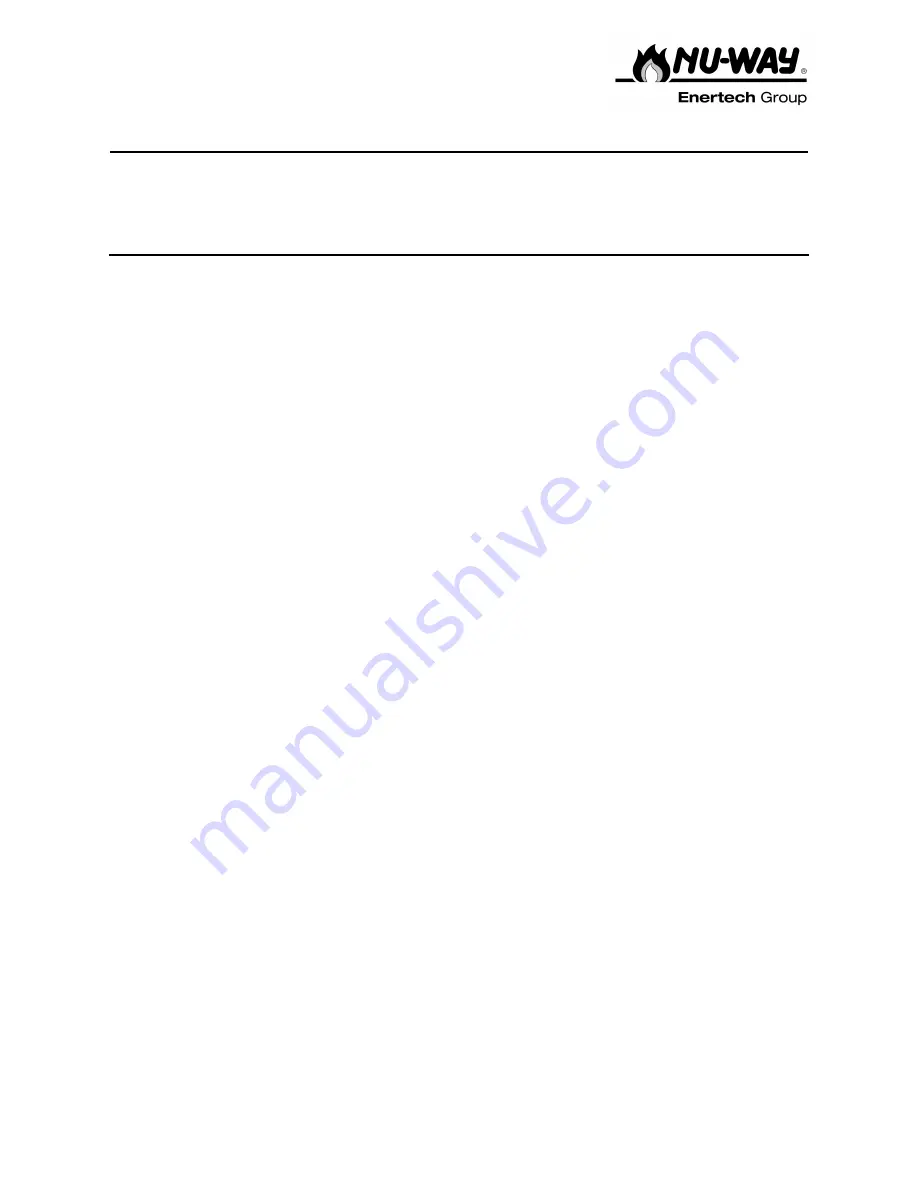
Installation - Maintenance
MULTIPLEX
blown gas burner
The MP burner range of compact industrial packaged gas burners covers outputs up to 150 therms, using a
very stable “nozzle-mixing” combustion head and is suitable for use on Natural, LPG or Towns Gas (type must
be specified at time of ordering). They are suitable for firing a wide range of industrial applications.
The control system and components used in conjunction with the MULTIPLEX burner should be in accordance
with BS5885 and recommendations and codes of practice set out by BRITISH GAS where the equipment is for
use in the UK, and to the relevant authority in other countries.
The instructions given by NU-WAY assume that these conditions have been met by the plant manufacturers
and/or installers. For general data see Multiplex Data Sheet.
BURNER MOUNTING AND COMBUSTION TUNNEL RECOMMENDATIONS
The MULTIPLEX burner would normally be provided with one of three tunnel options. The mounting
requirements external to the combustion chamber would hold for all three options. The internal requirements
will however vary and guidance for mounting is given. Nu-way will advise on any mounting problems you may
have and make recommendations on choice of tunnel materials if required.
External Mounting
All burners are provided with a mounting flange which is pre-drilled to dimensions given on the data sheet.
Combustion chamber fire hole should be required dimensions (See dimensions in Data Sheet).
Screwed studs or alternative fixings should be provided on burner flange holes centres.
Burner may be mounted to chamber in any one of the four available mounting positions provided by the
mounting flange.
When the burner is mounted to the furnace front withdrawal distance equal to the overall length of the burner
including combustion tunnel should always be allowed at the rear of the burner unit.
Gas pipework into the burner should be such as to include an elbow and union connection to ensure freedom of
removal of internal parts of the burner for service. Care should be exercised in assembly of the gas pipework to
ensure electrode extensions are not damaged. Care should be taken to ensure that it seats evenly and
squarely to the chamber. A gasket, gasket rope or furnace cement should be used to prevent leakage.
page 1
SERIES
MP