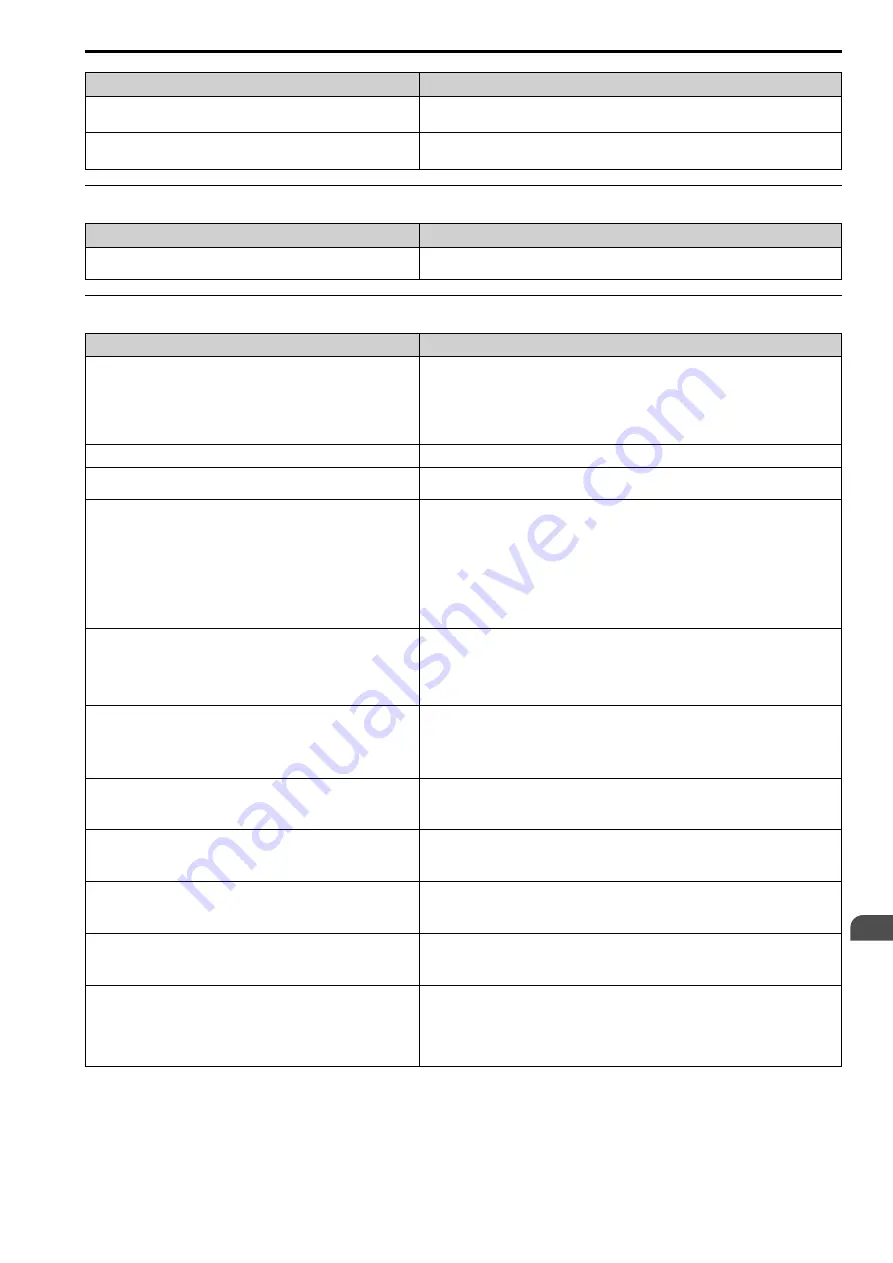
7.10 Troubleshooting Without Fault Display
SIEPCYEUOQ2V01A Q2V Technical Manual
261
Causes
Possible Solutions
The air around the motor is too hot.
•
Measure the ambient temperature.
•
Decrease the temperature in the area until it is in the specified temperature range.
The motor fan stopped or is clogged.
•
Clean the motor fan.
•
Make the drive environment better.
◆
The Correct Auto-Tuning Mode Is Not Available
Causes
Possible Solutions
The desired Auto-Tuning mode is not available for the selected control
mode.
Change the motor control method with parameter
A1-02 [Control Method]
.
◆
The Motor Stalls during Acceleration or Accel/Decel Time Is Too Long
Causes
Possible Solutions
The drive and motor system are at the torque limit or current suppression
will not let the drive accelerate.
•
Decrease the load.
•
Use a larger motor.
Note:
Although the drive has a Stall Prevention function and a Torque Compensation Limit
function, if you try to accelerate too fast or try to drive a load that is too large, it can be too
much for the limits of the motor.
Torque limit is set incorrectly.
Set the torque limit correctly.
The acceleration time setting is too short.
Examine the values set in
C1-01, C1-03, C1-05, or C1-07 [Acceleration Time]
and set them to
applicable values.
The load is too large.
•
Increase the acceleration time.
•
Examine the mechanical brake and make sure that it is fully releasing.
•
Decrease the load to make sure that the output current stays less than the motor rated current.
•
Use a larger motor.
Note:
•
In extruder and mixer applications, the load can increase as the temperature decreases.
•
Although the drive has a Stall Prevention function and a Torque Compensation Limit
function, if you try to accelerate too fast or try to drive a load that is too large, it can be too
much for the limits of the motor.
The frequency reference is low.
•
Examine
E1-04 [Max Output Frequency]
and increase the setting if it is set too low.
•
Examine
U1-01 [Frequency Reference]
for the correct frequency reference.
•
Examine the multi-function input terminals to see if a frequency reference signal switch is set.
•
When you use an MFAI, examine the low gain level set in
H3-03, H3-11 [AI1 Gain Setting,
AI2 Gain Setting]
.
The frequency reference is set incorrectly.
When
H3-10 = 5 [AI2 Function Selection = Freq Gain]
, see if the drive is set for voltage
(current).
•
Examine the value set in
H3-10
.
•
Use
U1-14 [Terminal AI2 InputLv]
to make sure that the analog input value set to terminal
AI2 is applicable.
The motor characteristics and drive parameter settings are not compatible.
•
Set the correct V/f pattern to agree with the characteristics of the motor.
•
Examine the V/f pattern set in
E1-03 [V/f Pattern Selection]
.
•
Do Rotational Auto-Tuning.
The drive is operating in vector control mode, but you did not complete
Auto-Tuning.
•
Do Auto-Tuning.
•
Calculate motor data and reset motor parameters.
•
Set
A1-02 = 0 [Control Method = V/f Control]
.
The Stall Prevention level during acceleration setting is too low.
Increase the value set in
L3-02 [StallP Level@Accel]
.
Note:
If the
L3-02
value is too low, the acceleration time can be unsatisfactorily long.
The Stall Prevention level during run setting is too low.
Increase the value set in
L3-06 [StallP Level@Run]
.
Note:
If the
L3-06
value is too low, speed will decrease before the drive outputs torque.
The drive is at the limit of the V/f motor control method.
•
When the motor cable is longer than 50 m (164 ft), do Auto-Tuning for line-to-line resistance.
•
Set the V/f pattern to
“
High Starting Torque
”
.
•
Use a Vector Control method.
Note:
V/f control method does not supply high torque at low speeds.
Содержание Q2V Series
Страница 2: ...This Page Intentionally Blank 2 SIEPCYEUOQ2V01A Q2V Technical Manual...
Страница 12: ...12 SIEPCYEUOQ2V01A Q2V Technical Manual...
Страница 18: ...i 2 Legal Information 18 SIEPCYEUOQ2V01A Q2V Technical Manual...
Страница 26: ...1 2 Features and Advantages of Control Methods 26 SIEPCYEUOQ2V01A Q2V Technical Manual...
Страница 38: ...2 8 Installation Methods 38 SIEPCYEUOQ2V01A Q2V Technical Manual...
Страница 70: ...3 3 Main Circuit Wiring 70 SIEPCYEUOQ2V01A Q2V Technical Manual Models B006 B012...
Страница 102: ...3 17 Motor Application Precautions 102 SIEPCYEUOQ2V01A Q2V Technical Manual...
Страница 138: ...4 12 Test Run Checklist 138 SIEPCYEUOQ2V01A Q2V Technical Manual...
Страница 143: ...Standards Compliance 5 5 2 European Standards SIEPCYEUOQ2V01A Q2V Technical Manual 143 EU Declaration of Conformity...
Страница 144: ...5 2 European Standards 144 SIEPCYEUOQ2V01A Q2V Technical Manual...
Страница 145: ...Standards Compliance 5 5 2 European Standards SIEPCYEUOQ2V01A Q2V Technical Manual 145...
Страница 146: ...5 2 European Standards 146 SIEPCYEUOQ2V01A Q2V Technical Manual...
Страница 266: ...7 10 Troubleshooting Without Fault Display 266 SIEPCYEUOQ2V01A Q2V Technical Manual...
Страница 284: ...8 6 Storage Guidelines 284 SIEPCYEUOQ2V01A Q2V Technical Manual...
Страница 312: ...10 10 Peripheral Devices and Options 312 SIEPCYEUOQ2V01A Q2V Technical Manual...
Страница 430: ...11 21 Parameters Changed by PM Motor Code Selection 430 SIEPCYEUOQ2V01A Q2V Technical Manual...
Страница 731: ...SIEPCYEUOQ2V01A Q2V Technical Manual 731 Z Z pulse Auto Tuning 125...
Страница 733: ...SIEPCYEUOQ2V01A Q2V Technical Manual 733...