time). The optimum settings depends on your application and your
requirements.
For further details regarding the PID algorithm, see “Control Algorithms”, p. 35.
The optimization of the servo-control parameters is typically done empirically: The response of the
axes to a step (“step response”) is analyzed under various values in closed-loop operation.
INFORMATION — SCREENSHOTS
The screenshots in the following instructions were created with an E-712 digital multi-axis
controller. With E-727, some values may differ, but the procedure outlined in the screenshots is as
with E-712.
Proceed as follows for each axis:
1.
Read the “General Notes on Servo-Controller Dynamic Tuning” (p. 134).
2.
Make sure the stage is mounted in exactly the same way as in the application. The load
on the stage is especially important.
3.
Make sure that the notch filter(s) are properly adjusted. For details, see “Adjusting the
Notch Filter(s) in Open-Loop Operation” (p. 136).
4.
In the main window of PIMikroMove, open the
Piezo Dynamic Tuner
window via the
E-
727… > Dynamic Tuner …
menu item.
5.
Configure the step response in the
Piezo Dynamic Tuner
window:
a)
Make sure that the correct axis is selected (
Axis
drop down list).
b)
Make sure that the axis is in closed-loop operation (
Servo / Closed Loop
box is
checked).
c)
Enter suitable values for the start value (
Offset:
) and the amplitude (
Amplitude:
) of
the step in the
Step
panel. The start value should be 0, and the amplitude should be
about 10 % of the axis travel range.
d)
By clicking the
Optimize Recording
button in the
Step
panel, optimize the number
of data recorder points that will be read from the controller when the step
response has been performed.
e)
If you want to compare the results of multiple step resonse measurements, check
the
Show history
box and select the number of old recordings to be displayed.