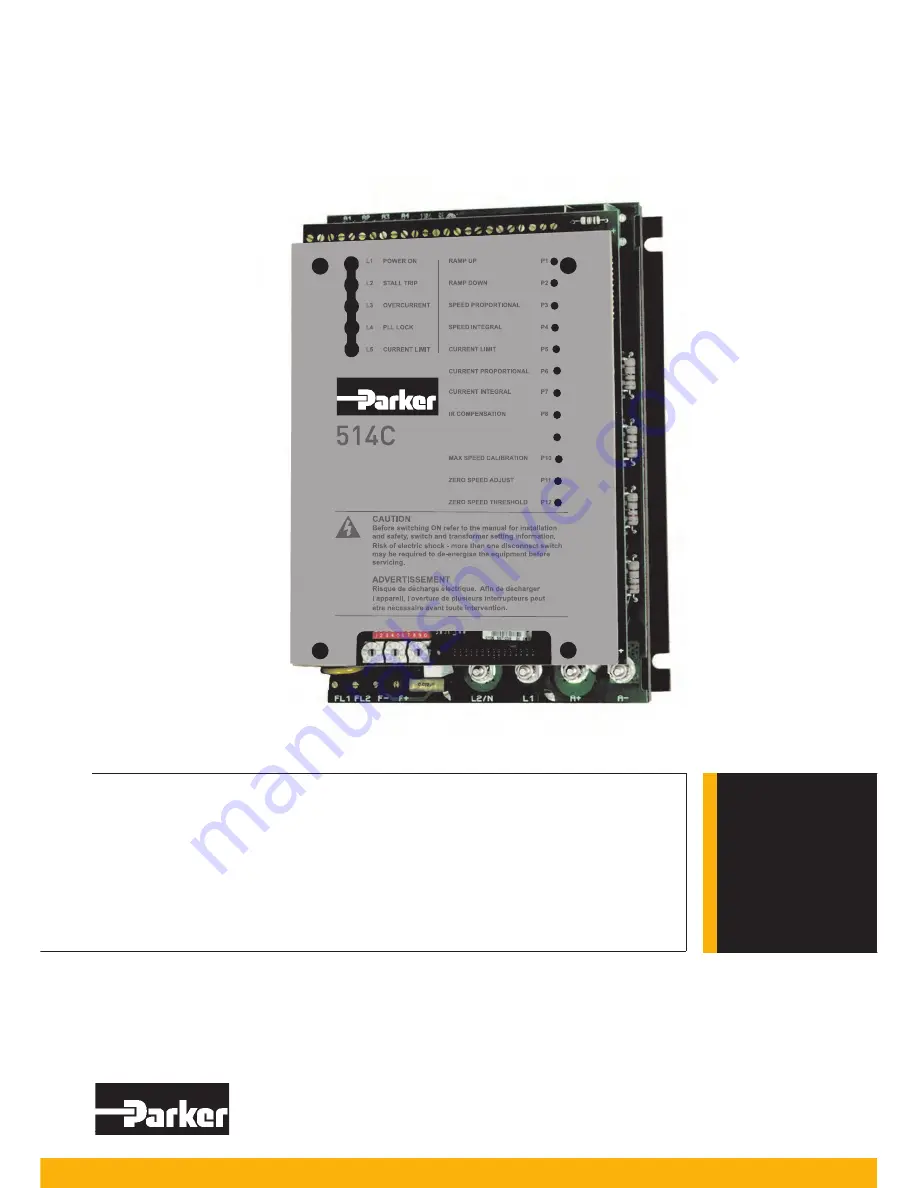
514C
DC Controller
HA463296 Issue 8
Technical Manual
aerospace
climate control
electromechanical
filtration
fluid & gas handling
hydraulics
pneumatics
process control
sealing & shielding
ENGINEERING
YOUR
SUCCESS.
This manual was downloaded on www.sdsdrives.com
+44 (0)117 938 1800 - [email protected]