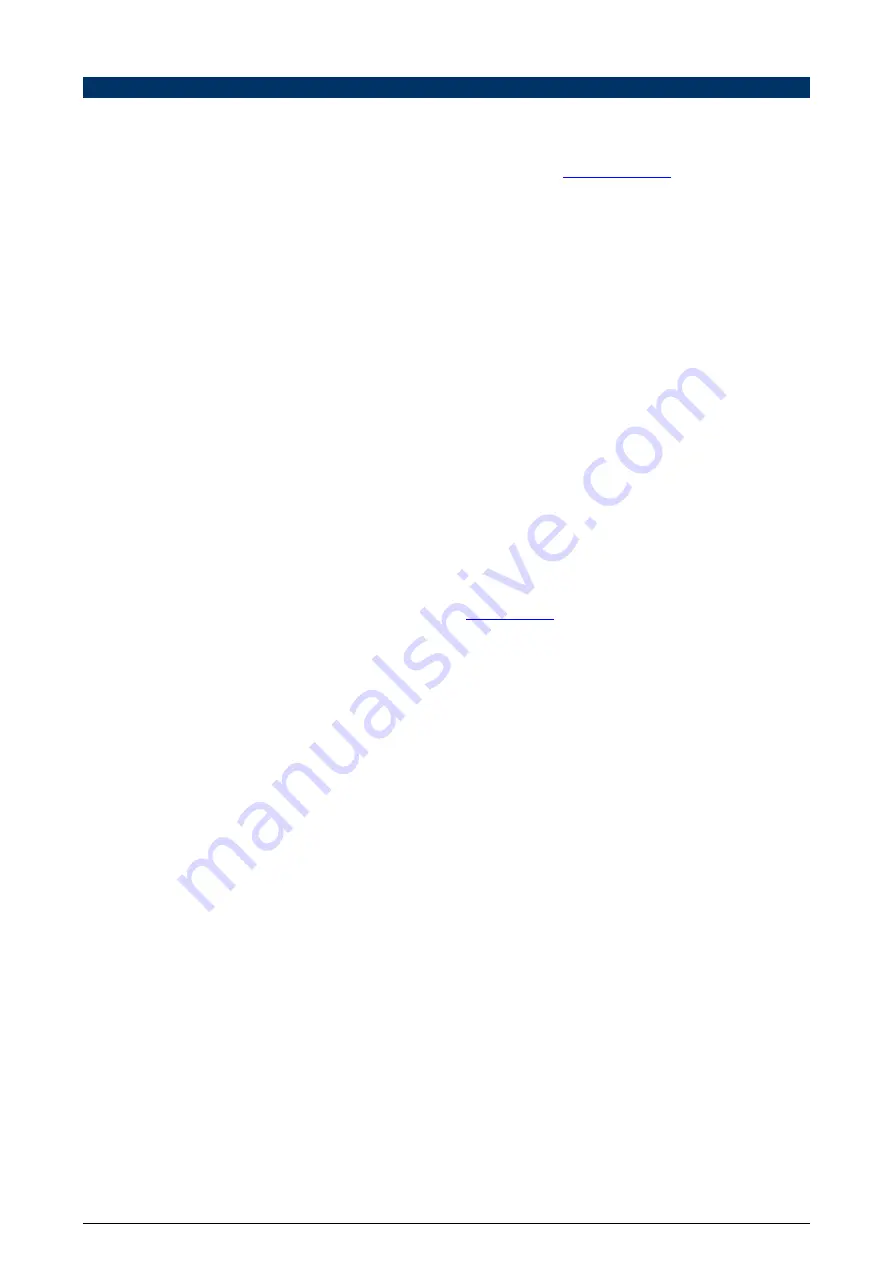
NOVUS AUTOMATION
10/25
5
SETTINGS
NP785 Ultra Low Differential Pressure Transmitter
is configurable by any of its interfaces. Due to the ease of use of the interface, it is
recommended to configure via USB using the
NXperience
software, but the device can also be configured via Modbus RTU by writing directly in
their configuration registers.
The description of the device registers, together with the configuration tables, can be found in the
5.1
GENERAL SETTINGS
The differential pressure value is obtained by counting the digital analog converter of the device internal sensor. It is possible to select any of the
following pressure units: mbar, mpsi, inH2O, mmH2O or Pa. Changing this setting reverts the transmission limits and alarm setpoints to the default
values, which are the operation limits of the device.
The device also features
Auto-Zero
and
Offset
functions and an internal digital filter to process the measured signal.
You can use the
Auto-Zero
function to correct small differences in the sensor read value with no differential pressure applied, caused by mounting,
device position or natural variations of the sensor over time. You can use the
Auto-Zero
function by pressing the
Auto-Zero
key for another 2
seconds or by using the
NXperience
software. If the pressure value read is within the allowable limits, the pressure reading will be reset to zero.
You can also use the software to determine if the
Auto-Zero
function will reset the Offset value.
You can set an
Offset
value, which will be described in the selected pressure unit, to make small adjustments to the output value. The digital filter,
in turn, allows you to set the 1st order filter time constant (in seconds). This helps to reduce the occurrence of noise effects and pressure peaks at
the expense, however, of a faster response.
It is recommended to run the
Auto-Zero
function after changing the configuration of the device.
It is also possible to configure the parameters of Modbus RTU communication, such as Baud Rate, parity, and slave address of the device.
To differentiate between units of the same model, you can set an identifier on the device.
For test purposes, the device allows forcing the measurement of differential pressure, analog output, and alarm output. For each of these cases,
you can configure a value to be forced and enable or disable forcing.
5.2
ALARM SETTINGS
NP785 Ultra Low Differential Pressure Transmitter
has a digital alarm output. The digital output will be activated whenever an alarm situation is
satisfied, except cases defined by some of its settings.
You can configure the alarm operation mode, high and low setpoints, hysteresis value, status transition timers, error condition and initial blocking.
Alarm configuration can be performed through the
NXperience
software (see
section), allowing different operation modes:
•
Off:
No alarm situation is active.
•
Sensor Error:
While there is some error reading the sensor, the alarm output will remain on.
•
Below Lower Setpoint:
The alarm output will be activated when the current pressure is lower than the lower setpoint. To exit the alarm
condition, the differential pressure must be greater than the lower setpoint plus the hysteresis value.
•
Above Higher Setpoint:
The alarm output will be activated when the differential pressure is higher than the upper setpoint. To exit the alarm
condition, the differential pressure must be lower than the lower setpoint minus the hysteresis value.
•
Intra-range:
The alarm output will be activated when the differential pressure is higher than the lower set point and lower than the upper set
point. To exit the alarm condition, the differential pressure must be greater than the upper setpoint plus the hysteresis value or lower than the
lower setpoint minus the hysteresis value.
•
Extra-range:
The alarm output will be activated when the differential pressure is higher than the setpoint higher or lower than the lower
setpoint. To exit the alarm condition, the differential pressure must be less than the upper setpoint minus the hysteresis value and higher than
the lower setpoint plus the hysteresis value.
In addition to the alarm operation modes, other parameters, which do not apply to the Sensor Error mode, can be configured to refine the behavior
of the alarm output:
•
Initial Blocking:
This parameter determines the use of the alarm output lock soon after the device is started. After initialization, a non-alarm
condition is required for the alarm output to be enabled.
•
Error Condition:
The status of this parameter determines whether the alarm output will remain on or off in case of sensor failure.
•
Hysteresis:
This parameter stores the pressure value that, with the values of the set points, determines the limit value to leave the alarm
situation.
Figure 07
shows the conditions for alarm activation and deactivation.
The alarm output can be timed by means of the
Time On
and
Time Off
parameters. For a given status transition to occur, the device must remain
in the new status for a period equal to the one configured in the respective transition parameter. These values are initialized to 0 by default.
Extra-range
mode is the default mode of alarm output. The default values of the set points, in turn, are the operating limits of the device. Any
changes in the pressure unit configuration readjust the values of the set points to the operating limits.