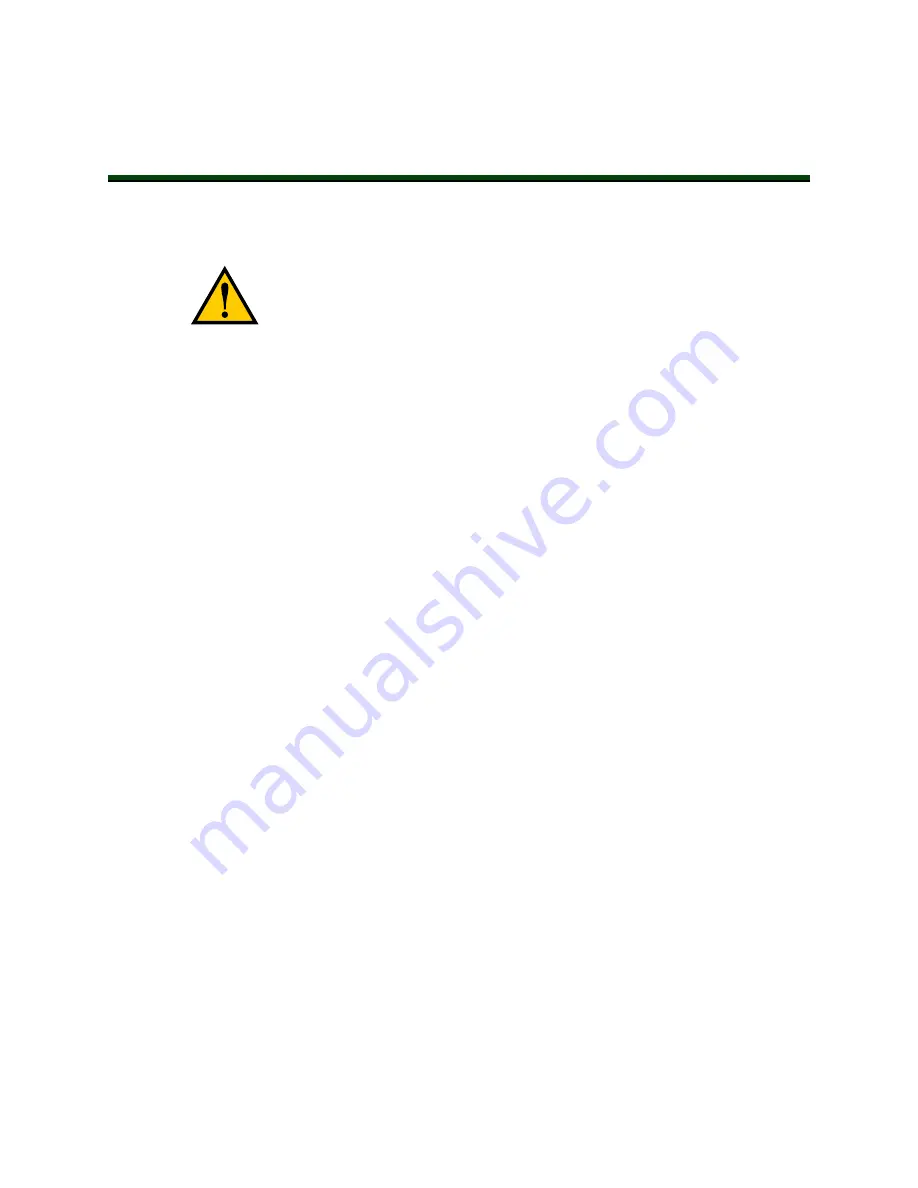
Chapter 3: Setup
Battery Safety Information
CAUTION:
Possible battery damage. Immediately charge the battery to a full
charge after receipt to avoid the risk of discharging the battery below a usable
state, which would require battery replacement.
Effective April 1, 2016, IATA regulations (UN 3480, PI 965) require that air-shipped lithium ion
batteries must be transported at a state of charge not exceeding 30%. To avoid total discharge,
fully charge the battery immediately upon receipt.
NOTE:
If the battery was not sent by air, it may be fully-charged.
Safety Precautions
l
Store batteries upright at:
n
One month: +5 to 45°C (41 to 113°F)
n
One year: 20 to 25°C (68 to 77°F)
l
Never expose the battery to water. If the battery is leaking, submerge in mineral oil and
contact your local Omron Support.
l
In case of fire, use a type D extinguisher: foam, dry chemical, or CO
2
.
Maintenance
Every six months:
l
Inspect battery for damage or leaks.
l
Place battery on a charger and allow to fully balance (battery shows all solid LEDs
when fully balanced).
Overview
In general, setup is the physical and logical preparation of the platform, configuration of the
wireless network, and the installation of the docking station. The physical preparation of the
platform includes attaching your payload structure to the platform.
Setup also includes generating the map the platform will use for navigation. This manual
provides an overview of that process, which is covered in detail in the
Mobile Robot Software
Suite User's Guide
.
11970-000 Rev H1
LD Platform OEM User's Guide
25
Содержание LD Platform
Страница 1: ...I611 E 02 LD Platform User s Guide...
Страница 8: ......
Страница 37: ...Chapter 3 Setup Figure 3 15 E Stop Jumper on LD Platform Core 11970 000 Rev H1 LD Platform OEM User s Guide 37...
Страница 44: ......
Страница 70: ...70 LD Platform OEM User s Guide 11970 000 Rev H1 6 2 Payload Bay Connections Figure 6 7 E Stop Chain Diagram...
Страница 98: ......
Страница 130: ......
Страница 139: ......