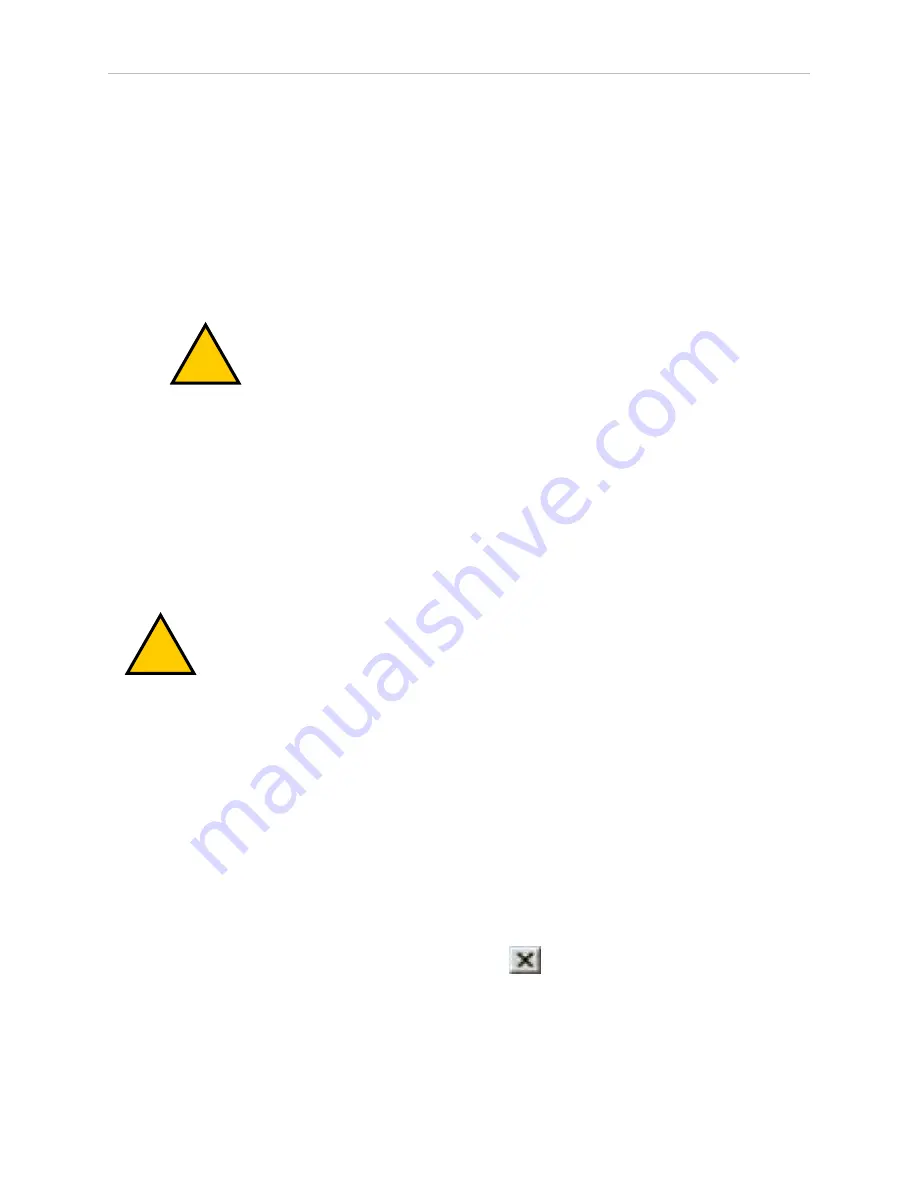
32
SmartController EX User's Guide
11069-000 Rev. H
4.3 Installing the ACE Software
a. Manual Mode
b. Auto Mode
4.
High Power ON / OFF Switch & Lamp
Controls high power, which is the flow of current to the robot motors. Enabling high
power is a two-step process. An Enable Power request must be sent from the user ter-
minal, an executing program, or a pendant. Once this request has been made, the button
light blinks, and the operator must press the button for high power to be applied. The
default timeout for the button is 10 seconds.
!
WARNING:
Disabling the High Power button violates IEC 60204-1. It is
strongly recommended that you not alter the use of the High Power but-
ton.
5.
Emergency Stop Switch
The E-Stop is a dual-channel, passive E-Stop that supports Category 3 PL-d per EN ISO
13849 safety requirements. It maintains motor power for a fixed time after the E-Stop is
activated. This feature allows the motors to decelerate under servo control to a stop.
This can aid in eliminating coasting or overshooting on low friction mechanisms. It can
also aid in the reduction of wear on highly-geared, high-inertia mechanisms, while
maintaining safety compliance per all standards.
4.3 Installing the ACE Software
!
WARNING:
Make sure that all cables are installed correctly and fully inserted
and screwed down before applying power to the system. Failure to do this
could cause unexpected robot motion. Also, a connector could be pulled out or
dislodged unexpectedly.
To begin the installation:
1. Insert the ACE software media into your PC.
l
If AutoPlay is enabled, the Welcome to ACE menu is automatically displayed.
l
If AutoPlay is disabled, you will need to manually start the installation media.
Use Windows Explorer to browse to the installation media, right-click on the
drive, and select AutoPlay from the menu.
2. Click
Read Important Information
. The ReadMe file is displayed.
3. Verify that your system meets the minimum requirements described in the System
Requirements section.
4. After reviewing the information, click the close icon (
) in the upper-right corner of
the ReadMe file window to close it.
Содержание SmartController EX
Страница 1: ...I602 E 03 SmartController EX User s Guide ...
Страница 6: ......
Страница 8: ...8 SmartController EX User s Guide 11069 000 Rev H 1 1 Product Description Figure 1 2 T20 Pendant ...
Страница 10: ......
Страница 14: ......
Страница 58: ......
Страница 71: ......