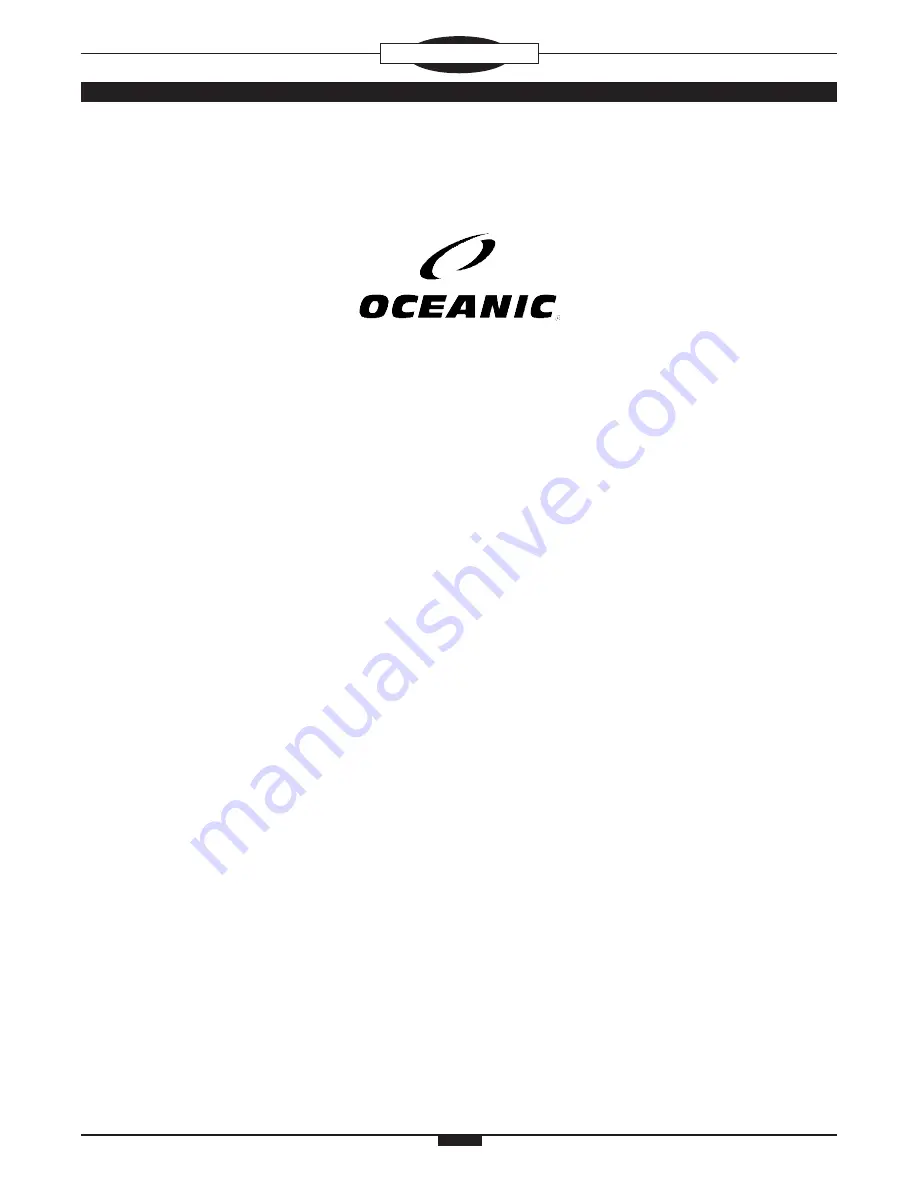
REGULATORS
DELTA II SECOND STAGE
© 2002 Design 1997
OCEANIC® Product Service Guide
Doc. 12-2223-r03 (10/3/10)
PG-1
R = Revision
DELTA 2
SERVICE
PROCEDURE
This Delta-2 Product Service Procedure conveys a list of components and service pro-
cedures that reflect the Delta-2 as it was configured at the time of this writing (10/3/10).