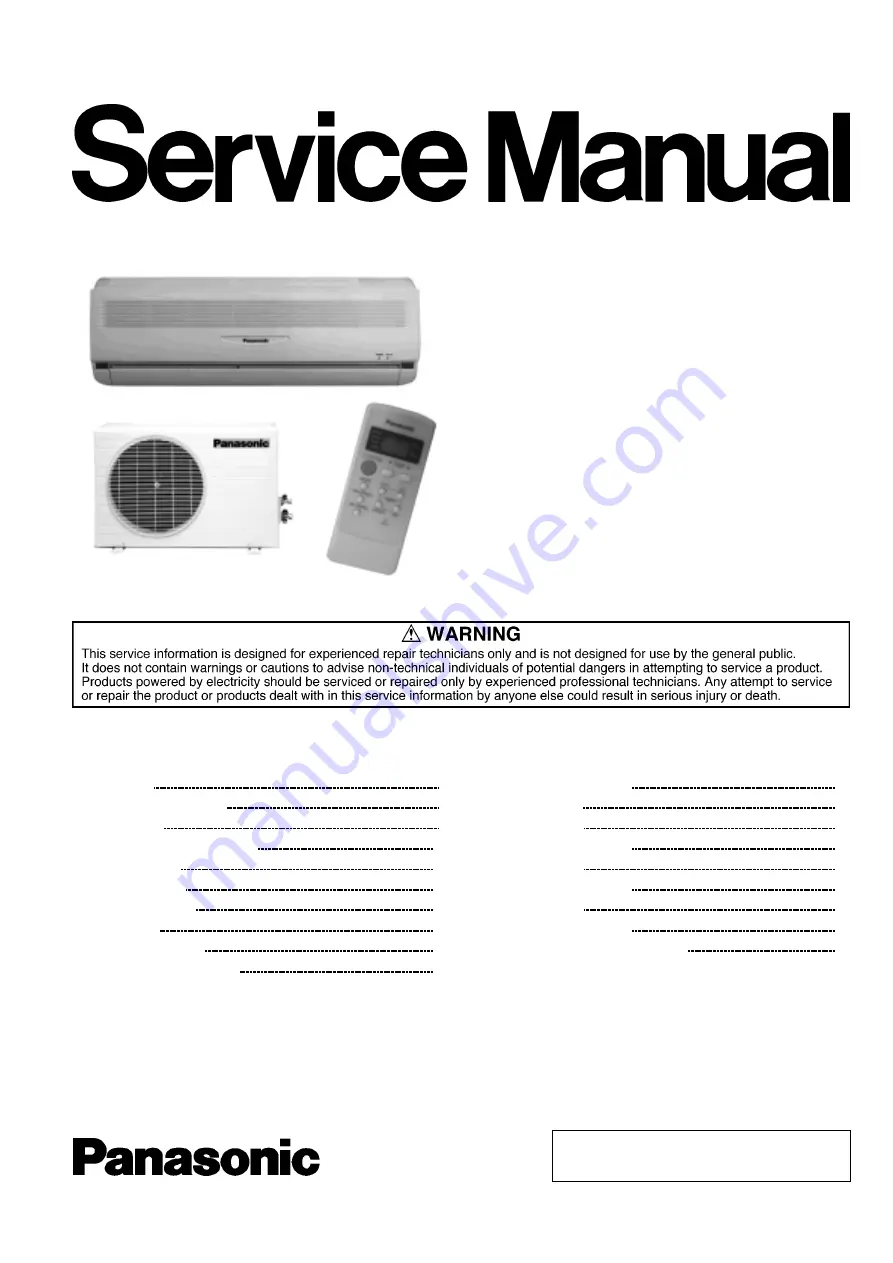
1
Functions
2
2
Product Specifications
5
3
Dimensions
9
4
Refrigeration Cycle Diagram
12
5
Block Diagram
13
6
Wiring Diagram
14
7
Operation Details
15
8
Installation
22
9
2-way, 3-way Valve
36
10 Disassembly of the parts
43
© Guangzhou Matsushita Air Conditioner Co., Ltd.
(GMAC) All rights reserved. Unauthorized copying
and distribution is a violation of law.
CS-PC9CKV CU-PC9CKV
CS-PC12CKV CU-PC12CKV
11 Trouble-shooting guide
47
12 Technical Data
49
13 Exploded View
51
14 Replacement Parts List
52
15 Exploded View
53
16 Replacement Parts List
54
17 Exploded View
55
18 Replacement Parts List
56
19 ELECTRONIC CIRCUIT DIAGRAM
57
Room Air Conditioners
CONTENTS
Page
Page
Order No: GMAC0401004C3
Содержание CS-PC12CKV
Страница 9: ...3 Dimensions 9 CS PC9CKV CU PC9CKV CS PC12CKV CU PC12CKV ...
Страница 10: ...10 CS PC9CKV CU PC9CKV CS PC12CKV CU PC12CKV ...
Страница 11: ...11 CS PC9CKV CU PC9CKV CS PC12CKV CU PC12CKV ...
Страница 12: ...4 Refrigeration Cycle Diagram 4 1 CS CU PC9CKV CS CU PC12CKV 12 CS PC9CKV CU PC9CKV CS PC12CKV CU PC12CKV ...
Страница 13: ...5 Block Diagram 5 1 CS CU PC9CKV CS CU PC12CKV 13 CS PC9CKV CU PC9CKV CS PC12CKV CU PC12CKV ...
Страница 14: ...6 Wiring Diagram 6 1 CS CU PC9CKV CS CU PC12CKV 14 CS PC9CKV CU PC9CKV CS PC12CKV CU PC12CKV ...
Страница 18: ...Time Graph for soft dry operation 18 CS PC9CKV CU PC9CKV CS PC12CKV CU PC12CKV ...
Страница 23: ...23 CS PC9CKV CU PC9CKV CS PC12CKV CU PC12CKV ...
Страница 50: ...Q Q Q Q Cooling characteristics 50 CS PC9CKV CU PC9CKV CS PC12CKV CU PC12CKV ...
Страница 51: ...13 Exploded View 51 CS PC9CKV CU PC9CKV CS PC12CKV CU PC12CKV ...
Страница 53: ...15 Exploded View 53 CS PC9CKV CU PC9CKV CS PC12CKV CU PC12CKV ...
Страница 55: ...17 Exploded View 55 CS PC9CKV CU PC9CKV CS PC12CKV CU PC12CKV ...
Страница 57: ...19 ELECTRONIC CIRCUIT DIAGRAM CS CU PC9CKV CS PC9CKV CU PC9CKV 57 CS PC9CKV CU PC9CKV CS PC12CKV CU PC12CKV ...
Страница 58: ...CS PC9CKV CU PC9CKV 58 CS PC9CKV CU PC9CKV CS PC12CKV CU PC12CKV ...
Страница 60: ...CS PC9CKV CU PC9CKV CS PC12CKV CU PC12CKV 60 CS PC9CKV CU PC9CKV CS PC12CKV CU PC12CKV ...
Страница 61: ...How to use electronic circuit diagram TIMER TABLE 61 CS PC9CKV CU PC9CKV CS PC12CKV CU PC12CKV ...
Страница 62: ...19 2 PRINT PATTERN INDOOR PCB CS PC9CKV CS PC12CKV 62 CS PC9CKV CU PC9CKV CS PC12CKV CU PC12CKV ...
Страница 63: ...CS PC9CKV CS PC12CKV 63 CS PC9CKV CU PC9CKV CS PC12CKV CU PC12CKV Printed in China ...