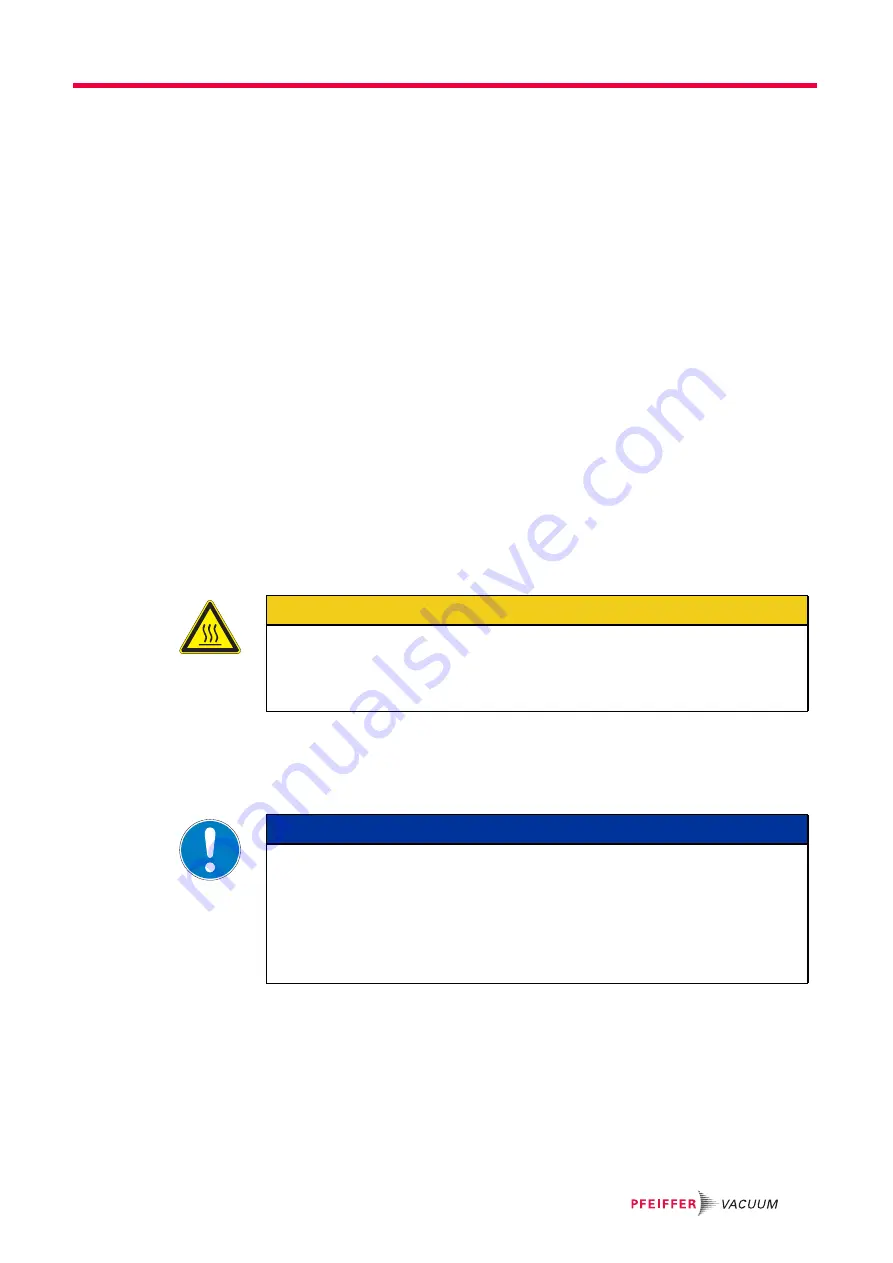
Operation
17
6 Operation
6.1 Before switching on the pump
Check the operating fluid level in the sight glass.
Compare the voltage and frequency information on the rating plate with the mains volt-
age and frequency values.
Check that the exhaust connection allows free flow (max. permissible pressure 150
kPa absolute).
– Activate the shut-off valves in such a way that they open before or at the same time
as the pump is started.
Protect the pump sufficiently from taking in contaminants by means of suitable precau-
tions (e.g. dust filters); if necessary, check operating fluid regularly or replace at short-
er intervals.
6.2 Switching on the pump
The pump can be switched on in any pressure range between atmospheric and
ultimate pressure.
No special precautions are necessary when pumping dry gases. In order to attain the
lowest possible ultimate pressures, the gas ballast valve should be closed.
Switch on pump at main switch 15.
Switch on the pump with the vacuum flange closed and allow to warm up for 30 min-
utes.
6.3 Pumping condensable vapours
Should the process gases contain condensable gases present at high percentages, the
rotary vane pump must be operated with gas ballast (i.e. with an open gas ballast valve).
Gas ballast valve,
standard version
To avoid condensation in the pump when pumping condensable vapours, air is periodi-
cally fed into the working chamber at the beginning of the compression phase via the gas
ballast valve 42.
The gas ballast valve is closed when turning to the right to position 0 and open when turn-
ing to the left to position 1. Intermediate settings are not possible.
CAUTION
Hot surface!
Danger of burns if hot parts are touched. Depending on the operating and ambient con-
ditions, the surface temperature of the pump may rise above 70 °C.
In this case, use suitable finger guards.
NOTICE
Bad final vacuum and damage to the pump!
Danger of condensation and corrosion due to exceeding the water vapour compatibility
during operation without gas ballast or in case of insufficient supply of flushing gas.
Only pump vapours when the pump is warm and the gas ballast valve is open.
When the process has been completed, allow the pump to continue running for
about 30 minutes with the vacuum flange closed and the gas ballast open for ope-
rating fluid regeneration purposes.