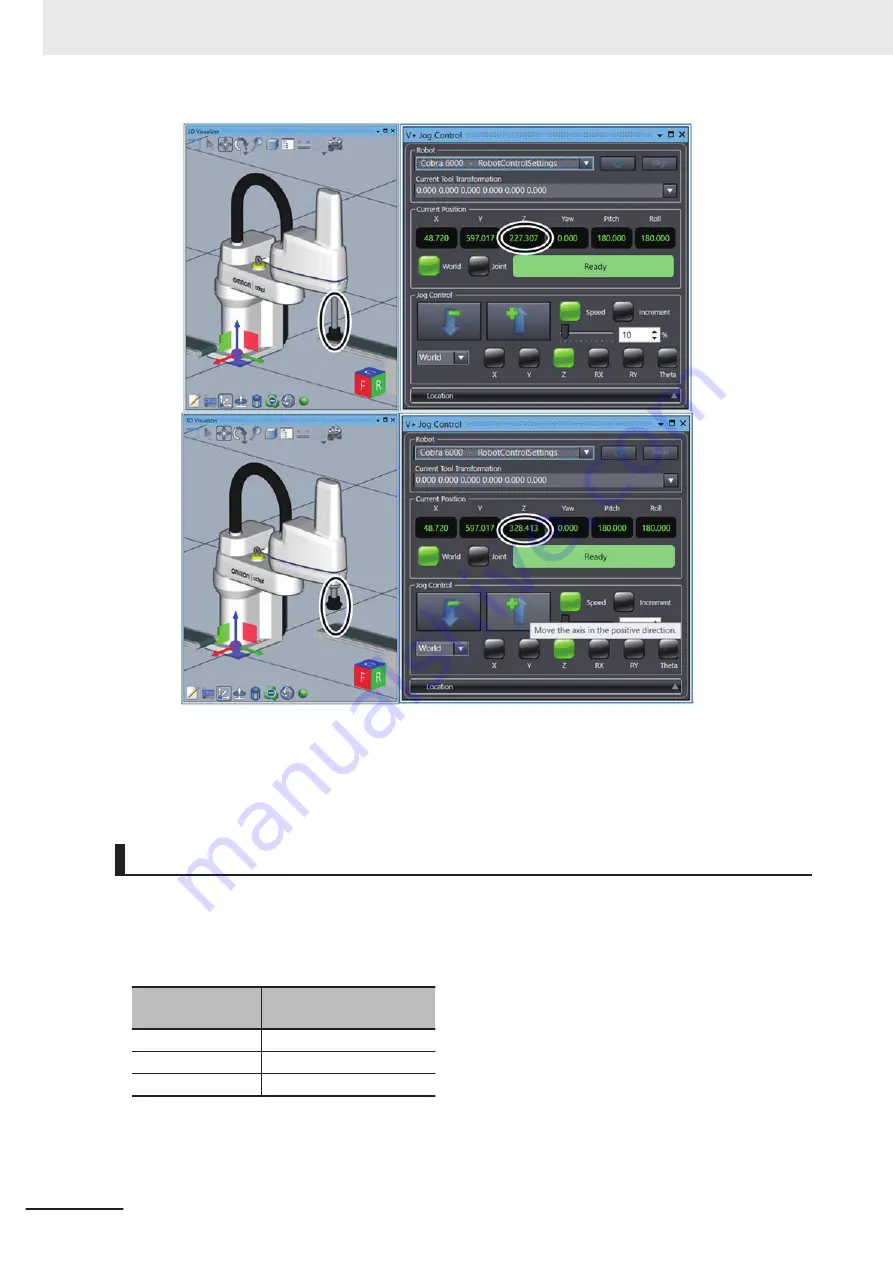
7
Take step 4 to 6 again to move the robot to the position and posture you want to specify.
Now the robot position has been configured.
Saving Current Positions to Variables
The current positions of the robot set by teaching must be saved in the V+ variables.
The procedure to save the current position of the robot to the already created V+ variable is described
below.
V+ position variables that need to be saved are listed in the table below.
Name of position
(Name of variable)
Description
gl.wait
Robot wait position
gl.pick
Workpiece pick-up position
gl.place
Workpiece place position
Save a current position to the variable
gl.wait
as an example. Save current positions to two other vari-
ables in the same manner.
3 Implementation Example of Static Pick-and-place Equipment
3-64
NJ-series Robot Integrated System Startup Guide (O049)
Содержание RL4 Series
Страница 4: ...AC1 152000 Introduction 2 NJ series Robot Integrated System Startup Guide O049 ...
Страница 12: ...A 3 Using Troubleshooting Functions A 22 CONTENTS 10 NJ series Robot Integrated System Startup Guide O049 ...
Страница 23: ...Outline View Detailed View Versions 21 NJ series Robot Integrated System Startup Guide O049 ...
Страница 30: ...Revision History 28 NJ series Robot Integrated System Startup Guide O049 ...
Страница 42: ...1 Overview 1 12 NJ series Robot Integrated System Startup Guide O049 ...
Страница 50: ...2 Before You Begin 2 8 NJ series Robot Integrated System Startup Guide O049 ...
Страница 144: ...3 Implementation Example of Static Pick and place Equipment 3 94 NJ series Robot Integrated System Startup Guide O049 ...
Страница 162: ...Appendices A 18 NJ series Robot Integrated System Startup Guide O049 ...
Страница 164: ...Appendices A 20 NJ series Robot Integrated System Startup Guide O049 ...
Страница 167: ......