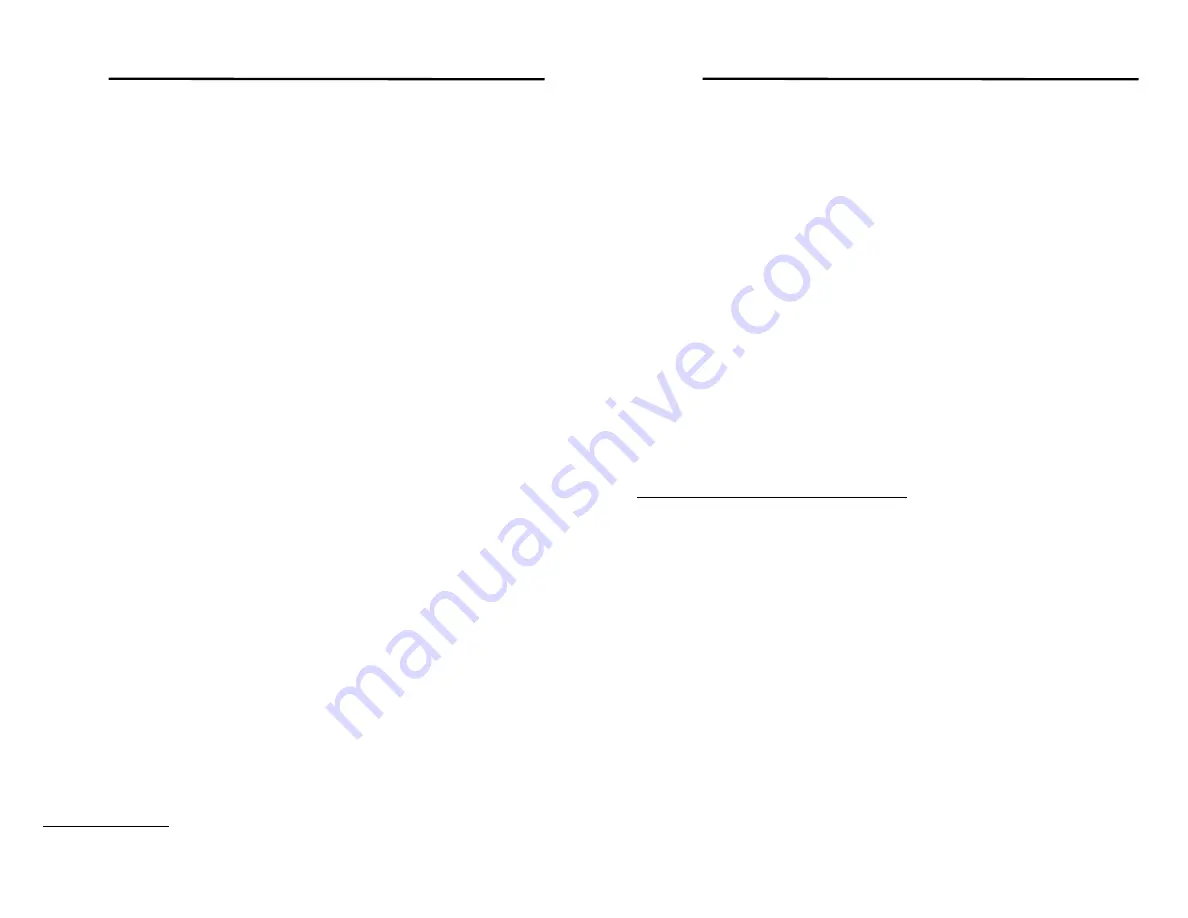
Nova Eclipse TG950 - Users Manual
34
6. GAGING TIPS AND TECHNIQUES
6.1 Reference Standards
The more closely the reference standard matches the actual test material,
the better the gaging accuracy. For metals, to compensate for variations
such as composition, microstructure, heat-treat condition, grain direction,
thickness range, surface roughness and geometry, the ideal reference
material would be samples produced from pieces of the actual material to
be tested. This type of reference standard is used for critical applications
requiring maximum gaging accuracy.
For many applications, satisfactory gaging accuracy can be obtained by
using a single reference sample. This sample should have the same
composition and geometry as the actual test object. Reference standard
thicknesses should be measured using a micrometer or similar device to
accurately establish known thicknesses. If a thickness range is anticipated,
use a reference sample that represents the thicker end of the range.
Machined stepped-wedges having thickness steps across the range of
interest can frequently be used provided they are of the same general
composition as the test material. Experimentation with known thicknesses
of the test objects is recommended.
W hen gaging thin materials that approach the lower performance limits of
the gage/probe combination, experiment with reference samples to
determine the actual lower limit. Do not attempt to gage materials thinner
than this limit. See
Very Thin Sections
in
Section 7, Gaging
Precautions
, below.
For exceptionally large thickness ranges, particularly in alloys where
microstructure variations can occur, use separate samples and calibration
setups at selected intervals across the range.
Many wrought and cast metal microstructures exhibit directionality,
depending upon the beam direction, that causes a slight variation in
ultrasonic velocity. For improved accuracy, reference samples should have
the same directionality/sound beam orientation as that of the material to be
gaged.
6.2 Test Surface and Geometry Considerations
Surface Condition:
Prior to gaging, remove performance-hindering foreign
Nova Eclipse TG950 - Users Manual
35
substances from the material surface; e.g.: dirt, loose scale, corrosion, soil,
flaking paint.
Excessive surface roughness can cause erratic, extremely low, or no
thickness readout. In such cases, consider scraping, sanding, grinding or
filing the surface smooth enough to obtain a proper response (provided
such a procedure and the amount of material removal are acceptable).
A uniformly-grooved surface, such as that produced by a single-point
cutting tool can also produce erroneous readings. As a possible remedy,
orient the probe's cross-talk barrier (located on the bottom of the probe) at
right angles to the groove pattern direction.
For either surface condition, first try using a high-viscosity couplant.
Adjusting the receiver gain may also remedy the problem. Use the GAIN
control located in the MAIN menu. The Hi-Power Probe (TG-208) may also
significantly improve the response.
For gaging thick materials or materials with large grain structures, consider
using a lower frequency probe such as the TG-208 Hi-Power Probe.
Surface Geometry - Cylindrical Shapes:
For gaging on cylindrical shapes
such as pipe, tubing, small diameter tanks, etc., it is vital to establish probe
normality (perpendicularity to surface) and to select the proper orientation of
the probe's cross-talk barrier.
To determine normality, rock the coupled probe back and forth along the
curved direction on the material surface and observe the accompanying
decrease/increase action of the thickness readout. Use the minimum
thickness reading, as this represents probe normality.
The cross-talk barrier is the thin material that splits the bottom of the probe
into halves (its direction is marked on both sides of the probe housing). The
cross-talk barrier orientation depends upon the test object’s surface
diameter. See the following probe orientation Figure. On large diameters,
orient the probe so its barrier is perpendicular to the cylindrical axis of the
test object. On smaller diameters, orient the probe barrier both
perpendicular to, and parallel with, the test object’s cylindrical axis (at the
identical location). Use the orientation that yields the lesser thickness
readout.