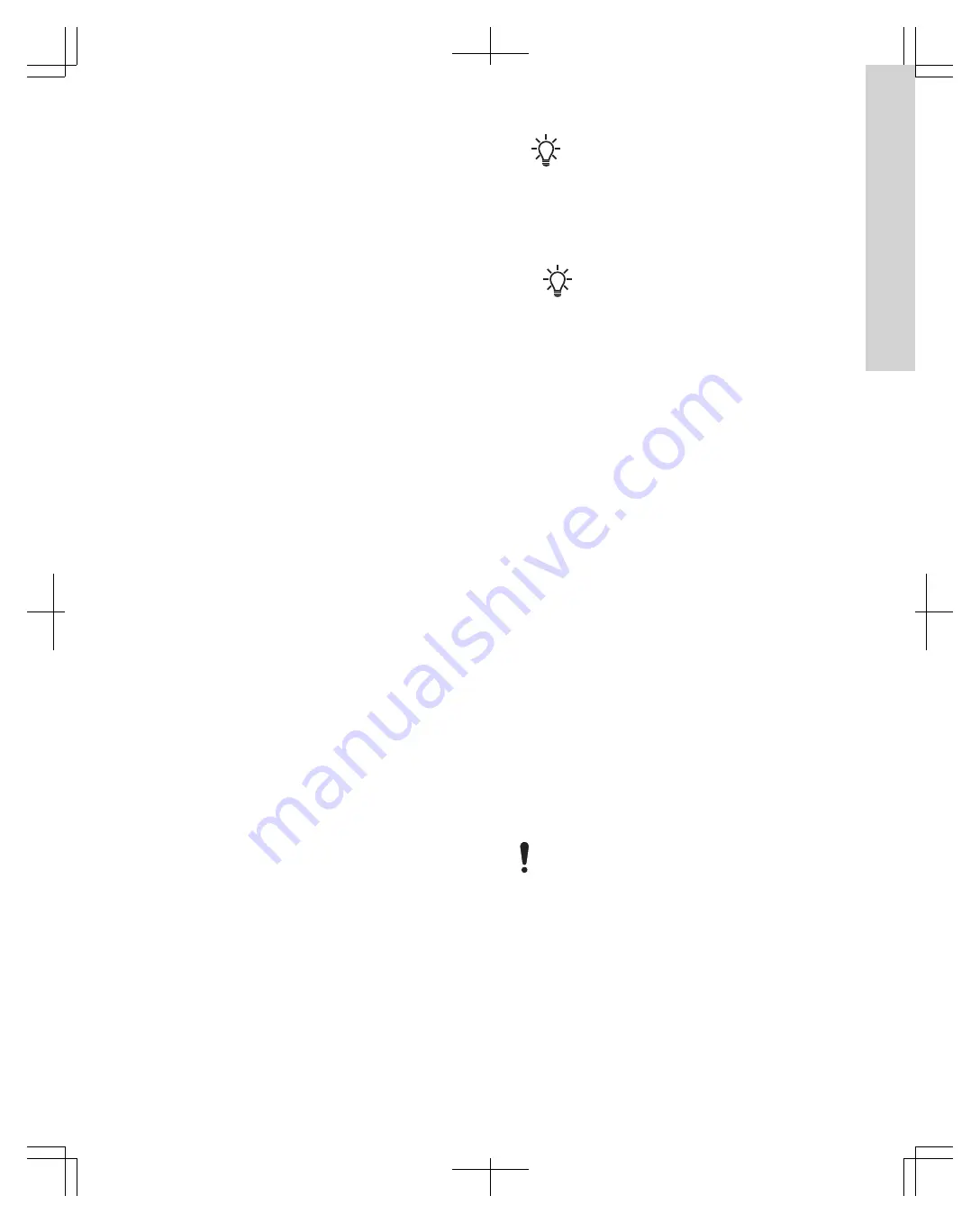
6.
Remove plug from bottom of casing and drain casing.
7.
Disconnect inlet and outlet lines.
The pump need not be disconnected from inlet and outlet pipes
for disassembly.
6
.6.1
Dismantling for base mounted pump
If pump is mounted on the base, remove the base hold-down bolts
and move pump to bench for disassembly.
1.
Remove any seal pipes (tubing) between pump discharge and
stuffing box of adapter (Item 11, Figure 1).
2.
Remove cap screws holding the adapter (11) to casing (1).
Before removing rotating assembly, scribe assembly marks on
casing, motor, and adapter flanges so that the unit can be
reassembled in the same orientation. Remove complete
rotating assembly by lifting motor from casing.
3.
Insert a rod of suitable diameter into a passage of impeller (2)
and hold while loosening impeller lockscrew (26). Remove
screw and impeller washer (24A).
4.
Slide impeller from end of shaft (6) and remove impeller key
(32). If it is necessary to pry the impeller off, use a gear or
wheel puller so that force is exerted on the motor shaft and not
the motor bearings. Pry evenly on opposite sides of impeller
where bending or denting of impeller shrouds will not occur.
5.
Loosen the gland bolts (17B) and pull gland (17) out slightly to
relax packing (13).
6.
Remove screws and slide adapter (11) off from shaft. Use care
not to scratch shaft sleeve (14).
7.
Remove gland (17), packing (13) and lantern ring (29), if
furnished, from the adapter.
8.
Slide shaft sleeve (14). O-ring and deflector from shaft.
9.
Remove casing ring (7) from casing only if damaged or worn to
excess (refer to Repair).
6
.7
Wear ring
Wear rings decrease the clearance between the impeller and volute
to reduce the quantity of liquid leaking from the high-pressure zone,
outlet, and the low-pressure zone, inlet. The rings are designed to
use the pumped liquid for lubrication and to be replaced when worn
to maintain optimal pump performance and service.
As the rings wear, the clearance between the impeller and
the volute increases as does the amount of liquid leaking from the
high-pressure to the low-pressure zone. The rate of wear depends
on the characteristics of the pumped liquid. The pump will typically
have a volute wear ring and can also have an impeller wear ring.
Badly worn wear rings will result in severe degradation of pump
performance: head and flow rate, especially on small
pumps. Examination of wear patterns can provide valuable
information to diagnose pump performance or maintenance issues
and determining the source of a problem.
6
.8
Replacing the wear ring
Standard pumps are not supplied with impeller wear rings, and they
can be installed in the field. The wear surface of the impeller is an
integral part of the impeller. Impellers with worn surfaces that
cannot be fitted with wear rings must be replaced.
Use the following steps to determine if the wear rings must be
replaced:
1.
Measure the outer diameter (OD) of the impeller wear surface
or wear ring (8) and the inner diameter (ID) of the volute wear
ring (7).
2.
Compute the diametrical clearance, ID minus OD, and
compare them with the allowed diametrical clearance.
3.
If the measured clearance is out of tolerance, proceed as
follows:
Ensure the ID of the volute ring is concentric with the
wear ring OD, and the surface is smooth.
a. Replace the volute wear ring and impeller wear ring if the
measured clearance is two times the maximum allowed
clearance.
Machining the impeller wear surface may be
necessary to install or replace the impeller wear
rings. Ensure that the impeller OD is not reduced
and is concentric with the bore of the impeller.
Bronze impeller rings are shrink-fitted onto the hub
according to ANSI B4.1 [FN-4].
Hardened impeller rings are installed according to
ANSI B4.1 [FN-1].
b. Replace the volute wear ring if the measured clearance is
out of tolerance.
6
.9
Inspecting the product
Visually inspect parts for damage affecting serviceability or sealing.
Emphasize inspection of mating parts having relative motion wear
rings, for example. Perform detail inspection as follows:
1.
Check O-rings and bearing cover gaskets for cracks, nicks, or
tears; packing rings for excessive compression, fraying or
shredding, embedded particles (dirt or metal). Replace if
defective in any way.
2.
Examine impeller passages for cracks, dents, gouges or
embedded material.
3.
If the pump capacity falls off due to wear on the impeller and
casing ring, repair is made by replacing the casing ring. The
inside diameter of the casing ring should be a minimum of
0.015" larger than the impeller skirt diameter.
4.
Normally, when the pump is completely disassembled, all
gaskets, O-rings and seals should be replaced at reassembly.
If the O-ring for the floating seat is not damaged, it may be
reused with the other, satisfactory seal parts.
Replace all packing rings (13). Replace shaft sleeve (14) if
wear has been detected upon inspection.
6
.10
Repairing the product
Make necessary repairs in the following manner:
1.
If ID on casing rings (7) is grooved, scored or eccentric, replace
the casing rings.
2.
If impeller wear surfaces are defective.
3.
Replace worn shaft sleeve.
6
.11
Assembling the pump
Avoid damaging any components and avoid
contamination (dirt, debris, moisture, etc.) of the unit.
Reassemble pump in the following manner:
1.
Install deflector and shaft sleeve (14) on shaft. Be sure that
sleeve bottoms on shaft shoulder. Position deflector midway
between end of sleeve and grease retainer. Align sleeve slot
with key slot of shaft.
2.
Install deflector (40), shaft sleeve "0" ring (130) and shaft
sleeve (14) on shaft. Make sure shaft sleeve bottoms on shaft
shoulder. Position deflector on motor shaft about midpoint
between gland and motor register within adapter. Align shaft
sleeve slot with key slot of shaft, slide gland (17) and lantern
ring (29), if furnished, onto the shaft to about the deflector.
1
7
English (US)