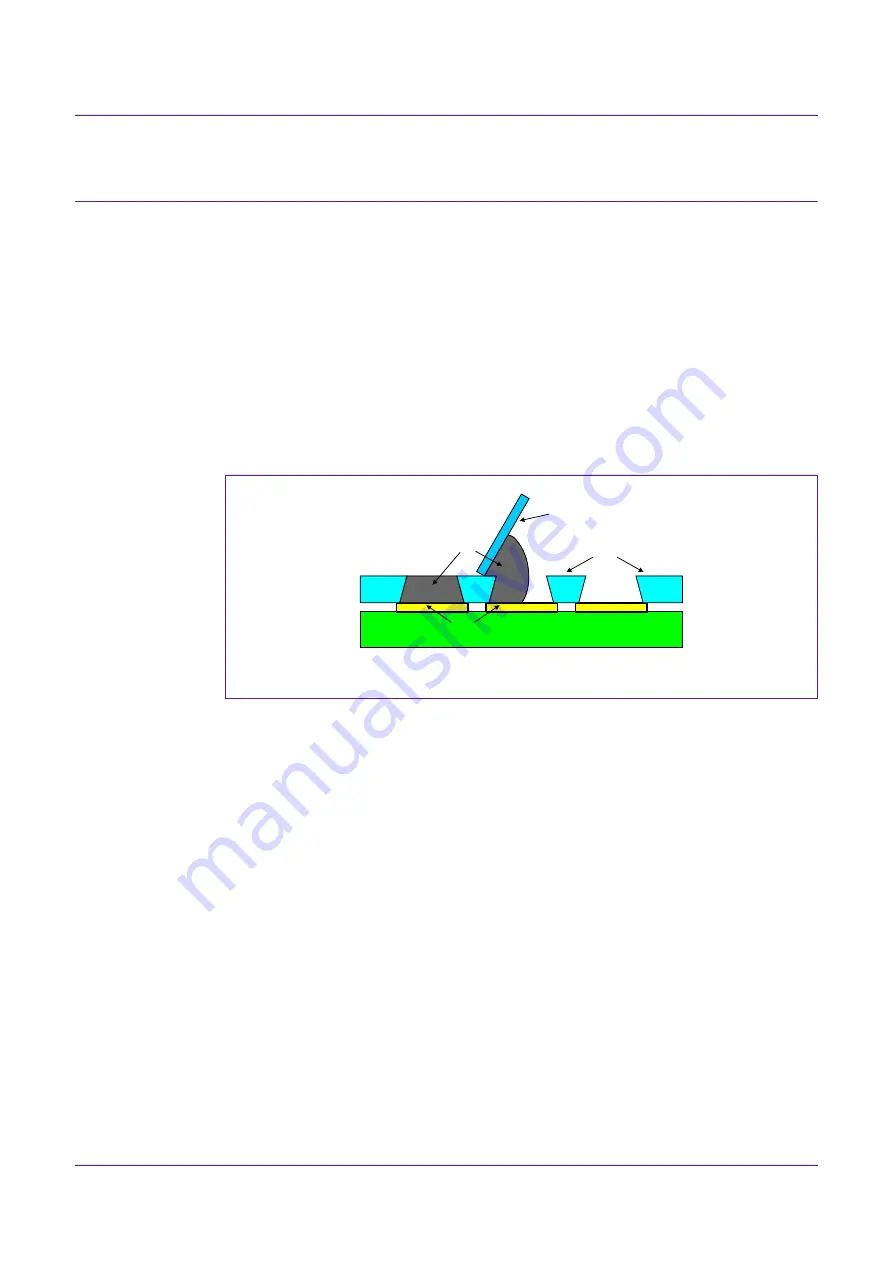
AN10365_3
© NXP B.V. 2008. All rights reserved.
Application note
Rev. 03 — 22 April 2008
12 of 24
NXP Semiconductors
AN10365
Surface mount reflow soldering description
4.
Surface mounting process
4.1 Solder paste printing
Solder paste printing requires a stencil aperture to be completely filled with paste. Then,
when the board is released from the stencil, the solder paste is supposed to adhere to the
board, so that all of the paste is released from the stencil aperture, and a good solder
paste deposit remains on the board. Ideally, the volume of solder paste on the board
should equal the ‘volume’ of the stencil aperture.
In practice, however, not all of the solder paste is released from the stencil aperture. The
percentage of paste release depends largely on the aperture dimensions, i.e. the length
and width and the depth (the stencil thickness). If a stencil aperture becomes very small,
the paste will no longer release completely. Furthermore, stencil apertures must be larger
if a thicker stencil is used.
Another important factor is the aperture shape, i.e. whether the aperture is rectangular,
trapezoidal, or otherwise. Paste release also depends - amongst others - on the loading
and speed of the squeegee, the board separation speed, the printing direction, and the
aperture orientation. In essence, all of these parameters must be adjusted so that all
solder paste deposits on one board, from the smallest to the largest, are printed properly.
Consequences of insufficient solder paste printing are usually open contacts or bad joints.
These may arise because:
•
The solder paste deposit is not sufficiently high: components or their leads may not
make proper contact with the paste, resulting in open circuits or bad joints, or
•
There is insufficient solder volume for a proper solder joint, also resulting in open
circuits, or
•
The activator is used up rapidly in a small solder paste deposit, so that the paste no
longer properly wets the component metallization, also resulting in open circuits
A second important aspect in solder paste printing is smearing. If some solder paste
bleeds between the stencil and the board during one printing stroke, then the next board
may not fit tightly to the stencil, allowing more paste to bleed onto the bottom of the
stencil. Once this effect starts, it strengthens itself. As a result, the solder paste may
eventually form bridges that stretch from one paste deposit to the next. If a bridge is
Fig 11. Stencil printing
001aac840
board
pad
squeegee
stencil
solder
paste