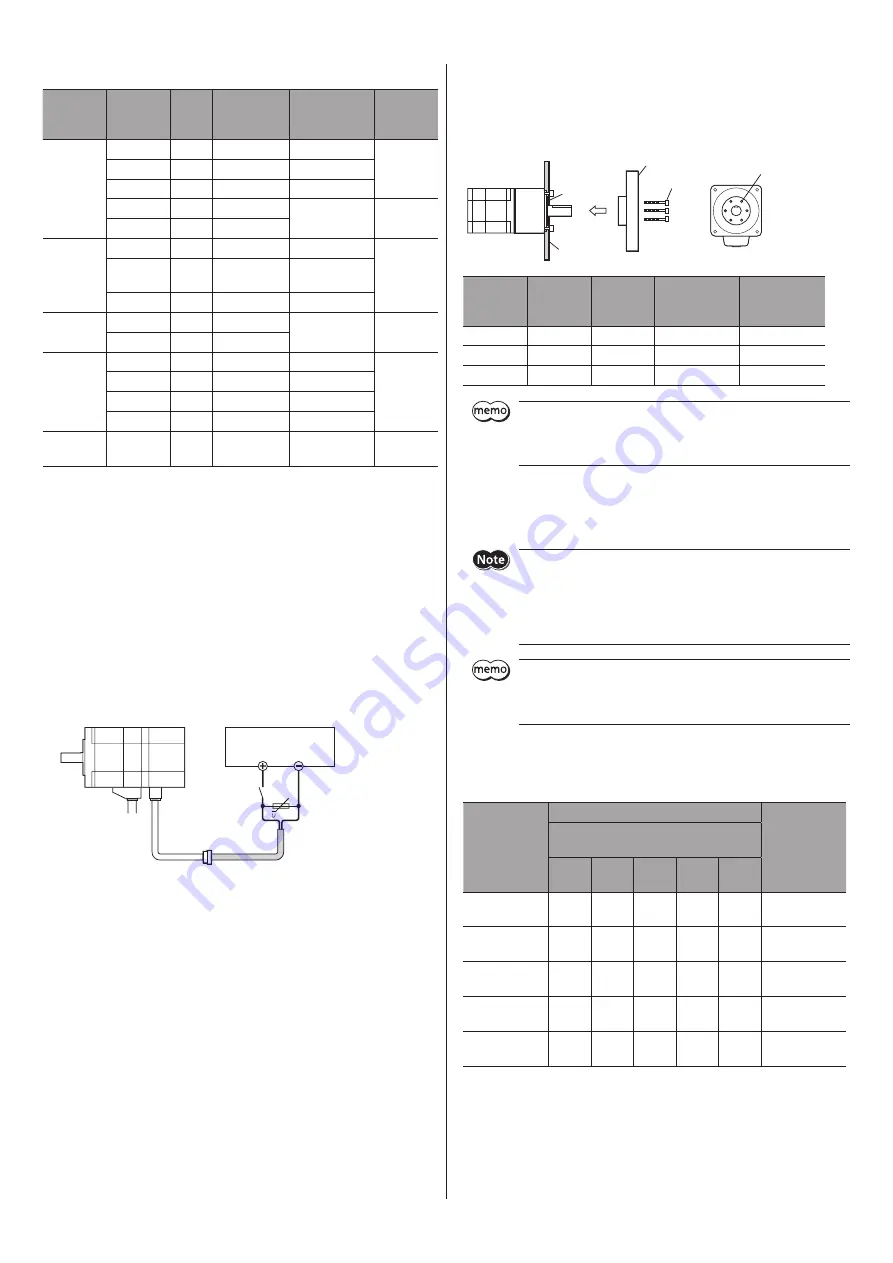
5
Nominal size, tightening torque, and installation method
Type
Motor
frame size
[mm (in.)]
Screw
size
Tightening
torque
[N·m (oz-in)]
Effective depth
of screw thread
[mm (in.)]
Installation
method
Standard
20 (0.79)
M2
0.25 (35)
2.5 (0.098)
A
28 (1.10)
M2.5
0.5 (71)
2.5 (0.098)
42 (1.65)
M3
1 (142)
4.5 (0.177)
60 (2.36)
M4
2 (280)
−
B
85 (3.35)
M6
3 (420)
TH
geared
28 (1.10)
M2.5
0.5 (71)
4 (0.157)
A
42 (1.65)
60 (2.36)
M4
2 (280)
8 (0.315)
90 (3.54)
M8
4 (560)
15 (0.591)
FC
geared
42 (1.65)
M4
2 (280)
−
B
60 (2.36)
M5
2.5 (350)
PL
geared
PS
geared
PN
geared
Harmonic
geared *1
28 (1.10)
M3
1 (142)
6 (0.24)
A
42 (1.65)
M4
2 (280)
8 (0.315)
60 (2.36)
M5
2.5 (350)
10 (0.394)
90 (3.54)
M8
4 (560)
15 (0.591)
Harmonic
geared *2
90 (3.54)
M8
4 (560)
−
B
*1
ARM24
,
ARM46
, and
ARM66
only.
*2
ARM98
only.
Installing a load
When installing a load to the motor, align the centers of the motor output
shaft and load shaft. Be careful not to damage the output shaft or the
bearings (ball bearings) when installing a coupling or pulley to the motor
output shaft.
z
Electromagnetic brake motor
To release the electromagnetic brake and install the load, a DC power
supply is needed to power the electromagnetic brake. Use a cable for
electromagnetic brake to connect a DC power supply of 24 VDC to the motor.
Black
White
Varistor *3
Switch
24 VDC±5% *2
Cable for electromagnetic
brake
Electromagnetic brake motor
DC power supply for
electromagnetic brake *1
*1 The power supply current capacities are as follows.
ARM24
,
ARM26
: 0.05 A or more
ARM46
: 0.08 A or more
ARM66
,
ARM69
,
ARM98
: 0.25 A or more
*2 If the distance between the motor and driver is extended to 20 m (65.6 ft.) to
30 m (98.4 ft.), use a power supply of 24 VDC±4%.
*3 Provide a varistor to protect the contact of the switch or to prevent electrical
noise. It is included with the electromagnetic brake motor of DC power input
type.
[Recommended varistor: Z15D121 (SEMITEC Corporation)].
z
Installing on the flange surface (Harmonic geared type)
With a Harmonic geared type (excluding
ARM98
), a load can be installed
directly to the gear using the load mounting holes provided on the flange
surface.
Metal plate
Frange
Screws
Load
Load mounting
holes
Motor
model
Screw size
Number of
screw
Tightening
torque
[N·m (oz-in)]
Effective depth
of screw thread
[mm (in.)]
ARM24
M3
4
1.4 (198)
4 (0.157)
ARM46
M3
6
1.4 (198)
5 (0.2)
ARM66
M4
6
2.5 (350)
6 (0.24)
y
When installing a load on the flange surface, the load cannot be
mounted using the key slot in the output shaft.
y
Design an appropriate installation layout so that the load will not
contact the metal plate or screws used for installing the motor.
Permissible radial load, permissible axial load, and
permissible moment load
y
If the radial load or axial load exceeds the specified allowable value,
repeated load applications may cause the bearing (ball bearings) or
output shaft of the motor to undergo a fatigue failure.
y
With a double shaft type, do not apply load torque, radial load, or
axial load to the output shaft on the opposite side of the motor
output shaft.
The permissible radial load and permissible axial load of the
PS
geared
type and
PN
geared type represent the value that the service life of
the gear part satisfies 20,000 hours when either of the radial load or
axial load is applied to the gear output shaft.
z
Permissible radial load, permissible axial load
•
Standard type
Motor model
Permissible radial load [N (lb.)]
Permissible axial
load [N (lb.)]
Distance from the tip of motor output shaft
[mm (in.)]
0
(0)
5
(0.2)
10
(0.39)
15
(0.59)
20
(0.79)
ARM14
ARM15
12
(2.7)
15
(3.3)
−
−
−
3 (0.67)
ARM24
ARM26
25
(5.6)
34
(7.6)
52
(11.7)
−
−
5 (1.12)
ARM46
35
(7.8)
44
(9.9)
58
(13)
85
(19.1)
−
15 (3.3)
ARM66
ARM69
90
(20)
100
(22)
130
(29)
180
(40)
270
(60)
30 (6.7)
ARM98
ARM911
260
(58)
290
(65)
340
(76)
390
(87)
480
(108)
60 (13.5)