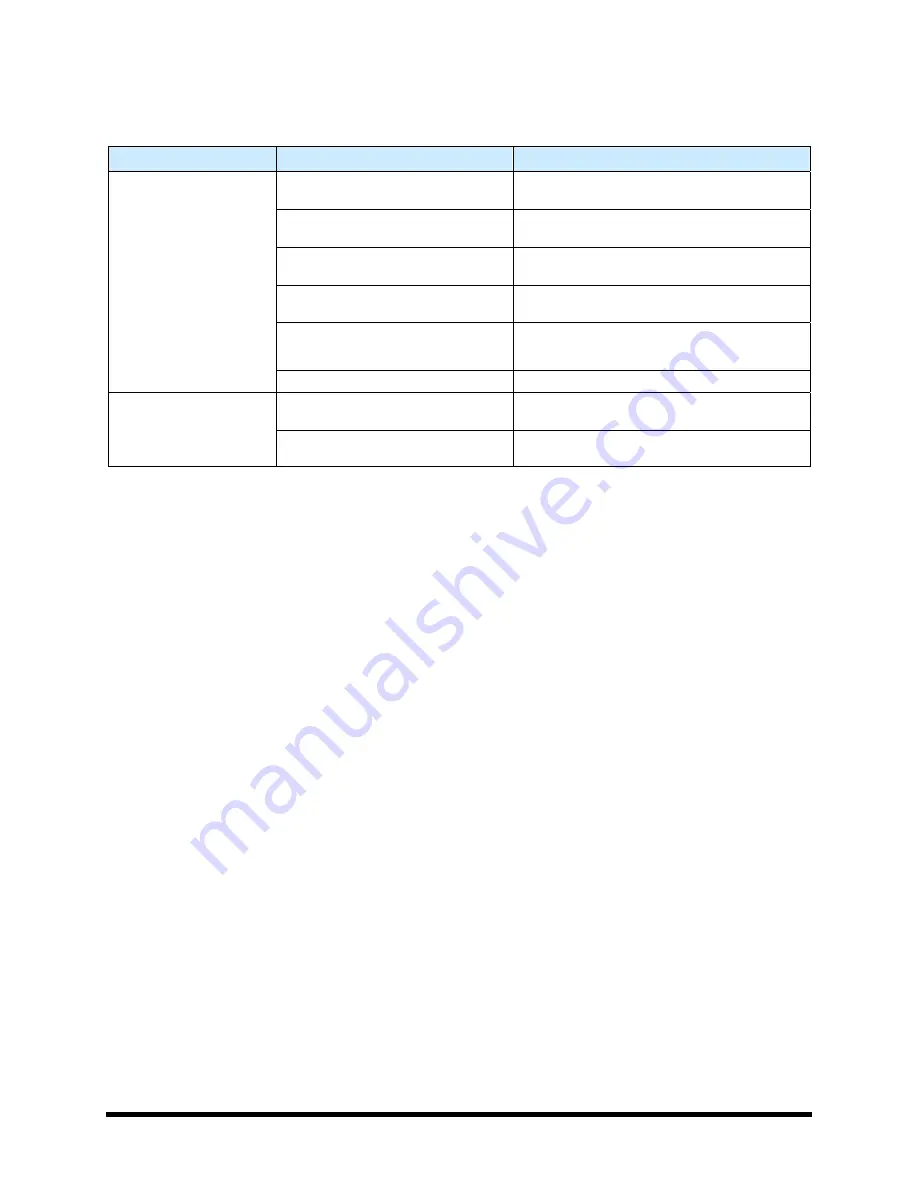
Troubleshooting
8-3
8.4.2 System
Accuracy
Table 8-2 System Accuracy
Symptom
Possible Cause
Recovery Procedures
Loose camera lens
Bad offset routines
Perform a Valve Offsets Routine. See
Camera needs calibrated
Cal Maps disabled
Enable Cal Maps. Contact a service
technician.
Bent needle
Replace the needle. Refer to the applicable
valve manual.
Inaccurate dispensing
Bad height sensor
Contact Asymtek Technical Support.
Loose camera lens
Fiducials not found
Corrupted vision file
Re-teach the vision targets or entire program
as necessary.
Содержание Asymtek Spectrum S-920
Страница 1: ...Spectrum Series S 920 Dispensing System Installation Operations Maintenance Manual P N 7212417 Rev A...
Страница 2: ......
Страница 4: ......
Страница 30: ...1 14 Introduction 1 10 5 Rear View Figure 1 7A Rear View 2 3 4 1 5...
Страница 124: ......
Страница 172: ...7 12 Maintenance Figure 7 7 Lubricating the X Axis Linear Guides Figure 7 8 Lubricating Y Axis Linear Guides...
Страница 185: ...Troubleshooting 8 11 Figure 8 3 FmXP Scale Setup Menu Figure 8 4 Scale Error Message...
Страница 190: ......
Страница 204: ......
Страница 208: ......
Страница 210: ......
Страница 220: ......
Страница 222: ......
Страница 223: ......
Страница 224: ......
Страница 225: ......
Страница 226: ......
Страница 234: ......