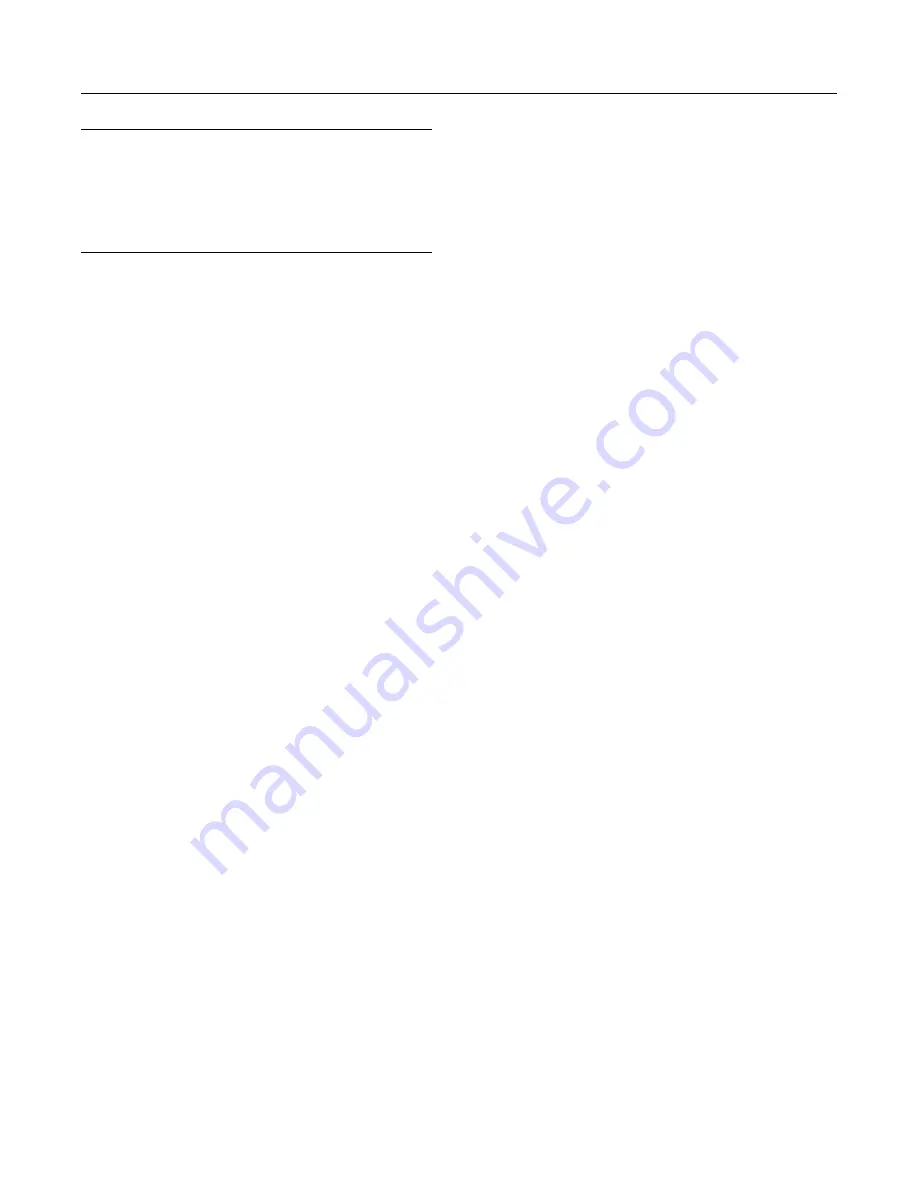
NOTICE
The fuels system has been qualified with fuel having
lubricity up to 0.52 mm (0.0205 inch) wear scar diam-
eter as tested by “ISO 12156-1”. Fuel with higher
wear scar diameter than 0.52 mm (0.0205 inch) will
lead to reduced service life and premature failure of
the fuel system.
Fuel additives can enhance the lubricity of a fuel.
Contact your fuel supplier for those circumstances
when fuel additives are required. Your fuel supplier
can make recommendations for additives to use, and
for the proper level of treatment.
Distillation
Distillation is an indication of the mixture of different
hydrocarbons in the fuel. A high ratio of lightweight
hydrocarbons can affect the characteristics of
combustion.
Recommendation for Biodiesel and
Using B20
Biodiesel is a fuel that can be defined as mono-alkyl
esters of fatty acids. Biodiesel is a fuel that can be
made from various feedstocks. The most commonly
available biodiesel in Europe is Rape Methyl Ester
(RME). This biodiesel is derived from rapeseed oil.
Soy Methyl Ester (SME) is the most common
biodiesel in the United States. This biodiesel is
derived from soybean oil. Soybean oil or rapeseed oil
are the primary feedstocks. These fuels are together
known as Fatty Acid Methyl Esters (FAME).
Raw pressed vegetable oils are NOT acceptable for
use as a fuel in any concentration in compression
engines. Without esterification, these oils solidify in
the crankcase and the fuel tank. These fuels may not
be compatible with many of the elastomers that are
used in engines that are manufactured today. In
original forms, these oils are not suitable for use as a
fuel in compression engines. Alternate base stocks
for biodiesel may include animal tallow, waste
cooking oils, or various other feedstocks. To use any
of the products that are listed as fuel, the oil must be
esterified.
Fuel made of 100 percent FAME is generally referred
to as B100 biodiesel or neat biodiesel.
Biodiesel can be blended with distillate diesel fuel.
The blends can be used as fuel. The most commonly
available biodiesel blends are B5, which is 5 percent
biodiesel and 95 percent distillate diesel fuel. B20,
which is 20 percent biodiesel and 80 percent distillate
diesel fuel.
Note:
The percentages given are volume-based.
The U.S. distillate diesel fuel specification “ASTM
D975-09a” includes up to B5 (5 percent) biodiesel.
European distillate diesel fuel specification EN590:
2010 includes up B7 (7 percent) biodiesel.
Note:
Engines that are manufactured by Perkins are
certified by use of the prescribed Environmental
Protection Agency (EPA) and European Certification
fuels. Perkins does not certify engines on any other
fuel. The user of the engine has the responsibility of
using the correct fuel that is recommended by the
manufacturer and allowed by the EPA and other
appropriate regulatory agencies.
Specification Requirements
The neat biodiesel must conform to the latest
“EN14214 or ASTM D6751” (in the USA). The
biodiesel can only be blended in mixture of up to 20%
by volume in acceptable mineral diesel fuel meeting
latest edition of “EN590 or ASTM D975 S15”
designation.
In United States Biodiesel blends of B6 to B20 must
meet the requirements listed in the latest edition of
“ASTM D7467” (B6 to B20) and must be of an API
gravity of 30-45.
In North America biodiesel and biodiesel blends must
be purchased from the BQ-9000 accredited
producers and BQ-9000 certified distributors.
In other areas of the world, the use of biodiesel that is
BQ-9000 accredited and certified, or that is
accredited and certified by a comparable biodiesel
quality body to meet similar biodiesel quality
standards is required.
Engine Service Requirements
Aggressive properties of biodiesel fuel may cause
debris in the fuel tank and fuel lines. The aggressive
properties of biodiesel will clean the fuel tank and fuel
lines. This cleaning of the fuel system can
prematurely block of the fuel filters. Perkins
recommend that after the initial usage of B20
biodiesel blended fuel the fuel filters must be
replaced at 50 hours.
Glycerides present in biodiesel fuel will also cause
fuel filters to become blocked more quickly. Therefore
the regular service interval should be reduced to 250
hours.
When biodiesel fuel is used, crank case oil and
aftertreatment systems may be influenced. This
influence is due to the chemical composition and
characteristics of biodiesel fuel, such as density and
volatility, and to chemical contaminants that can be
present in this fuel, such as alkali and alkaline metals
(sodium, potassium, calcium, and magnesium).
64
SEBU9075-03