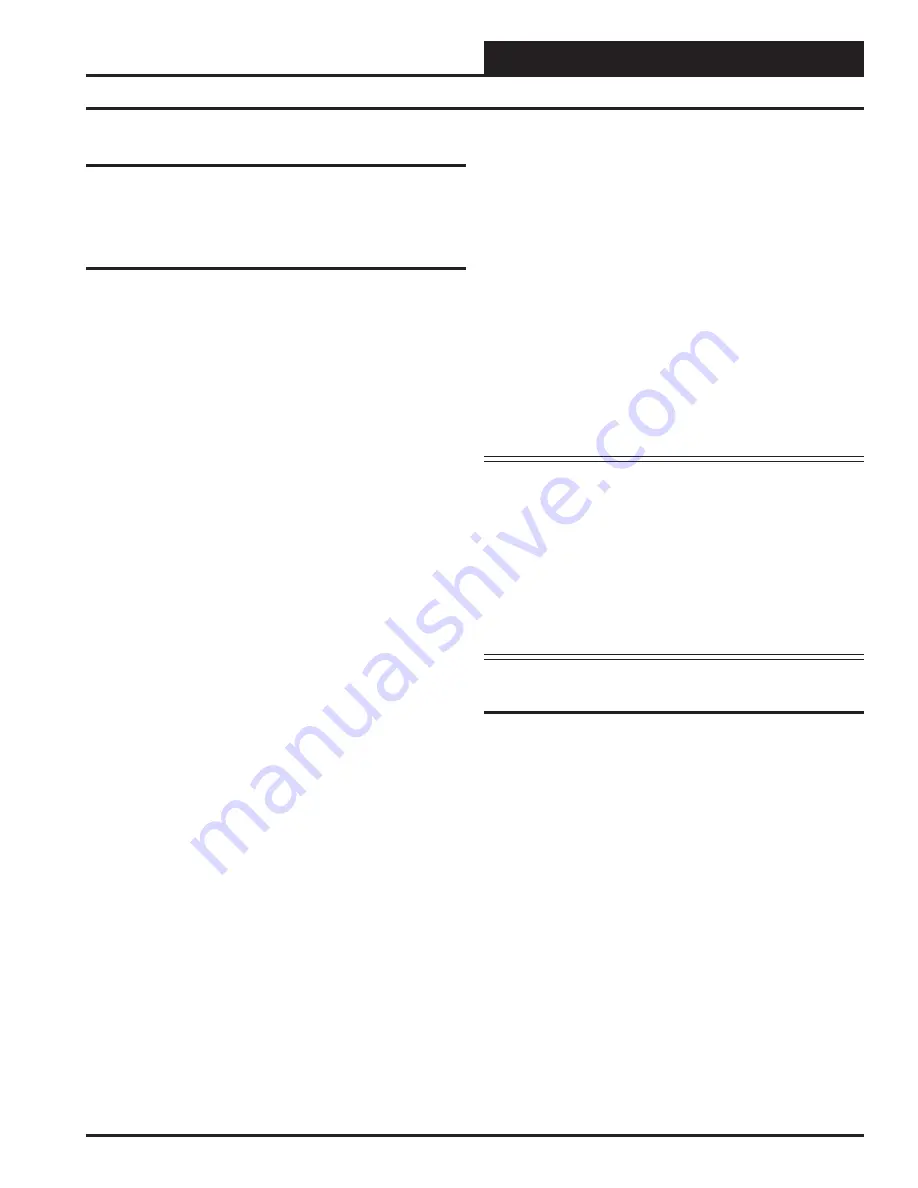
Controller Installation & Wiring
General
Correct wiring of the VAV/Zone Controller is the most important factor
in the overall success of the controller installation process. The VAV/
Zone Controller wiring has been simplified by the use of modular con
-
nectors and prefabricated modular cables.
Controller Mounting
If you purchased the Round Zone Damper or Rectangular Zone Damper
Kits from WattMaster, the controller and actuator are factory mounted
and wired in the damper control enclosure. If your VAV/Zone Control-
lers are pressure independent, an airflow probe and pressure sensor will
also be factory mounted and wired.
Most terminal unit manufacturers will offer the option of factory mount-
ing the Orion controls in their terminal units for an additional charge.
An installation worksheet and instructions are available for the Orion
VAV/Zone Controller package which can be shipped with the VAV/Zone
control(s) to the terminal unit manufacturer to simplify factory mounting
and wiring of the controller.
When the Non-Modular VAV/Zone Controller Actuator Package is to be
field mounted, it is important to mount it in a location that is free from
extreme high or low temperatures, moisture, dust, and dirt.
1. Leave the enclosure cover on the Non-Modular VAV/Zone
Controller Actuator Package circuit board during installation
to protect the circuit board from damage. The damper actuator
is factory mounted for what we refer to as right-hand terminal
unit mounting. This assumes you are standing downstream of
the terminal unit with air hitting you in the face. The side of the
unit towards your right arm would be the right side of the unit
and where the standard configuration Zone Controller Actuator
Package would be mounted over the damper shaft. If you have a
left-hand terminal unit, the actuator will need to be rotated 180
degrees within the plastic enclosure and the enclosure assembly
flipped over to mount over the damper shaft on the left side of
the terminal unit. The enclosure base is designed with the appro-
priate holes and cutouts to allow for these two mounting options.
A left-hand label is also included with the actuator and can be
applied over the right-hand label for left-hand control locations
when desired.
2. If you need to rotate the damper actuator from its factory
supplied position, first unplug the actuator cable from the actua
-
tor, then remove the (3) screws on the back side of the enclosure
base that secure the actuator to the enclosure’s base. Rotate
the actuator 180 degrees and re-install the (3) screws you just
removed into the mating holes on the enclosure base and tighten
them to secure the actuator to the base.
3. Turn the enclosure base/actuator assembly back over to its
original mounting position so the actuator is facing up. All instal-
lation instructions are based on the damper moving clockwise to
open (see the note below if your damper requires counterclock
-
wise-to-open rotation). Check the damper for proper rotation and
mark the end of the damper shaft to indicate open and closed
positions. Loosen the (2) shaft mounting bracket nuts on the
ends of the universal mounting clamp enough to slide the entire
actuator and plastic enclosure assembly over the terminal unit
damper shaft. Rotate the enclosure base/actuator assembly until
it is approximately level and perpendicular with the terminal
unit mounting surface or enclosure side walls. Use the included
self-tapping mounting screw to secure the enclosure base to the
terminal unit sheet metal or terminal unit control enclosure sur-
face. This is done by inserting the screw through the anti-rotation
bushing, centering it and the bushing in the mounting slot, and
using a battery powered drill to tighten it until the screw head
is flush with the top surface of the anti-rotation bushing. Do not
over tighten the screw!
4. Turn the damper blade to its fully closed position. With the man-
ual override clutch button depressed, rotate the actuator clamp
to within approximately
1
/
16
in. to ⅛ in. of the distance between
the actuator stop and the clamp. This varies depending on the
damper seal design and thickness. Finger-tighten the universal
clamp mounting nuts. Then tighten the two nuts again with an
8 millimeter wrench to approximately 3-5 ft./lb. of torque. On
dampers with edge seals, the actuator will compress the damper
blade seal when reaching the end position. Adjust the end stops,
if required. Re-attach the actuator cable removed in step #1 to
the actuator.
Note:
If the damper on the terminal unit cannot be installed for
clockwise-to-open operation, the Non-Modular VAV/
Zone Controller Actuator Package can be configured for
counterclockwise-to-open operation via the operator in-
terface or through the Prism software program. It must be
changed prior to system start-up for the designated units
for the zone damper to function properly.
See page 19
of this manual for detailed, reverse acting configuration
information. Installation for reverse acting configurations
is the same as for clockwise-to-open units except all refer-
ences to clockwise will now be in the counter-clockwise
direction.
Important Wiring Considerations
Please carefully read and apply the following information when wiring
the Non-Modular VAV/Zone Controller Actuator Package.
See
Figure
7
for Non-Modular VAV/Zone Controller Actuator Package wiring and
connections.
See Figure 14
for connecting and wiring multiple Non-
Modular VAV/Zone Controller Actuator Packages in a system.
1. Size and wire the transformer to be used for powering the Non-
Modular VAV/Zone Controller Actuator Package(s) per the
instructions. Failure to size the transformer and/or wire the Non-
Modular VAV/Zone Controller Actuator Package(s) correctly
may cause the VAV/Zone Controller Actuator Package to operate
erratically or not at all. See
Figure 15
for wiring and transformer
sizing information.
2. If a Supply Air Temperature Sensor is to be connected, the
minimum wire size used should be 24 gauge.
3. Do not pry on the connectors when connecting or
disconnecting the modular cables. Be sure to push in on the
connector release clip and then pull straight up.
4. Communications wiring should be 18 gauge 2 conductor twisted
pair with shield Belden #82760 or its equivalent. This type of
wire is available form WattMaster.
9
Non-Modular ZCAP Technical Guide
Installation & Wiring