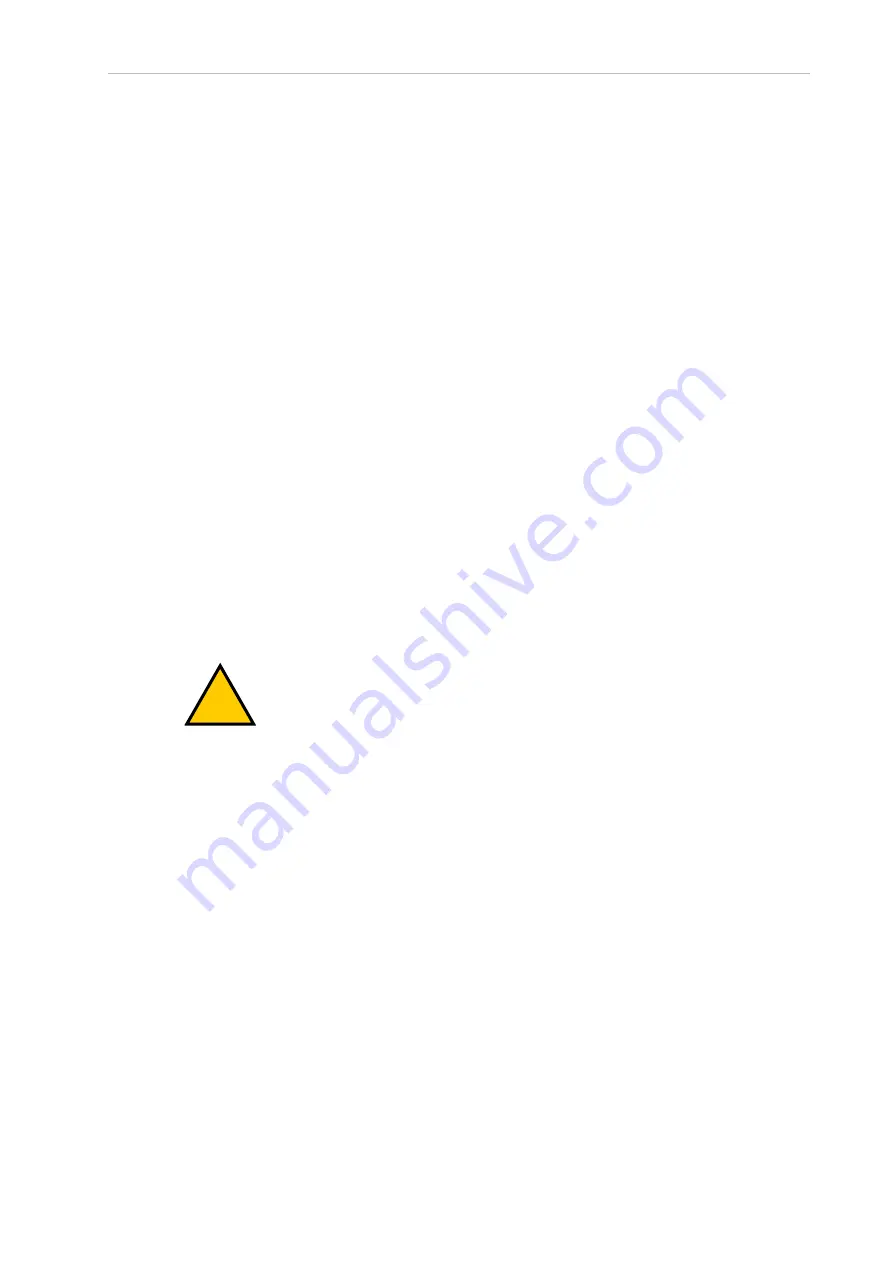
Chapter 3: Robot Installation
Robot Orientation
We recommend mounting the robot so that the Status Display Panel faces away from a con-
veyor belt (when present). Although the work envelope of the robot is symmetrical, this ori-
entation gives better access to the status display. It also orients the arm loading for aggressive
moves across the belt. This orientation places the robot World Y-axis along the conveyor belt,
and the X-axis across the belt.
Mounting Surfaces
The mounting frame should have 3 mounting tabs that provide a mounting surface for the
robot. These mounting tabs will be mated to the robots mounting pads. Use the following con-
siderations when designing the mounting tabs.
l
The 3 mounting tabs should be aligned to a flat, horizontal plane with a maximum of
0.75 mm parallelism deviation. Exceeding this allowance will cause inconsistent robot
move positioning.
l
If welding mounting tabs to the frame, this should be done as a last step in the con-
struction process to ensure parallelism to a flat, horizontal plane.
l
Consider using a flat surface as a datum during the construction of mounting tabs.
Refer to Robot Physical Dimension Drawings on page 119 for more information.
NOTE:
The robot base-mounting pads have spring-lock Heli-Coils in the M12
holes, so lock washers are not needed on the M12 mounting bolts.
Mounting Procedure
Use the following procedure to mount the iX3 robot.
!
WARNING:
PERSONAL INJURY OR PROPERTY DAMAGE RISK
Do not attempt to lift the robot from any points other than with slings as
described in the mounting procedure.
NOTE:
The shipping pallet will not fit inside most frames, so the robot will
need to be manually moved to the inside of the frame.
1. Position the robot directly under the mounting frame.
2. Put adequately sized straps through the six lifting slots near the three mounting pads.
The following figure shows two of these slots.
22792-000 Rev. A
iX3 565 Robot with EtherCAT User’s Manual
35