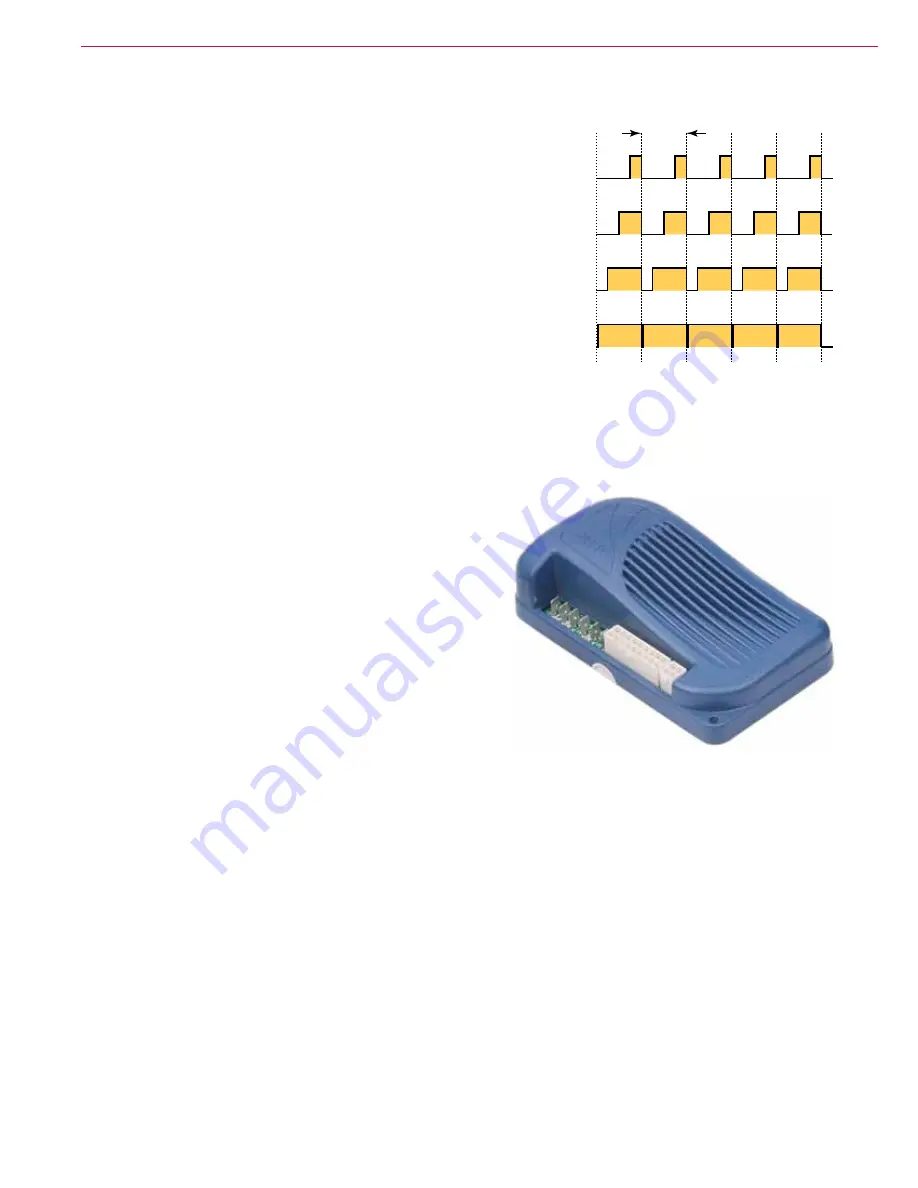
15
20 - Wheel System, Traction
Drive Motor PWM Function
The drive motor is controlled from a Curtis 1228 controller, which is
a pulse-width-modulation speed controller designed specifically for
permanent magnet DC motors Pulse-width-Modulation (PWM) is a form
of motor speed control that alters the power to a motor by rapidly turning
the power on and off The ratio (also called “duty cycle”) between the
On and Off states determines how much power the motor receives The
shorter the “off-time” the closer to full power the motor will receive This
switching occurs so fast (15kHz for this controller) that the motor simply
sees it as a reduction in power (voltage) instead of the rapid on/off PWM
is a standard motor control technique because it is easier to turn power
all the way on and all the way off, than it is to vary the magnitude of the
power Varying the magnitude would create a lot of heat that would need
to be dissipated
Drive Controller
The primary purpose of the drive controller is, of course, to control the drive motor However, it also provides
some ancillary control of the other functions of the machine, which will be discussed in greater detail in the
applicable chapters As a motor controller, it delivers PWM-varying power to the drive motor in both positive
and negative polarities for forward and reverse motor operation
Even though the machine does not utilize an
electromechanical brake system, the drive controller
possesses the output control for one Instead, this is used for
ancillary machine control, specifically, the scrub functions.
As used by this machine, the Brake output from the drive
controller is more aptly referred to as a “Scrub Enable”
function The brake outputs (or “Scrub Enable”) are active
only when the drive is commanded for movement In this
manner, when the machine is stopped, the scrub motor,
solution solenoid, and detergent pump circuits are all
disabled The Brake+ output is always 36 volts as long as
they keyswitch is on, and the Brake- output is switched to
ground when the machine is commanded to move
The controller is powered directly from the batteries, but through a 30-amp circuit breaker The drive
controller remains inactive (inhibited) until the KSI input receives positive battery power through the main
key switch When KSI is active, the drive is ready to operate, and awaiting a throttle command to move
25% PWM Duty Cycle
50% PWM Duty Cycle
75% PWM Duty Cycle
100% PWM Duty Cycle
1-Cycle
(15kHz)