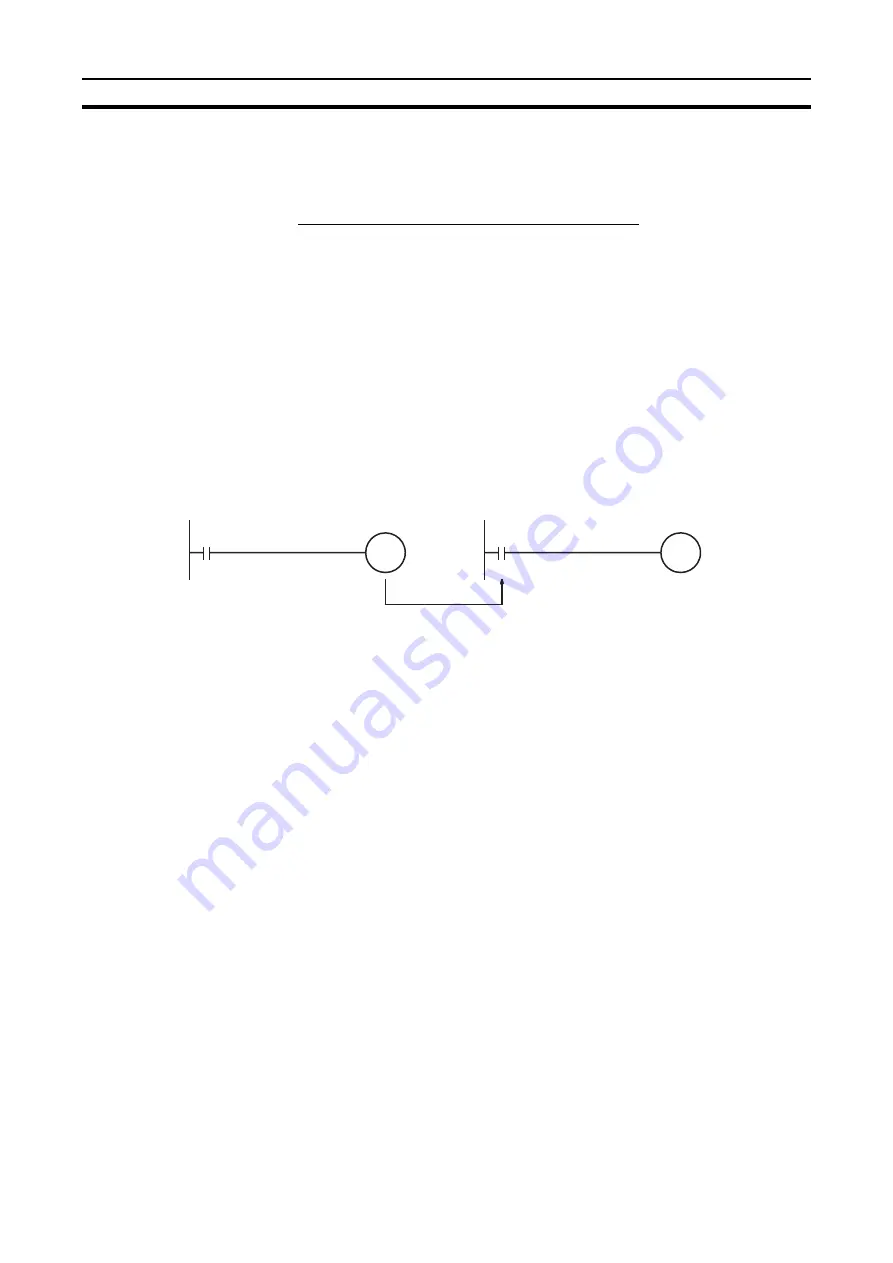
156
One-to-one PC Link I/O Response Time
Section 7-4
Maximum Response Time
(Except for the Online Editing of DM 6144 to DM 6655)
Interrupt ON delay:
50
µ
s
Interrupt mask standby time:
150
µ
s
+
Change-to-interrupt processing:
10
µ
s
Maximum response time:
210
µ
s
In addition to the response time shown above, the time required for executing
the interrupt processing routine itself and a return time of 10
µ
s must also be
accounted for when returning to the process that was interrupted.
7-4
One-to-one PC Link I/O Response Time
When two CPM2C-S PCs are linked 1:1, the I/O response time is the time
required for an input executed at one of the PCs to be output to the other PC
by means of 1:1 PC Link communications.
The minimum and maximum I/O response times are shown here, using as an
example the following instructions executed at the master and the slave. In
this example, communications proceed from the master to the slave.
The following conditions are taken as examples for calculating the I/O
response times. In CPM2C-S PCs, LR area words LR 00 to LR 15 are used in
1:1 data links and the transmission time is fixed at 12 ms.
Input ON delay:
10 ms (input time constant: default setting)
Master cycle time:
10 ms
Slave cycle time:
15 ms
Output ON delay:
15 ms
Minimum I/O Response
Time
The CPM2C-S responds most quickly under the following circumstances:
1,2,3...
1.
The CPM2C-S receives an input signal just prior to the input refresh phase
of the cycle.
2.
The Master’s communications servicing occurs just as the Master-to-Slave
transmission begins.
3.
The Slave’s communications servicing occurs just after the transmission is
completed.
Input
Output (LR)
Input
(LR)
Output
Master
Slave
Содержание CPM2C-S100C
Страница 2: ......
Страница 3: ...CPM2C S Programmable Controller Operation Manual Revised September 2009 ...
Страница 4: ...iv ...
Страница 6: ...vi ...
Страница 10: ......
Страница 14: ...xiv ...
Страница 180: ...158 One to one PC Link I O Response Time Section 7 4 ...
Страница 222: ...200 Programming Example Section 8 3 ...
Страница 250: ......
Страница 256: ......
Страница 258: ......
Страница 260: ...238 Support Software Appendix C ...
Страница 268: ......