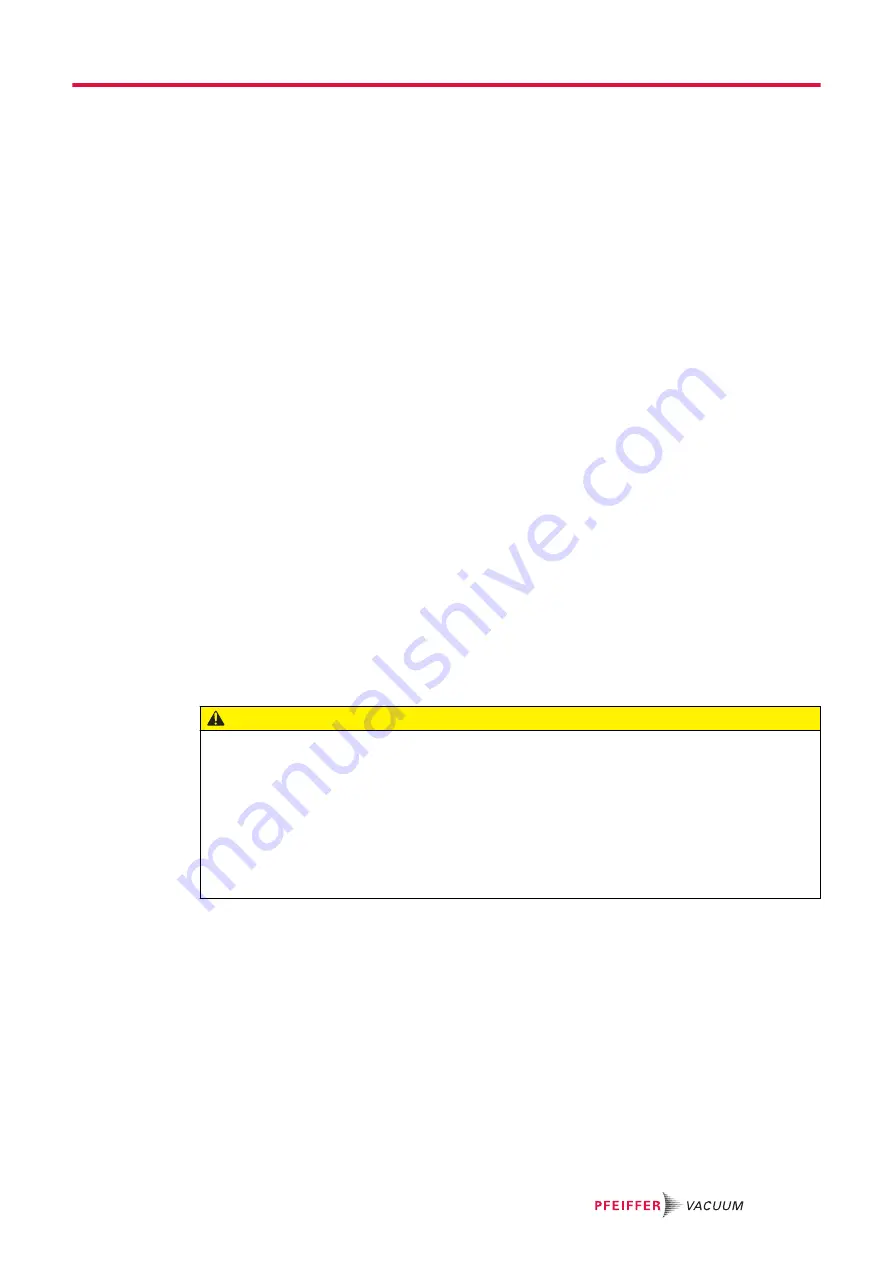
5 Installation
The rotor of the turbopump revolves at very high speed. In practice it is not possible to exclude the risk
of the rotor touching the stator (e.g. due to the penetration of foreign bodies into the high vacuum con-
nection). The kinetic energy released acts on the housing and on the anchoring of the turbopump within
fractions of a second. This makes the stability of the turbopump and its fastenings extremely important.
Comprehensive tests and calculations conforming to ISO 27892 confirm the safety of the turbopump
both against crashes (destruction of the rotor blade) and against bursting (breakage of the rotor shaft).
The experimental and theoretical results are expressed in safety measures and recommendations for
the correct and safe fastening of the turbopump.
5.1 Preparatory work
Preliminary note
► Choose an installation location that permits access to the pumping station and to supply lines at
all times.
Prerequisites
● The given ambient conditions
● level, vibration-free surface
● Distance to side walls or adjacent devices: at least 50 cm
● Distance to free table edges min. 10 cm
● when using a housing heater and water cooling, the temperature on the connection flange on the
vacuum chamber is not permitted to exceed 120 °C
Choosing the installation location
1. Ensure adequate cooling options for the pumping station.
2. Install suitable protective shielding if ambient magnetic fields occur that are higher than the maxi-
mum permitted.
3. Install suitable protective shielding to prevent the radiated heat output exceeding the permissible
values when high temperatures arise due to the processes involved.
5.2 Setting up the pumping station
CAUTION
Cutting injuries on sharp and rotating parts with the high vacuum flange open during installa
tion
With the high vacuum flange open, access to sharp-edged parts is possible. There is a risk of cutting
injuries. Objects falling inside destroy the pump during subsequent operation.
► Only remove the original protective cover immediately before connecting the high vacuum flange.
► Do not reach into the high vacuum flange.
► Wear protective gloves during the installation process.
► Do not put the pump into operation with the vacuum flanges open.
► Ensure that the mechanical installation is completed before the electrics are connected.
General notes for the installation of vacuum components
► Choose an installation location that permits access to the product and to supply lines at all times.
► Observe the ambient conditions named for the area of use.
► Provide the highest possible level of cleanliness during assembly.
► Ensure that flange components during installation are grease-free, dust-free and dry.
Installation
19/56